A safety incident report usually identifies the precipitating event. It doesn’t identify the small failures that led to it. In many cases, those failures aren’t just three deep but far deeper.
One way to determine the root cause is to start with the precipitating event and use the Five Questions Method. But it may need to branch off, due to the multiple causes effect (typically, multiple errors precede a safety incident). Here’s an example:
Jerrod sustained a serious eye injury.
Q1: Why did Jerrod sustain a serious eye injury?
A: He was standing next to a grinder when he had no reason to be there, and his safety glasses didn’t have side shields.
Q2: Why was Jerrod standing there?
A: He was waiting for Brad, the machinist, to put the finishing touches on a part.
Q3: Why did Brad permit an unnecessary third party to stand so close to the grinder?
A: Brad had not been trained in this safety issue.
Q4: Why didn’t Jerrod’s safety glasses have those side shields?
A: Jerrod had been instructed per the company’s safety policy to have those side shields but ignored the instructions.
Q5: Why didn’t Jerrod’s coworkers, Jerrod’s supervisor, or any other supervisor call him out on this?
A: That’s a very good question.
This method is helpful, but using it is tricky. It’s easy to get the wrong answer and then follow the wrong path. For example, the answer to Q2 could have been there was no waiting area for Jerrod — and that could have led to asking why we don’t have a waiting area. But a waiting area for “customers” of the machinists is a luxury.
And how would going down that path prevent a similar outcome if Jerrod’s coworker Dave is unnecessarily in the wrong place in some other circumstance? For example, he’s escorting a contractor who is a thermographer. The thermographer must stand in front of equipment that has covers removed. But whether Dave does the same does not affect the outcome of the thermography, so he has no reason to also stand in front of the equipment. He is safer to stand off to one side. A similar logic extends to many other circumstances, such as when Bill stands under a crane load.
Because it’s a rearview mirror approach and because of seemingly infinite permutations of safety mistakes, this approach is of limited value. You may determine what exact error started the whole chain of events, but correcting for it won’t prevent a similar error from being made due to the same underlying cause.
How do you get at the underlying cause?
Ask the right question
Though it may take a slight cognitive leap, you get better results faster by asking, “Which fundamental safety principles, controls, and/or procedures may have been violated here?” Answer that, and you pull up a weed by its roots instead of plucking off a leaf.
You’ll find a list of 10 principles in NFPA 70E, Informative Annex E, E.1. This Annex also lists eight safety program controls [E.2] and 12 procedures [E.3]. These are typical — exactly what’s in your facility’s electrical safety program may differ.
Going back to Q5 in the example of Jerrod, the answer that will help us the most is that there was a failure to fully implement the safety program principle of “Protecting employees from shock, burn, blast, and other hazards due to the working environment.”
This still leaves us with a rearview mirror approach, however. Waiting for the wake-up call of a safety incident to tell you to address safety program defects is not the best way.
Getting in front of it
We can draw lessons from how maintenance has evolved over the past few decades. At one time, maintenance was reactive. The main job of the maintenance department was to follow failures around and fix them. This was often referred to as “putting out fires.” This is the equivalent of fixing a safety failure after someone is injured.
Then someone got the idea of doing the equivalent of basic fire prevention. This was called... wait for it... preventive maintenance. For electricians, this meant performing specific steps like cleaning breaker contacts and lubricating motors — and usually on a calendar basis, whether a need was indicated or not. It did, however, significantly reduce downtime. Applying this concept to reducing safety incidents means things like regularly scheduled safety training, inspections of tool guards, and inspections of PPE.
Modern maintenance is condition-based and predictive. One benefit of this approach is it eliminates unnecessary maintenance, which is wasteful and needlessly introduces human error. The biggest advantage is it provides a fact-based means of intervening before a failure occurs. This is where you need to be with your safety program.
Safety training doesn’t automatically make people safe. Maybe they don’t understand the training, don’t retain it, or don’t comply with it. Condition-based and predictive maintenance both require the use of test equipment to measure what’s going on and a system to compare the measurement to expected values. Those values may be absolute (e.g., motor vibration not to exceed 0.16 in. per second). Or they may be relative (e..g., the latest reading of insulation resistance shows a sharp rise in the curve relative to the historic measurements).
