The Value of Independent Electrical Testing
Where were you in 1996? Were you at the start of your career in the electrical industry or a seasoned expert in your prime? Regardless of where that year found you in your professional life, one thing has remained constant — how valuable independent electrical testing (when performed prior to energization and servicing of loads) is to the safe operation of electrical systems.
Take a moment to think about this excerpt, shown in blue, which is taken from an EC&M “Thoughts from Our Shop” editorial written in June 1996 by Senior Editor Robert “Bob” Lawrie titled “Why Independent Electrical Testing is Best.”
Expert testing is your key to good design, safe construction, and reliable electrical system operation. In fact, when you think about the complex equipment and systems being specified and installed — and the maintenance know-how required to keep it running — it becomes obvious that skilled testing is vital to your welfare.
Revisiting some of Lawrie’s thoughts on the subject from 22 years ago, we will address how and why many of these concepts still hold true today.
If you think about it, electrical power systems have come a long way over the last couple of decades in the engineering, design, installation, reliability, and system validation of performance for these important assets. It should be noted that these field acceptance tests are different from the tests performed by independent testing laboratories such as UL for product conformance. They are also different from the manufacturer’s factory tests. It is assumed that the installing contractor utilized equipment manufactured and tested by the factory in compliance with standards from UL, NEMA, IEEE, etc. as applicable.
As noted in Lawrie’s editorial,
(1996) …the proliferation of fast-track projects, high-speed manufacture, expeditious design, and speedy installation can lead to mistakes and problems anywhere along the way.
The field tests performed by an independent third-party testing company verify that the equipment, after it has left the factory and after installation, has not been damaged, is correctly installed, and performs as the factory and design engineer intended that it should. This field test data assists electrical inspection authorities in determining that the equipment is suitable for service, and assures the owner that they received the goods and services as intended. Also, not to be overlooked is the fact that the electrical equipment is deemed safe for energization and continued use.
On the topic of initial testing and continued maintenance, what’s the secret to assuring the owner and user of electrical systems find value with independent testing? It’s a two-pronged approach: 1) consensus-based electrical standards and 2) personnel certification.
Let’s look at the two important aspects of independent electrical testing as they exist today (electrical standards and personnel certification), and compare some of the thoughts Lawrie had “from the shop” back in 1996.
Consensus-based electrical standards
Enough cannot be said about the significant contributions made by the men and women of the electrical industry who volunteer their time and efforts, whether on their own or through corporate sponsorship, toward the advancement of consensus-based electrical safety, installation, and performance standards. The standards available today and specified for use by independent electrical testing entities assure the owner of an unbiased assessment of their equipment, free from influence by the manufacturer or the installing contractor.
Once again, let’s hear from Lawrie.
(1996) Call in an expert tester to be sure your equipment and systems are safe, work properly, meet all applicable codes, and are legally certified as such. Electrical testing should be a required procedure for all new installations, modernizations, or electrical maintenance programs.
The process of developing consensus-based standards has shown to be an effective way to consolidate many aspects, facts, and points of expertise into a single document that allows interested parties from many factions of industry to contribute, comment, and ultimately agree upon.
Here are just a few examples of the relevant electrical standards that have had significant advancement over the last 22 years. These have not only advanced the electrical industry, but have also had a direct impact on the advancement of independent electrical testing entities:
National Fire Protection Association (NFPA) NFPA 70-2017
National Electrical Code (NEC)
A regionally adopted standard for the safe installation of wiring and equipment, the NEC is revised on a three-year cycle and is continuously improved and kept relevant to latest codes and standards. The NEC is an essential standard for all newly installed electrical systems.
NFPA 70B-2016
Recommended Practice for Electrical Equipment Maintenance
Though not a standard but a recommended practice, authorized by the NFPA in 1968 and first published in 1972, 70B provides guidance on the testing and maintenance of all types of electrical equipment. With the continued focus and understanding on how “condition of maintenance” affects the safe operation of equipment and protection of personnel, 70B is becoming more important with each passing day. The stated purpose of the recommended practice is “to reduce hazards to life and property that can result from failure or malfunction of industrial-type electrical systems and equipment.”
