Many people who work in the field assume it’s management’s job to report violations of safety practices related to working at elevation. Is this assumption reasonable? Not considering last year’s top 10 OSHA violations: Fall protection general requirements is No. 1 on the list with 5,271 violations.
The news gets worse:
- No. 3, ladders, 2,018 violations
- No. 4, scaffolding, 1,943 violations
- No. 7, fall protection, 1,660 Violations
Keep in mind that these are violations documented by an OSHA inspector. It’s tip of the iceberg stuff. So no, you can’t totally rely on management to somehow prevent fall hazard safety violations. It really is a team assignment.
Many people who understand that it’s a team assignment believe their role is to report violations to management. The theory behind this belief is violations exist because management can’t be everywhere and see everything, so informing management solves the violation problem.
However, reporting doesn’t always result in solutions to poor attitudes, training deficiencies, equipment defects, inadequate procedures, and other problems that result in gravity-related safety violations occupying three of the top five slots and four of the top 10 slots in OSHA’s tally.
Your reporting responsibilities fall into two areas; one of those reporting responsibility areas includes your own work. Let’s look at that first.
Reporting your own issues
Issues can arise in the course of elevated work where you either stop work to address the problem or you unsafely forge ahead. Examples include:
- Inadequate equipment for the application. For example, a ladder of adequate height or correct type is not available or ladder does not have correct feet for the surface.
- Procedure has a “hole” in it. For example, there is a tie-off eye on the platform, but the procedure doesn’t note this. Or the procedure says to tie off, but there’s no tie-off point at the location.
- PPE is missing or damaged. For example, you notice the harness you were going to wear has a frayed stitch.
- Fall protection equipment is damaged. For example, a bolted guard rail system has loose bolts.
Your response in such cases should be:
- Stop work.
- Identify the exact problem.
- Identify possible solutions.
- Report to your foreman.
- Obtain resolution.
The resolution may be to go onto another job until this one can be made safe or to make this one safe. For example, you aren’t a qualified welder, so you can’t weld a tie-off in if that’s the defect. However, you can check out a different harness if the issue is a damaged harness.
Reporting others’ issues
If a coworker is committing an unsafe act, what should you do?
- Keep silent and wait for your coworker to fall to his death.
- Make a note to report the behavior to your supervisor and hope your supervisor can address the problem before your coworker falls to his death.
- Show your coworker you care by asking him to stop work and discuss the unsafe act.
Did you even have to think about which answer is correct? Here is how you do it:
- Ask your coworker to stop work.
- Ask your coworker to Identify the exact problem.
- Ask your coworker to identify possible solutions.
- Ask your coworker to report the exchange to his foreman if doing so will identify a training need or other issue management can correct.
- Ask your coworker to obtain a resolution.
Do you see how similar this is to handling your own safety issues?
In any good company, individual managers and management as a whole will be responsive to safety issues. Make their job easier by:
- Clearly identifying the issue. Exactly what is the problem and where?
- Providing possible solutions. Ask the individual you reported to (e.g., your supervisor or the safety director) what he thinks of your proposed solution(s). Will this solve the problem? How soon might it be implemented?
- Asking for feedback. Ask the individual you reported to when you can expect feedback on the issue(s) resolution.
- Following up. Check back with them after a reasonable time.
This process works for all safety issues. However, if it is used consistently with each fall safety issue, any company that has the normal distribution of violations can see four of the top 10 OSHA violations disappear from their own safety audits. And of course, it will protect you and your coworkers from a fatal injury.
About the Author
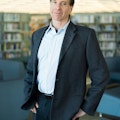
Mark Lamendola
Mark is an expert in maintenance management, having racked up an impressive track record during his time working in the field. He also has extensive knowledge of, and practical expertise with, the National Electrical Code (NEC). Through his consulting business, he provides articles and training materials on electrical topics, specializing in making difficult subjects easy to understand and focusing on the practical aspects of electrical work.
Prior to starting his own business, Mark served as the Technical Editor on EC&M for six years, worked three years in nuclear maintenance, six years as a contract project engineer/project manager, three years as a systems engineer, and three years in plant maintenance management.
Mark earned an AAS degree from Rock Valley College, a BSEET from Columbia Pacific University, and an MBA from Lake Erie College. He’s also completed several related certifications over the years and even was formerly licensed as a Master Electrician. He is a Senior Member of the IEEE and past Chairman of the Kansas City Chapters of both the IEEE and the IEEE Computer Society. Mark also served as the program director for, a board member of, and webmaster of, the Midwest Chapter of the 7x24 Exchange. He has also held memberships with the following organizations: NETA, NFPA, International Association of Webmasters, and Institute of Certified Professional Managers.