Thus, to “get in front of it,” you must have a means of measuring how well safety training is understood, retained, and implemented.
Understanding
NFPA 70E provides general retraining requirements in Sec. 110.6. This text uses terms such as “knowledgeable,” “understand,” and “familiar.” Your “test equipment” to employ the equivalent of condition-based and predicative maintenance on training efficacy consists of things like:
- Asking probing questions during training.
- Asking those same questions of those who have completed the training (“qualified persons”).
- Witnessing and critiquing practical demonstrations during training.
- Witnessing and critiquing actual performance by qualified persons.
These functions need not — and should not — fall entirely on management. Workers should check each other, providing a cycle of regular observation and feedback.
Retention
The NFPA 70E Technical Committee members understand that people forget things over time, thus NFPA 70E has retraining requirements built in. For example, lockout/tagout retraining must take place at intervals not exceeding three years [Sec. 110.6(B)(2)(2)].
Practice does not make perfect, practice makes permanent. Over time, people will introduce small mistakes in how they do things. If not spotted, identified, and corrected, those become ingrained. To extend retention, you must nip error creep in the bud.
One way to do that is to pick some error discovered in the “Understanding” phase we just discussed and then address it to the team. For example, Larry didn’t use the correct voltage verification method during lockout/tagout. So at the next safety meeting, the electrical supervisor might conclude by saying, “I don’t want any of you taking shortcuts with voltage verification while doing lockout/tagout. It can become a fatal habit.” There’s no need to detail what that method is; these qualified people have already been trained on it. The mention will trigger what needs to be triggered.
Compliance
Failure to comply with the safety program requirements can be due to problems with understanding and/or retention. But if you have addressed those, then you must look for other factors. It may be the company’s fault. For example, Erin wasn’t wearing the proper gloves. You ask why, and she says the tool crib did not have any her size. Simply going without is not a correct solution, Erin should have gone to her supervisor about the problem. But maybe she did, and it’s the supervisor who isn’t complying because he told her to just use other gloves that fit even though they aren’t correct for the task.
If the employee is violating the safety program requirements and the company is at least partly to blame (as in the gloves example), you have a training problem. The employee needs to be made aware that where some issue prevents compliance, the work must stop until the issue is resolved.
In cases where the employee is willfully violating those requirements, you have a discipline problem.
Don’t extend a “favor” by giving the offending employee an unofficial verbal warning. Follow the company’s procedure for progressive discipline. The reasons go beyond legal protection for the company and include the protection of other employees.
Real causes
While it may suffice for insurance and legal reasons to file a safety incident report that identifies only the precipitating event, it doesn’t suffice for getting at the real root causes of safety failures. Nor is it good to wait for an incident before addressing those root causes.
You need to be proactive, predictive, and constantly on the lookout for small erosions in safety training and safety practices. This is ultimately much better than chasing your tail after someone is injured.
About the Author
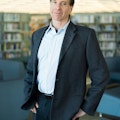
Mark Lamendola
Mark is an expert in maintenance management, having racked up an impressive track record during his time working in the field. He also has extensive knowledge of, and practical expertise with, the National Electrical Code (NEC). Through his consulting business, he provides articles and training materials on electrical topics, specializing in making difficult subjects easy to understand and focusing on the practical aspects of electrical work.
Prior to starting his own business, Mark served as the Technical Editor on EC&M for six years, worked three years in nuclear maintenance, six years as a contract project engineer/project manager, three years as a systems engineer, and three years in plant maintenance management.
Mark earned an AAS degree from Rock Valley College, a BSEET from Columbia Pacific University, and an MBA from Lake Erie College. He’s also completed several related certifications over the years and even was formerly licensed as a Master Electrician. He is a Senior Member of the IEEE and past Chairman of the Kansas City Chapters of both the IEEE and the IEEE Computer Society. Mark also served as the program director for, a board member of, and webmaster of, the Midwest Chapter of the 7x24 Exchange. He has also held memberships with the following organizations: NETA, NFPA, International Association of Webmasters, and Institute of Certified Professional Managers.