NFPA 70E-2018
Standard for Electrical Safety in the Workplace
First published in 1979 at the request of OSHA, the latest edition is from 2018. Arguably the world’s premier electrical safety standard, providing guidance and protection from electrical hazards, the stated purpose of the standard is “to provide a practical safe working area for employees relative to the hazards arising from the use of electricity.”
ANSI/NETA ATS-2017
Acceptance Testing Specifications for Electrical Power Equipment & Systems
First published in 1972, the latest edition is from 2017. NETA became an ANSI-accredited standards developer in 1996, and the acceptance testing specification was developed for use by those responsible for assessing the suitability for initial energization of electrical power equipment and systems and to specify field tests and inspections that ensure these systems and apparatus perform satisfactorily, minimizing downtime and maximizing life expectancy.
ANSI/NETA ETT-2018
Standard for Certification of Electrical Testing Technicians
First published in 2000, the latest edition of which is ANSI/NETA ETT-2018, the standard was created to codify the experience, education, and training requirements necessary for an individual to obtain a level of competency as an electrical test technician.
IEEE C2-2017
National Electrical Safety Code (NESC)
While most workers and workplaces are covered by the NEC and NFPA 70E, there are exemptions to the standards — most prominently in the utility sector. Where do they turn? Most use IEEE C2, the National Electrical Safety Code. The purpose of the NESC is “the practical safeguarding of persons during the installation, operation, or maintenance of electric supply and communication lines and associated equipment.”
Personnel certification
Certification of competency is particularly important in the electrical testing industry. Inherent in the determination of the equipment’s serviceability is the prerequisite that individuals performing the tests can conduct the tests in a safe manner and with complete knowledge of the hazards involved. They must also evaluate the test data and make an informed judgment on the continued serviceability, deterioration, or non-serviceability of the specific equipment. Here are several personnel certification resources that are available today:
InterNational Electrical Testing Association (NETA)
Certified Electrical Test Technician
Providing certification for the electrical testing technician (ETT), they perform tests and inspections and evaluate the suitability of electrical power equipment and systems for the intended use. As a requirement of certification, technicians performing these electrical tests and inspections shall be trained and experienced concerning the apparatus and systems being evaluated. These individuals shall conduct the tests in a safe manner and with complete knowledge of the hazards involved. They must evaluate the test data and make a judgment on the serviceability of the specific equipment.
NETA accredits the company and certifies the individual, thus assuring the end-user of the qualifications of the company as well as the overall competence of the individual technician. The association bylaws are designed to ensure that its members meet stringent criteria and provide a full range of testing services. NETA also requires continuing technical development for its certified technicians. The qualifications of each NETA-accredited company and its technicians are reviewed on a three-year cycle.
National Institute for Certification in Engineering Technologies (NICET)
Certification in Electrical Power Testing
Providing individual certification in electrical power testing that is portable throughout a technician or engineer’s career, NICET’s certification program is for technicians who test equipment used in the production, transmission, and distribution of electrical power. These technicians are engaged in inspection, testing, and periodic maintenance of electrical power equipment, and evaluation of such equipment for acceptance for service, continued serviceability, or required maintenance.
NFPA Certified Electrical Safety Compliance Professional (CESCP)
Certified Electrical Safety Professional
With a focus on NFPA 70E, the CESCP certification is designed to meet the needs of electrical and safety professionals who oversee electrical safety programs or who manage electricians and other personnel exposed to electrical hazards.
Professional Electrical Apparatus Reconditioning League (PEARL)
Electrical Equipment Reconditioning Technician
PEARL provides certification for electrical equipment reconditioning technicians, for individuals who inspect, test, evaluate, and recondition electrical equipment. Technicians must be knowledgeable about the electrical equipment they recondition and capable of performing reconditioning functions in a safe manner.
Final thoughts
Some manufacturers push back on the value and necessity for independent, third-party testing. We’ve heard statements such as “who better to service the equipment than the manufacturer of the equipment” or “we can assure the safety and reliability of the equipment and will provide an extended warranty if we do the commissioning.” However, long gone are the days when it’s any one manufacturer’s project.
