Last year, the No. 1 most cited OSHA violation was for failing to meet the general requirements for fall protection as provided in 29CFR1926.50. The requirements are fairly detailed, so it’s understandable that an employer might miss one or a few if the employer relies on a prescriptive approach to safety.
Some general themes run through these; for example, OSHA rules apply if the employee might fall 6 ft or more. So, the employer could train employees and their supervisors to question every elevation above 6 ft and identify what would be needed to prevent a fall.
Suppose a working surface is a mezzanine 10 ft above the floor below it and one side of that is open. What could keep people from accidentally plunging over that side? A guardrail system might work. Perhaps the side is open to facilitate moving material up to the mezzanine via lift truck or hoist. The guardrail could be removable, with a procedure in place that requires putting it back as soon as the material movement has been completed. Or perhaps it is possible to move the material over the guardrail.
The first option would satisfy 1926.501(b)(1) as long as the mezzanine is not a working surface during this operation. The second option would satisfy it all the time.
Maybe installing a guardrail there is not feasible. Or the work needs to be done now and there’s no time to install a guardrail first. A safety net system or a personal fall arrest system would protect the employee while also satisfying the OSHA requirement. Notice the order there: Think first of how to protect the employee.
Employee protection: Look for fall hazards
Protecting the employee is the purpose of the OSHA requirements. If your focus is on trying to remember particular requirements, you will inevitably violate a few. If your focus is on identifying potential hazards and then protecting against them, you can turn to OSHA regs (or the company’s safety policies) for recommendations in the form of requirements.
Anyone looking at a 10-ft mezzanine with an open side should have a mental alarm bell go off. But the reality is that mental alarm bell is on snooze far too often. OSHA fines the companies, which should get management’s attention. But the very fact that OSHA has to get their attention is a problem. Employees who encounter fall hazards are the ones with the most to lose (loss of life, for example) and, therefore, are the ones with the most incentive to get management’s attention.
Also, consider the fact that OSHA usually won’t fine a company if the fall height is less than 6 ft, even though somebody can fatally fall from a lesser height. And maybe they won’t fine the company if personal fall protection was used but it had already taken several hard falls and was more than five years old. Who really wins if a fine is avoided, but someone is seriously or fatally injured? What if that someone is you?
Nobody can write a list of safety rules that will provide complete protection, and OSHA is no exception. Before you work at elevation, take the time to survey that elevation. Visually scan each side, then the area between the sides, for fall hazards. Is there any way gravity could pull you over an edge or through a hole?
For each hazard that exists, identify an approved means of protection. It’s at this stage where employees should be communicating with their supervisor about what solution is the most effective and what can realistically be implemented. Solutions are preferred in this order:
- Design the problem out (risk elimination). For example, a maintenance procedure involves taking vibration readings on HVAC motors that are on an open mezzanine. Install vibration sensors on the motors, thus eliminating the manual task.
- Provide a permanent means of stopping the hazard. For example, install a guardrail on that mezzanine so it’s no longer open.
- Provide a means of protecting personnel from the hazard. For example, install a safety net.
- Provide PPE as a supplement to other measures or as a last resort. Many people jump right to using PPE, but itis the weakest form of protection.
About the Author
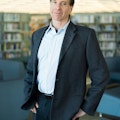
Mark Lamendola
Mark is an expert in maintenance management, having racked up an impressive track record during his time working in the field. He also has extensive knowledge of, and practical expertise with, the National Electrical Code (NEC). Through his consulting business, he provides articles and training materials on electrical topics, specializing in making difficult subjects easy to understand and focusing on the practical aspects of electrical work.
Prior to starting his own business, Mark served as the Technical Editor on EC&M for six years, worked three years in nuclear maintenance, six years as a contract project engineer/project manager, three years as a systems engineer, and three years in plant maintenance management.
Mark earned an AAS degree from Rock Valley College, a BSEET from Columbia Pacific University, and an MBA from Lake Erie College. He’s also completed several related certifications over the years and even was formerly licensed as a Master Electrician. He is a Senior Member of the IEEE and past Chairman of the Kansas City Chapters of both the IEEE and the IEEE Computer Society. Mark also served as the program director for, a board member of, and webmaster of, the Midwest Chapter of the 7x24 Exchange. He has also held memberships with the following organizations: NETA, NFPA, International Association of Webmasters, and Institute of Certified Professional Managers.