Whether you’re developing an electrical safety program from scratch or reviewing an existing one, Informative Annex E is a valuable resource. It’s divided into three sections:
E.1 Typical Electrical Safety Program Principles. A principle is a theme or concept that underlies the requirements stated in the program. To ensure your program is effective, develop a list of principles. What do we want our electrical safety program to accomplish? Annex E enumerates ten principles that you’d typically find in a well-thought out program. These include inspecting and evaluating the electrical equipment, using the right tool for the job, and assessing people’s abilities.
E.2 Typical Electrical Safety Program Controls. A control is a method for reducing or eliminating the hazards encountered. Annex E enumerates eight such controls. One example is “Procedures are to be used to identify the electrical hazards and to develop job safety plans to eliminate those hazards or to control the associated risk for those hazards that cannot be eliminated.” Another example is “Precautions appropriate to the working environment are to be determined and taken.”
E.3 Typical Electrical Safety Program Procedures. Annex E enumerates twelve things you’d typically find in a procedure. These include purpose of task, limits of approach, and reference data. What Annex E doesn’t tell you is what to exclude from your procedures. That is also an important aspect of writing a usable procedure. Always keep in mind that the only people performing the work are those who are “qualified” in the OSHA sense of the word. They already know how to do the work, so do not include tutorial information or lengthy explanations (if you look at the list of twelve, you’ll see those are not on the list).
About the Author
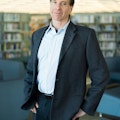
Mark Lamendola
Mark is an expert in maintenance management, having racked up an impressive track record during his time working in the field. He also has extensive knowledge of, and practical expertise with, the National Electrical Code (NEC). Through his consulting business, he provides articles and training materials on electrical topics, specializing in making difficult subjects easy to understand and focusing on the practical aspects of electrical work.
Prior to starting his own business, Mark served as the Technical Editor on EC&M for six years, worked three years in nuclear maintenance, six years as a contract project engineer/project manager, three years as a systems engineer, and three years in plant maintenance management.
Mark earned an AAS degree from Rock Valley College, a BSEET from Columbia Pacific University, and an MBA from Lake Erie College. He’s also completed several related certifications over the years and even was formerly licensed as a Master Electrician. He is a Senior Member of the IEEE and past Chairman of the Kansas City Chapters of both the IEEE and the IEEE Computer Society. Mark also served as the program director for, a board member of, and webmaster of, the Midwest Chapter of the 7x24 Exchange. He has also held memberships with the following organizations: NETA, NFPA, International Association of Webmasters, and Institute of Certified Professional Managers.