Since its creation in 1971, OSHA has made a huge difference in worker safety but not directly. OSHA doesn’t come on site and show people how to work safely. So, what does OSHA do?
Among other things, OSHA publishes safety regulations for employers to follow. The regulations are part of the Code of Federal Regulations (CFR), specifically 29 CFR. OSHA then cites employers for violations of these regulations when the thinly spread OSHA inspectors catch them violating. A citation may or may not carry a fine or other sanction.
An individual is not legally capable of violating an OSHA regulation, since the regulations are for companies to follow. But companies are made of individuals, and that has implications for OSHA compliance:
- If individual executives don’t properly fund and oversee the creation/execution of the company’s safety program, OSHA violations are guaranteed to occur. Whether OSHA will see those is another matter but not one that should matter. The existence of violations means employees are under threat of physical harm, and that’s what should matter to the executives.
- If individual managers don’t properly execute their responsibilities in the training and performance of employees relative to the company’s safety program — and fulfill their responsibilities in auditing the program and correcting program deficiencies — OSHA violations are guaranteed to occur.
- If individual employees don’t do their best to learn from the safety training, perform their work within the framework of the safety program, and work in state of safety awareness, the effect on the number of OSHA violations may be negligible, but the effect on employee safety will be significant.
Those OSHA regulations weren’t just dreamed up by someone sitting behind a desk. They have had heavy input from industry. The regulations related to electrical work are particularly noted for that, which is why you see verbatim wording in industry standards, such as the working space requirements stated in NFPA 70. NFPA 70 did not adopt those from OSHA. It wasn’t quite the other way around, either. The head of OSHA’s electrical section collaborated with industry standards makers (such as National Electrical Code Panel members) to develop a set of rules that were practical, sensible, and effective.
The “in what ways would you be able or unable to comply” question would come up. If compliance meant some impractical burden, then something would change. The result is that OSHA regulations (for the most part) are not necessarily difficult to comply with. But just as the NEC is not a design manual for electrical installations and doesn’t advise you on how to optimize an installation for efficiency [Art. 90], so the OSHA regulations do not constitute a safety manual for companies to use or workers to follow. A major concept underlying the OSHA regulations is they provide a basis for a company to create its safety program, which employees then follow.
All this being said, consider that some OSHA violations just don’t seem to go away. Last year, fall protection held the No. 1 slot for the twelfth year in a row. There were over 5,250 citations, about the same as the previous year. That doesn’t mean there were “only” 5,250 + violations. Remember, the thinly spread OSHA inspectors don’t cite what they don’t catch.
OSHA’s fall protection requirements are in Subpart M. This runs a little less than seven pages and is followed by Appendix A, B, C, D, and E. The appendices provide helpful supplemental information, including a simple fall protection plan. Subpart M itself covers:
- Duty to have fall protection
- Fall protection systems criteria and practices
- Training requirements
Nothing in here is intellectually challenging, and fall protection systems are not unduly expensive or hard to obtain. For individual executives and individual managers to fail to live up to their responsibilities as laid out in Subpart M is, therefore, a failing of character — not of ability or resources.
To underscore this character problem even further, the manufacturers of fall protection equipment provide many free resources. Depending on the product and the manufacturer, these include instructional videos plus manuals with good graphics and clear text. Safety-oriented executives and managers don’t consider these resources optional; they drink them in.
Individuals, of course, may fail to use their fall protection training while on the job, but most individuals don’t. The problem is (and we know this from the sheer number of violations and that number one spot) with the executives and managers. This leaves a void that the employees themselves can fill.
If your company doesn’t have a solid fall protection program, then ask your manager why not and when this will be fixed. If you get a wishy washy answer, go to the next level of management or personally contact the CEO or (if small shop) owners about this issue. Don’t make threats (such as you will quit or you will call OSHA). Just explain that the company has a serious problem and is at risk for major liability, plus your personal safety is at risk.
Make it clear you are there to seek and offer help, not to cause trouble. The trouble will cause itself if the issue isn’t given its proper due by management. Ask what you might do to help. Do they need a copy of the OSHA regulations? Offer to get them one. Do they lack a trainer? Offer to study the OSHA regulations and the company safety program and be at least a fill-in fall protection safety trainer.
If you simply wait for company leaders who have not shown leadership to suddenly do so, you will wait a long time. By taking the lead on this (or any other) safety issue, you show your own leadership potential and help make your company a safer one to work for.
What if your company has a solid fall protection program? Personally thank at least one executive and at least one manager for making this happen. Show leadership by doing your best to understand and execute the company’s fall protection program. It also would not hurt to tell a coworker or two that your company isn’t one of those racking up OSHA violations (whether cited or not) and that says something about your management.
About the Author
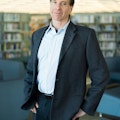
Mark Lamendola
Mark is an expert in maintenance management, having racked up an impressive track record during his time working in the field. He also has extensive knowledge of, and practical expertise with, the National Electrical Code (NEC). Through his consulting business, he provides articles and training materials on electrical topics, specializing in making difficult subjects easy to understand and focusing on the practical aspects of electrical work.
Prior to starting his own business, Mark served as the Technical Editor on EC&M for six years, worked three years in nuclear maintenance, six years as a contract project engineer/project manager, three years as a systems engineer, and three years in plant maintenance management.
Mark earned an AAS degree from Rock Valley College, a BSEET from Columbia Pacific University, and an MBA from Lake Erie College. He’s also completed several related certifications over the years and even was formerly licensed as a Master Electrician. He is a Senior Member of the IEEE and past Chairman of the Kansas City Chapters of both the IEEE and the IEEE Computer Society. Mark also served as the program director for, a board member of, and webmaster of, the Midwest Chapter of the 7x24 Exchange. He has also held memberships with the following organizations: NETA, NFPA, International Association of Webmasters, and Institute of Certified Professional Managers.