Energy-Saving Tips Associated with Motor Installations
Industrial motor installations often provide great opportunities for energy savings. The typical industrial motor lasts a long time — often several decades — so an investment in energy reduction can add up to serious money during the lifetime of the installation.
Where can you find this gold mine of savings? Here are some areas to look:
• Motor selection. An energy-efficient motor costs more than its counterpart, but over the life of the motor the difference can pay for itself many times over. Thus, replacing a perfectly good standard motor with an energy-efficient one may make financial sense. Make sure you also choose the correct motor for the application (e.g., Design B if that’s appropriate, correct insulation rating for the temperature, etc.).
• Circuit conductors. It’s hard to find something that makes less sense than “saving money” by sizing motor circuit conductors to the minimum size required by code and paying for the resulting voltage drop every day for the next 40 years. Minimize voltage drop to the degree that is practical. It’s not ethical to save $50 in construction costs knowing the owner is going to lose that much money every month in wasted energy costs; at least give the owner a chance to decide whether to waste the money or not.
• Voltage imbalance. You may “save money” by using the motor supply circuits to supply lighting loads instead of putting those loads on their own transformer/panel. In addition to wasting energy, the voltage imbalance (which you almost certainly will have) greatly reduces the life of the motor. Maybe this makes even less sense than undersizing the conductors. What do you think? Keep three-phase and single-phase loads on separate branch circuit transformer/panel systems.
• Power factor. Motors are inductive loads, so they will cause power factor to drop unless there is power factor (PF) correction at the motor. If the PF correction is in the variable frequency drive (VFD), it will not affect the power supply unless the motor is running. If the VFD is not PF-corrected, adding PF correction capacitors solves this problem, but only when the motor is running. When the motor is not running, those capacitors need to be out of the circuit; so think through your motor controls and where you place these capacitors.
• Power quality. PF isn’t the only power quality issue. We already mentioned voltage imbalance. Use a power analyzer to find other power quality issues that need solving.
• Lubrication. It’s not true that “grease is grease.” Many greases are not compatible with one another, and mixing some greases can have about the same effect as pouring sand into the bearings. That does waste energy, and it can easily waste the motor too. Beyond this simple mistake, don’t try to “save money” by using cheap greases. Use a modern synthetic lubricant, and make sure whoever is greasing the motors has completed formal training in how to do the job correctly. Lubrication errors are a significant source of downtime in factories, mostly because those doing the lubrication are usually not qualified for that purpose.
• Alignment/vibration minimization. When a motor shakes, what’s really happening is some of the energy that should go toward turning the motor (and thus the load) is being wasted to move the motor back and forth. The time taken to do an extremely precise alignment is a wise investment, especially if you use good tools to ensure the alignment actually is precise.
• Motor controls. In the motor system, use a VFD to reduce motor speed rather than using a gearbox to reduce speed (unless the gearbox is needed to increase torque). In many systems, a motor drives a pump, and there’s a pressure bypass or flow control that wastes the output; instead, reduce the output at the source using a VFD.
• Gearboxes. Where you do use a gearbox, ensure it’s precisely aligned to the motor at one end and to its load at the other. Ensure its mounting is secure and minimizes vibration. Set it up on a temperature monitoring program (infrared thermography and/or temperature switch) to alert maintenance when efficiency drops. Efficiency may drop because of gear wear or lubrication problems; using synthetic lubricant minimizes both of these causes.
About the Author
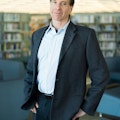
Mark Lamendola
Mark is an expert in maintenance management, having racked up an impressive track record during his time working in the field. He also has extensive knowledge of, and practical expertise with, the National Electrical Code (NEC). Through his consulting business, he provides articles and training materials on electrical topics, specializing in making difficult subjects easy to understand and focusing on the practical aspects of electrical work.
Prior to starting his own business, Mark served as the Technical Editor on EC&M for six years, worked three years in nuclear maintenance, six years as a contract project engineer/project manager, three years as a systems engineer, and three years in plant maintenance management.
Mark earned an AAS degree from Rock Valley College, a BSEET from Columbia Pacific University, and an MBA from Lake Erie College. He’s also completed several related certifications over the years and even was formerly licensed as a Master Electrician. He is a Senior Member of the IEEE and past Chairman of the Kansas City Chapters of both the IEEE and the IEEE Computer Society. Mark also served as the program director for, a board member of, and webmaster of, the Midwest Chapter of the 7x24 Exchange. He has also held memberships with the following organizations: NETA, NFPA, International Association of Webmasters, and Institute of Certified Professional Managers.