Electricians often are tasked with motor maintenance, but are not trained in the mechanical end of things. For example, how do you pack grease in a bearing? There is a prescribed method for doing this, and it’s not at all similar to how untrained people do it.
Generally, sending motors to a motor shop for mechanical work internal to the motor is more cost-effective than having electricians do it (if the downtime window permits). Partly, this is because of the training deficiencies (which invariably result in early failures).
And partly it’s because electricians are a limited resource best tasked to electrical work. This dynamic also typically applies to plant mechanics, though presumably they have had instruction on the correct way to pack and install a bearing.
Among the electrical work electricians can do to reduce bearing failure, the following items are particularly important:
- Eliminate motor grounding. This sounds counterintuitive, unless you understand the NEC definitions of grounding and bonding [Art. 100]. Grounding is a connection to the dirt. It’s crucial for lightning protection, but does nothing to eliminate the differences of potential that can cause current to flow through bearings.
- Establish a robust bonding system for each motor system. This is what you do instead of driving a ground rod next to the motor. Remember, current does not follow the path of least resistance. We know, from Kirchoff’s Law, that current takes every path before it in inverse relationship to the impedances. Draw a circuit with two resistors, 100 ohms and 10 ohms, in parallel to refresh your memory on this one.
- Conduct power quality analysis. Good bonding will reduce current through bearings to nearly zero, but you still want to reduce or eliminate that current at its source. Undesired high frequencies from power quality anomalies are especially problematic.
- Routinely conduct thermographic scans to identify high-impedance connections, as these contribute to a slew of problems (including voltage imbalance if especially bad in one phase). Also use those scans to identify environmental temperature problems and bearings that already are running hot.
About the Author
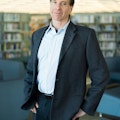
Mark Lamendola
Mark is an expert in maintenance management, having racked up an impressive track record during his time working in the field. He also has extensive knowledge of, and practical expertise with, the National Electrical Code (NEC). Through his consulting business, he provides articles and training materials on electrical topics, specializing in making difficult subjects easy to understand and focusing on the practical aspects of electrical work.
Prior to starting his own business, Mark served as the Technical Editor on EC&M for six years, worked three years in nuclear maintenance, six years as a contract project engineer/project manager, three years as a systems engineer, and three years in plant maintenance management.
Mark earned an AAS degree from Rock Valley College, a BSEET from Columbia Pacific University, and an MBA from Lake Erie College. He’s also completed several related certifications over the years and even was formerly licensed as a Master Electrician. He is a Senior Member of the IEEE and past Chairman of the Kansas City Chapters of both the IEEE and the IEEE Computer Society. Mark also served as the program director for, a board member of, and webmaster of, the Midwest Chapter of the 7x24 Exchange. He has also held memberships with the following organizations: NETA, NFPA, International Association of Webmasters, and Institute of Certified Professional Managers.