Sometimes when Preventive Maintenance (PM) or Predictive Maintenance (PdM) must be done on a motor, it’s not running. So the maintenance tech must start the motor and run it to complete the maintenance task (or come back later, which often isn’t a good option).
PM work is intended to extend the life of the motor, but the choices made when starting the motor can put it under life-shortening stress. PdM work allows you to predict failure and schedule repairs or replacement, but the choices made when starting the motor could put a “failing” motor firmly into the “failed” category.
One of the most important things to do is avoid starting the motor under maximum load. If you can avoid any load at all, even better. For example, don’t start:
• An air compressor motor in its high-demand loading phase.
• A pump motor if the pump it drives is dead-headed.
• A mixer if the tank is full of slurry, unless that just can’t be avoided.
• A grinder if the feeder chute has material in it.
About the Author
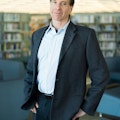
Mark Lamendola
Mark is an expert in maintenance management, having racked up an impressive track record during his time working in the field. He also has extensive knowledge of, and practical expertise with, the National Electrical Code (NEC). Through his consulting business, he provides articles and training materials on electrical topics, specializing in making difficult subjects easy to understand and focusing on the practical aspects of electrical work.
Prior to starting his own business, Mark served as the Technical Editor on EC&M for six years, worked three years in nuclear maintenance, six years as a contract project engineer/project manager, three years as a systems engineer, and three years in plant maintenance management.
Mark earned an AAS degree from Rock Valley College, a BSEET from Columbia Pacific University, and an MBA from Lake Erie College. He’s also completed several related certifications over the years and even was formerly licensed as a Master Electrician. He is a Senior Member of the IEEE and past Chairman of the Kansas City Chapters of both the IEEE and the IEEE Computer Society. Mark also served as the program director for, a board member of, and webmaster of, the Midwest Chapter of the 7x24 Exchange. He has also held memberships with the following organizations: NETA, NFPA, International Association of Webmasters, and Institute of Certified Professional Managers.