Tips for Getting the Most Out of Your Digital Multimeter
Modern digital multimeters (DMMs) are user-friendly, accurate, and safe — when used correctly! Reading voltage is simple, but measurements must be properly interpreted. With a clamp-on DMM, accurate current flow readings are obtained if you follow the tricks of the trade. Resistance measurements are easy if you know what you are measuring (see “Make Sure Your DMM Does What You Need It to Do,” below). Following are tips for measuring voltage, current, and resistance for safe and effective DMM use.
Tips to interpret the voltage measurement
Follow all safety precautions, set up the DMM, and place the test leads on the test points. The number appearing on the meter face is the voltage difference between those two points. However, that number may not be what you think it is.
Set the DMM for the correct voltage.
A simple error is failing to set the meter function switch to the appropriate voltage type (AC or DC). Experienced techs will quickly catch their mistake and change to the switch. New technicians, while learning to use their meter, may just be confused and proceed in the wrong direction. Make sure you know whether the circuit is AC or DC, and set the meter accordingly.
Use a true-rms DMM when applicable.
Reading voltage values in electronic circuits, such as variable-frequency drives (VFDs), uninterruptible power supply (UPS) systems, battery chargers, and any distribution system supplying significant electronic loads, requires the use of a “true-rms” meter rather than an “average-responding” DMM. An average responding meter reads the root mean square value (rms) of a pure sine wave. Due to the countless electronic devices in distribution systems today, many such systems are made up of distorted sine waves. These distorted waves can produce voltage readings as much as 40% low and high on average responding DMMs. Electronic loads produce high-frequency noise and harmonics that distort the non-sinusoidal readings. Low-pass filters are designed into DMMs to block high-frequency noise. Use the correct type of DMM on these circuits, or expect inaccurate readings (Photo 1).
Be aware of voltage drop.
When measuring voltage values in distribution systems, do not expect to read nominal system voltage — the voltage found on the transformer nameplate. Voltage drops due to long conductor runs and equipment operations occur. Intermittent problems and overheating may occur. If a coil in a relay or motor starter drops to approximately 70% to 80% of the rated voltage, the relay will continually drop and pick back up creating a chattering sound. Motors will tend to draw more current at lower voltages, creating overheating problems. Understand the concept and effects of voltage drop to effectively troubleshoot your system.
Watch for DMM loading in electronic circuits.
DMMs have high input impedance when set to voltage, thus preventing the meter from acting as a load on the circuit. While not a problem when reading distribution system voltages, measuring values in electronic circuits can be different. Modern DMMs generally have sufficient input impedance, preventing any appreciable amount of current flow through the DMM. Ensure the meter meets the proper specifications when working with electronics.
Tips for clamp-on ammeter use
The clamp on the clamp-on DMM senses the strength of the magnetic field around a conductor created by current flow. Increasing current flow increases the strength of this field and thus an increased amperage reading on the meter. Grasping this basic concept helps us understand the tips for using the clamp-on DMM.
Clamp around only one wire.
The direction of the electromagnetic field developed around a conductor depends upon the direction of the current flow through the wire. The clamp on the DMM (whether a part of the meter design or an accessory for the meter) senses this magnetic field developed around the wire. As current flows through one conductor of a circuit, it returns on an opposite conductor. Thus, the magnetic fields developed around each of these conductors would be in opposite directions. If both conductors are placed inside the clamp at the same time, the magnetic fields will cancel each other, and the field sensed by the clamp will be zero, thus the DMM would indicate zero amperes when, in fact, there is current flow through the circuit (Photo 2).
Three-phase motor circuits can be tricky as well. If the current is flowing out to the source on one ungrounded conductor, then it is flowing back on the other two phase conductors at the same time. Since the three conductors are out of phase with each other, clamping around two of the three phases will provide a very inaccurate and useless reading. Clamping around all three of the phases would show zero amperes on the DMM once again. Clamping around more than one wire in a single-phase or a 3-phase circuit rather than just one will most likely produce an incorrect reading.
Keep the wire in the right spot.
Many technicians are not aware of the two parallel lines found on the clamp of the DMM (Photo 3). In fact, many refer to this as a “negative sign.” The parallel lines indicate the “sensing zone” for the clamp. The conductors under test must be placed at or below these parallel lines for an accurate reading.
In addition to the true vs. average responding meter discussion previously, using an average-responding clamp-on meter can give erroneous readings as well. Know your DMM and what you are measuring.
