OSHA began as a system for regulating employers and mandating a top-down system for improving workplace safety. OSHA regulators realized this approach alone wasn’t enough, and they requested private industry to develop a standard that mainly comes from the other direction. That standard is NFPA 70E. It provides a framework that employees can use to ensure electrical safety in the workplace.
You could approach this standard with the mindset it’s a collection of rules and procedures that you need to game to get your work done efficiently. Or you could approach this standard with the mindset that it’s a guide to what you can (and should) do to ensure an electrically safe workplace.
If you choose the latter, you’ll find implementation actually improves your overall efficiency. And not just because giving an honest effort to NFPA 70E greatly reduces the likelihood of productivity-draining injuries and fatalities.
One reason for unsafe acts in the performance of work is the work is not being performed methodically and with sufficient information to adequately understand the job before starting to do it. NFPA 70E organizes the approach to work. You could almost view the improved safety as a side benefit.
Consider, for example, the Job Briefing and Planning Checklist provided in Informative Annex I. Read through that, and you can readily see that the job walk-through needed to complete this will also solve other problems.
Consider for example, why rework is typically done (answer: poor prejob planning) and how this eliminates that cause. Or think about how many wasted trips get made mid-job for tools, PPE, equipment (e.g., a taller ladder), portable lighting, test equipment, and drawings that “nobody thought of” prior to starting the work. How many times have you had to put covers back on, go get these items, then remove the covers again?
About the Author
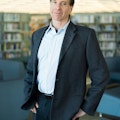
Mark Lamendola
Mark is an expert in maintenance management, having racked up an impressive track record during his time working in the field. He also has extensive knowledge of, and practical expertise with, the National Electrical Code (NEC). Through his consulting business, he provides articles and training materials on electrical topics, specializing in making difficult subjects easy to understand and focusing on the practical aspects of electrical work.
Prior to starting his own business, Mark served as the Technical Editor on EC&M for six years, worked three years in nuclear maintenance, six years as a contract project engineer/project manager, three years as a systems engineer, and three years in plant maintenance management.
Mark earned an AAS degree from Rock Valley College, a BSEET from Columbia Pacific University, and an MBA from Lake Erie College. He’s also completed several related certifications over the years and even was formerly licensed as a Master Electrician. He is a Senior Member of the IEEE and past Chairman of the Kansas City Chapters of both the IEEE and the IEEE Computer Society. Mark also served as the program director for, a board member of, and webmaster of, the Midwest Chapter of the 7x24 Exchange. He has also held memberships with the following organizations: NETA, NFPA, International Association of Webmasters, and Institute of Certified Professional Managers.