Today, there are complex systems from different disciplines and vendors, all of which could be installed as an addition to an existing system that might include components from manufacturers that no longer exist or are part of a mergers and acquisitions scenario. All these variables affect the how electrical power systems are designed, built, and installed, and support the need for a well-rounded and vendor-neutral service provider: the independent electrical testing entity.
Turning back to Lawrie’s thoughts again:
(1996) Remember that on a new installation, asking a vendor to test his or her own equipment is like asking an author to review his or her own book. An independent, unbiased third party is bound to be more objective. Although a manufacturer may know its own equipment very well, it is unlikely that its experts will be asked to do any field testing. Also, vendor engineers are trained on details concerning only their own equipment and, as such, may overlook common problems in other brands of equipment. An independent test company has no vested interest in the equipment and is trained on a wide variety of brands. It approaches troubleshooting and maintenance in a thorough, step-by-step manner as prescribed in its manuals. It has no preconceived bias.
Advancements within the independent electrical testing industry over the last 22 years have been notable, and the advancements over the next 22 years should make for even safer and more reliable electrical systems.
One final point from Lawrie on this subject:
(1996) Without third-party acceptance testing performed by qualified test personnel immediately prior to energizing, potential problems could go undiscovered. Also, electrical testing is critical to effective maintenance of existing electrical equipment. Be sure to call for independent testing that will serve as your defense against a professional liability suit. Keep safety on your side--independent electrical testing is best.
Owners need to be assured their electrical assets are engineered correctly, are what they thought they were buying, have been installed in accordance with applicable codes and standards, are functioning reliably, and, most importantly, are safe for all those working on or near the equipment. This is the case both before initial energization as well as years after the equipment has been in service. So the bottom line is what was true in 1996 still holds true 22 years later.
Widup is the CEO and White is the vice president of training at Shermco Industries, Irving, Texas. They can be reached at [email protected] and [email protected].
About the Author
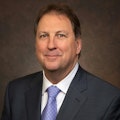
Ron Widup
Sr. Advisor, Technical Services
Ron Widup is the vice chairman, board of directors, and senior advisor of technical services for Shermco Industries and has been with Shermco since 1983. He is a member of the NETA Board of Directors and Standards Review Council; Principal member of the Technical Committee for NFPA Standard for Electrical Safety in the Workplace (NFPA 70E); Principal member of the National Electrical Code (NFPA 70) Code Panel 11; Principal member and Chairman of the Technical Committee for Standard for Competency of Third-Party Evaluation Bodies (NFPA 790); Principal member and Chairman of the Technical Committee on Recommended Practice and Procedures for Unlabeled Electrical Equipment Evaluation (NFPA 791); and Principal member of the Technical Committee Standard for Electrical Equipment Maintenance (NFPA 70B). He is a member of the Texas State Technical College System (TSTC) Board of Regents, a NETA Certified Level 4 Senior Test Technician, a State of Texas Journeyman Electrician, a member of the IEEE Standards Association, an Inspector Member of the International Association of Electrical Inspectors, and an NFPA Certified Electrical Safety Compliance Professional (CESCP).
James White
Director of Training
James R. (Jim) White is the VP of Training Services at Shermco Industries, Inc., in Irving, Texas. He is a certified electrical safety compliance professional (CESCP) through the NFPA and one of approximately 130 Level IV senior certified technicians through NETA. A principal member for Shermco Industries on the NFPA Technical Committee “Recommended Practice for Electrical Equipment Maintenance” (NFPA 70B), he represents the interNational Electrical Testing Association (NETA) and is also an alternate member of NFPA Technical Committee “Standard for Electrical Safety in the Workplace” (NFPA 70E), a principal representative of NEC Code Making Panel CMP-13, and principal representative of ASTM F18 Committee “Electrical Protective Equipment For Workers.” White is a senior member of IEEE and past chairman (2008) of the IEEE Electrical Safety Workshop. In 2011, he received the IEEE/PCIC “Electrical Safety Excellence” award, and in 2013 he was honored with NETA’s “Outstanding Achievement Award.”