The job briefing is an indispensable tool for reducing safety problems on the job. But it is not an infallible tool because the person who provides the briefing isn’t infallible. To expose undisclosed dangers, start with the briefing. Be alert to the possibility of incomplete information. For example, if the job is in an operating plant and the person giving the briefing never mentions a process shutdown, coordinating with operators, or the like, then the briefing is probably missing important information that should have been included.
At a pulp mill in South Carolina, a crew was assigned to perform a series of wiring checks on the top floor of a six-floor building. The foreman spoke with an operator he happened to see near the building. He asked, “Do you know of anything that might be a safety issue from an operations standpoint if we go into that building?” The operator said he didn’t.
During the job briefing, the foreman noted that there was no activity in the building but the client requires everyone to carry an escape respirator anyhow — one more thing to carry up six flights of stairs. While they were setting up for the job, one of the electricians realized he’d forgotten a piece of test equipment and said he’d go down and get it.
As he exited the stairwell onto the first floor, a powerful smell greeted him. He backed into the stairwell and put on his emergency respirator then exited again. Two operators, both wearing hooded chemical suits and full respirators, had just opened a valve that vented sulfur dioxide.
The mistake the foreman made was he did not check in at the control station to ask the site operator what was scheduled and where. A single operator not assigned to a given task would not necessarily be aware that anyone else is engaged in that task. Further, the foreman should have registered his work plan with the site operator; this alone would have prevented the entire episode.
Safety lessons
• Lesson One: Before working up a job briefing, survey the entire path taken to the work location. Note what potential dangers (e.g., sulfur dioxide) are present and then contact the people who have authority over a given area to coordinate your work with their master schedule and also be apprised of any potential dangers associated with that particular equipment and/or location.
On the way into the building, any member of the crew would have seen the big “Sulfur Dioxide” signs and could have asked why the site operator didn’t assign an operator to be an attendant for the duration of this task. And therein lies …
• Lesson Two: As you encounter a potential danger, ask the foreman (or whoever gave the job briefing) what specific prevention measures were taken or why a specific measure was not taken.
Suppose in this situation it wasn’t the electricians who failed to check in with the site operator; they have clearance to be in that building. As they enter, they see two guys in canary suits and full-face charcoal canister respirators. Who are they to presume the site operator doesn’t know what he’s doing?
Well, the answer is they need to assume anybody can make a mistake and they need to be alert to things that are out of place — such as two guys dressed for a chemical release in a building where you’re about to do electrical work. Maybe they just grabbed a work order from the pile instead of waiting for an assignment, so the site operator didn’t know.
If the whole crew was chatting about last night’s ball game and didn’t notice those two operators, another layer of danger would have been added to this situation. And therein lies …
• Lesson Three: Take the time to actively and methodically look for dangers before you enter an area and periodically after you do. Something that nobody had anticipated could happen. This is how you notice things like spills, leaks, tripping hazards, and other unexpected dangers or abnormal conditions.
A thermographer worked for an electrical services firm in western Tennessee. Before entering an electrical equipment room at a mid-sized manufacturing plant, he paused at the door. He visually scanned the room. He noticed several enclosures with bolts missing from their covers.
So, he refused to enter to perform the thermography. In his report, he noted that the UL label of each enclosure was based on that enclosure being properly sealed closed. When only four of the 12 bolts that hold a cover in place are actually in the cover, that enclosure is not able to meet its safety requirements.
The maintenance manager disagreed with this viewpoint, stating they were going to remove the covers anyhow. But the proper procedure is to remove one cover, perform the scan, and then replace the cover before moving on to the next enclosure. This failure on the part of plant maintenance to ensure the enclosures were properly maintained was an undisclosed danger.
You have five senses plus the “something isn’t right” sense. Always look, touch, smell, and listen (tasting isn’t generally advised). And if something doesn’t seem right, it’s probably not. Rather than dismiss it because there’s no obvious explanation, take the time to figure out what that is. Retracing your steps can often produce that Aha! moment.
About the Author
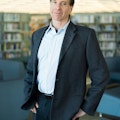
Mark Lamendola
Mark is an expert in maintenance management, having racked up an impressive track record during his time working in the field. He also has extensive knowledge of, and practical expertise with, the National Electrical Code (NEC). Through his consulting business, he provides articles and training materials on electrical topics, specializing in making difficult subjects easy to understand and focusing on the practical aspects of electrical work.
Prior to starting his own business, Mark served as the Technical Editor on EC&M for six years, worked three years in nuclear maintenance, six years as a contract project engineer/project manager, three years as a systems engineer, and three years in plant maintenance management.
Mark earned an AAS degree from Rock Valley College, a BSEET from Columbia Pacific University, and an MBA from Lake Erie College. He’s also completed several related certifications over the years and even was formerly licensed as a Master Electrician. He is a Senior Member of the IEEE and past Chairman of the Kansas City Chapters of both the IEEE and the IEEE Computer Society. Mark also served as the program director for, a board member of, and webmaster of, the Midwest Chapter of the 7x24 Exchange. He has also held memberships with the following organizations: NETA, NFPA, International Association of Webmasters, and Institute of Certified Professional Managers.