Be safe — probing can be dangerous.
Probing around in a live panel with the DMM clamp to try and clamp around only one wire can result in unwanted contact with live parts. You might even knock a loose wire out of its terminal. As with all DMM usage, follow safety procedures, and never attempt to measure current with test leads inserted in the input jacks.
Tips for accurate resistance measurements
To measure resistance with the DMM, a small amount of current flow leaves a battery from within the meter, flows out the test lead, through the component under test, returns through the opposite test lead, through meter circuitry, and back to the battery. The amount of current flow is converted to ohms of resistance, and thus the reading on the meter face. Not paying attention to this simple circuit is where the problems arise with measuring resistance.
Do not touch the tips of both test leads while attempting a resistance reading.
Current will flow through any path possible to return to the source. Of course, the DMM does not know what path the current flow has taken — only that a certain amount flows back to the meter.
Photo 4 illustrates this error as the worker places fingertips on the test leads while testing a motor starter. Holding onto the tips of both leads will cause the DMM to attempt to measure resistance across the worker’s body, and the actual desired measurement will not be obtained. Always be sure at least one end (if not both ends) of the meter leads is making contact only with the circuit under test; otherwise, a parallel path for meter current flow can be created through the technician’s body.
Disconnect one portion of the circuit (if required).
Another example of parallel resistance is reading through multiple components when troubleshooting. Even the savviest troubleshooter can be caught off guard by this one. This especially applies when reading resistance in control circuits. There will be many parallel paths for current flow in the typical control circuit. Make sure the component under test is isolated from the remainder of the circuit.
Measure resistance only on de-energized circuits.
Do not rely on the DMM for protection. Understanding how the meter works to read resistance is also key to safety. Imagine placing a couple of AA batteries across an energized 120V, 240V, or even a 480V circuit. Not only would the meter most likely be destroyed, but the worker could also receive serious injury. Fortunately, most DMMs will have built-in protective circuitry to protect both the worker and the meter. If set to read resistance and placed on a live circuit, the DMM may emit an audible sound, a flashing LED, or simply fail to read a value depending upon the DMM. This is just another good reason to use quality test equipment and know that DMM before you use it.
Summary
Don’t be fooled by the user-friendliness of the modern DMM. A quality device used correctly can tell the electrical worker the specifics of a circuit that would be impossible to know otherwise. However, if certain key aspects of measurement techniques are not closely adhered to, inaccurate measurements can result — sometimes grossly inaccurate measurements. Be sure to know your meter and its nuances before you first apply it to a circuit. Understand how your DMM works and its limitations. Follow the manufacturer’s instructions for use, and apply the DMM tips provided to get the most out of your DMM.
Make Sure Your DMM Does What You Need It to Do
Here’s a handy checklist to follow when using a digital multimeter (DMM).
- Inspect the DMM, leads, and any accessories before each use.
- Replace DMM batteries before use if a low battery indication is obtained.
- Use a logging DMM to record data for later analysis and spot trends/sporadic problems.
- For safety and convenience, use a wireless DMM to obtain measurements remotely from the equipment.
- Consider a DMM with temperature, frequency, capacitance, milliamp, microamp, and other measurement capabilities if needed.
- Use the diode test function rather than the resistance function to test the operability of electronic components with P-N junctions such as diodes, transistors, and LEDs.
- Use the relative mode (REL) feature to indicate the difference between a stored value and the current value.
- Use the min/max setting to capture events that occur in microseconds and would otherwise be lost.
- Use intrinsically safe DMMs in hazardous locations.
About the Author
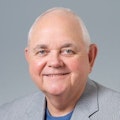
Randy Barnett
CESCP
Randy Barnett is an NFPA Certified Electrical Safety Professional, a long-time journeyman electrician, instructor and author with expertise in industrial electrical construction and maintenance. He is Electrical Codes & Safety Manager for NTT Training. Because of his ability to develop and deliver quality programs, Randy has trained more than 10,000 students in all 50 states, including Canada, Singapore, Afghanistan, Dubai, Trinidad, and Saudi Arabi. His articles appear in numerous trade publications and, his book on "Commercial and Industrial Wiring" is used as an entry-level text in many electrician training programs. Randy also appears at various corporate and trade association speaking engagements and consults on training program design and implementation. Randy is a graduate of the U.S. Navy Nuclear Power School, served as a nuclear electrician in submarines and holds a B.S. in business.