NFPA 70E: Electrical Safety — Lockout/Tagout Principles and Employee Involvement
NFPA 70E provides a terse directive on employee involvement. It says, “Each person who could be exposed directly or indirectly to a source of electrical energy shall be involved in the lockout/tagout procedures” [120.2(A)].
It then provides an example of direct exposure and another of indirect exposure [Informational Note]. The first example is an electrician who is working on the motor starter control. It’s a direct exposure situation because the electrician could come into direct contact with the electricity present on the motor starter control terminals.
The second example is who is working on the coupling between the motor and the compressor. This person isn’t exposed to the electrical energy, but they are exposed to the mechanical energy produced by the motor due to the presence of the electrical energy. The way you protect this person in the second example is by de-energizing the circuit supplying the motor and motor starter.
This principle of protecting not only against shock from direct contact with electricity but also against injury from electrically driven equipment is a core principle in lockout/tagout. To fulfill this principle, you must start lockout/tagout with an assessment of the entire system you’re working on. In so doing, you should also look for where you may be the direct or indirect recipient of non-electrical energy sources.
Some questions to answer:
- Who else will also need their lock and tag on specific equipment? That is, who else may be directly or indirectly exposed?
- Who else (including operators) may be affected by de-energization or operation of this circuit/panel/machine even if not directly or indirectly exposed?
- What are the operational implications, as deduced from the drawings? What are the operational implications, according to the operators? Resolve any discrepancies.
- Are there any emergency devices (e.g., pressure valves, annunciators, fire protection) that are presumably operational? What happens if one operates while the area is occupied? Do any of these need to be rendered temporarily inoperable, and, if so, what is the exact procedure for that?
- Which equipment must be prepared in advance for shutdown (e.g., by removing work in process)?
- Are there any time limits or other restrictions or conditions of lockout to consider?
- What other energy sources must be addressed? Consider kinetic (e.g., punch press ram position), pneumatic, hydraulic, process pressure, etc.
- What non-electrical means should or must be used in addition to electrical lockout?
Not everyone who is “involved” will necessarily be aware of being involved. If you are performing the lockout/tagout, part of your job is to determine who may be directly or indirectly affected by your work on the equipment and then involve them in the lockout/tagout process. In many plants, discussing the project with the production superintendent or designated supervisor is part of the process, and it will give you answers to those questions posed above.
About the Author
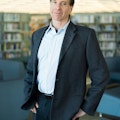
Mark Lamendola
Mark is an expert in maintenance management, having racked up an impressive track record during his time working in the field. He also has extensive knowledge of, and practical expertise with, the National Electrical Code (NEC). Through his consulting business, he provides articles and training materials on electrical topics, specializing in making difficult subjects easy to understand and focusing on the practical aspects of electrical work.
Prior to starting his own business, Mark served as the Technical Editor on EC&M for six years, worked three years in nuclear maintenance, six years as a contract project engineer/project manager, three years as a systems engineer, and three years in plant maintenance management.
Mark earned an AAS degree from Rock Valley College, a BSEET from Columbia Pacific University, and an MBA from Lake Erie College. He’s also completed several related certifications over the years and even was formerly licensed as a Master Electrician. He is a Senior Member of the IEEE and past Chairman of the Kansas City Chapters of both the IEEE and the IEEE Computer Society. Mark also served as the program director for, a board member of, and webmaster of, the Midwest Chapter of the 7x24 Exchange. He has also held memberships with the following organizations: NETA, NFPA, International Association of Webmasters, and Institute of Certified Professional Managers.