Tip of the Week: Missing from Maintenance Procedures
Well-written maintenance procedures don’t cover every contingency. Instead, they are designed to ensure the same maintenance steps are performed each time. One goal of training should be to ensure those steps are performed the same way every time.
Because those procedures are lean, they occasionally leave holes. An electrician performing preventive maintenance (PM) may notice something not covered by the PM. If the electrician simply fixes it, then there’s no history and the problems just continue.
So these “outside the PM” issues must be reported. They include such things as poor lighting, poor workmanship, housekeeping issues, National Electrical Code (NEC) violations, visible damage to conductors, and even squeaky hinges on cabinet doors.
What should management do about the reported problems? In one plant, every time an issue arose in the course of a PM, another item was added to the PM procedure. This eventually made each PM procedure so cumbersome nobody would use it.
Management finally came to terms with this issue. They stripped out all of the “we found this problem once” steps that were added. Then they considered what from this list could be mentioned in related training. They also created a list of items to mention in the daily safety talk (only one item per safety talk).
A suggestion here is to add one line to each PM: “Other issues not covered by the PM.” Next to this have a checkbox for “Repaired” and another for “Reported only.”
Something like an oil spill would be addressed immediately. Something like a missing knockout in a box or a messy wire loom in a control cabinet would be considered repair ticket material.
Anything that is an NEC violation (such as that missing knockout) should be treated like the proverbial canary in the mine. Have the repair ticket mention the specific problem to be fixed. But also have instructions to look for (and repair) similar NEC violations in the immediate area.
About the Author
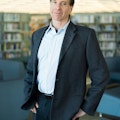
Mark Lamendola
Mark is an expert in maintenance management, having racked up an impressive track record during his time working in the field. He also has extensive knowledge of, and practical expertise with, the National Electrical Code (NEC). Through his consulting business, he provides articles and training materials on electrical topics, specializing in making difficult subjects easy to understand and focusing on the practical aspects of electrical work.
Prior to starting his own business, Mark served as the Technical Editor on EC&M for six years, worked three years in nuclear maintenance, six years as a contract project engineer/project manager, three years as a systems engineer, and three years in plant maintenance management.
Mark earned an AAS degree from Rock Valley College, a BSEET from Columbia Pacific University, and an MBA from Lake Erie College. He’s also completed several related certifications over the years and even was formerly licensed as a Master Electrician. He is a Senior Member of the IEEE and past Chairman of the Kansas City Chapters of both the IEEE and the IEEE Computer Society. Mark also served as the program director for, a board member of, and webmaster of, the Midwest Chapter of the 7x24 Exchange. He has also held memberships with the following organizations: NETA, NFPA, International Association of Webmasters, and Institute of Certified Professional Managers.