A large manufacturing plant in central Tennessee had a robust safety program. The safety director physically toured the plant twice a week, always taking with him a department head or supervisor to make it a training exercise, not just an inspection. Consequently, safety problems tended to be spotted and resolved early on.
Imagine the safety director’s surprise when, one day, he received a phone call from OSHA; the caller wanted to discuss frequent reports of OSHA violations. The OSHA rep said it was the same individual calling and one would be hard-pressed to call any of the complaints actual violations. OSHA did not want to discourage employees from reporting their concerns, but this individual was abusing the privilege.
OSHA was not at liberty to share the individual’s name. However, it could share that the nature of the complaints indicated this person worked in maintenance on the second shift. After reviewing the complaint list, the safety director agreed. There was enough vagueness to avoid any kind of reporting retribution, but enough clues left by the employee that the company could do something to stop what amounted to the harassment of a federal agency.
The plant engineer was tasked with meeting individually with each second-shift maintenance employee to discuss the reporting. The gist of what the plant engineer was instructed to say is, “Please tell us first and give us a chance to address the problem. You should contact OSHA only if we are unreasonably unresponsive to your concern.”
That is the first filter in deciding whether to report your employer to OSHA. Did you give your employer a chance to fix the problem? Did you clearly articulate what the problem is, so they don’t have to play guessing games? Did you ask for an estimated time before resolution and then follow up with them if the problem isn’t resolved by then?
Safety violations happen. Generally, they exist due to a combination of circumstances that may include an individual’s failure to comply with existing policy. They may or may not be the fault of company management.
Generally, OSHA violations exist due to a weakness in the company’s safety policies. That can include holes in the policies themselves, inadequate training, inadequate enforcement, or some combination thereof. They usually are the fault of company management.
You probably don’t have an OSHA-reportable situation unless the problem is systemic. Reporting one-offs to OSHA wastes their limited resources and will not improve safety in your company. Reporting one-offs to your supervisor and/or using your company’s recommended practices (such as asking a coworker to stop an unsafe act and tell him how it can be done safely) will contribute to making your company safer.
How to report
Before contacting OSHA, make a written list of the safety infractions. Look at the list; are these systemic or a collection of one-offs? What is the response from management when such things are reported? The agency is looking for systemic problems that management is not making an effort to resolve. If this is what you can document, then contact OSHA,
Don’t claim you found an OSHA violation unless you are well-versed in the OSHA regulations and have conducted a thorough review of the company’s safety program. Citations tend to be for violations at the program level, not for an individual instance of a particular safety violation.
For example, if you see an individual violate lockout/tagout, that’s a safety violation. If you see this occurring frequently and management is aware of it but doesn’t act to stop the problem, then there is likely an OSHA violation. Remember, it’s about systemic issues, not about one-offs.
You can submit your complaint online. However, if you call OSHA, then ask the OSHA rep if this situation appears to call for further action from the agency. If the answer is negative, ask for advice on what you should do next. If the answer is affirmative, thank the OSHA rep and let the agency create a case; you are done involving yourself at this point.
Don’t expect immediate results. There may not be any results, given how thinly OSHA is stretched. If you feel your place of work is inordinately dangerous and management isn’t addressing the dangers, then you need to quit. There is a severe shortage of electricians; you should have no problem finding another job at a company where safety matters.
Does quitting seem too drastic? It didn’t in 2005 for the safety director at the Texas City Refinery when he could not get action from corporate. He said he was quitting, but they convinced him to stay on until they could find someone to replace him. Three days after that conversation, he was among the 15 people killed in an explosion (180 others were injured).
Ultimately, your safety is your responsibility.
About the Author
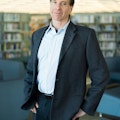
Mark Lamendola
Mark is an expert in maintenance management, having racked up an impressive track record during his time working in the field. He also has extensive knowledge of, and practical expertise with, the National Electrical Code (NEC). Through his consulting business, he provides articles and training materials on electrical topics, specializing in making difficult subjects easy to understand and focusing on the practical aspects of electrical work.
Prior to starting his own business, Mark served as the Technical Editor on EC&M for six years, worked three years in nuclear maintenance, six years as a contract project engineer/project manager, three years as a systems engineer, and three years in plant maintenance management.
Mark earned an AAS degree from Rock Valley College, a BSEET from Columbia Pacific University, and an MBA from Lake Erie College. He’s also completed several related certifications over the years and even was formerly licensed as a Master Electrician. He is a Senior Member of the IEEE and past Chairman of the Kansas City Chapters of both the IEEE and the IEEE Computer Society. Mark also served as the program director for, a board member of, and webmaster of, the Midwest Chapter of the 7x24 Exchange. He has also held memberships with the following organizations: NETA, NFPA, International Association of Webmasters, and Institute of Certified Professional Managers.