NFPA 70E says, “An electrical safety program shall identify the controls by which it is measured and monitored” [110.5(F)].
This traditionally meant employees would receive a barely comprehensible safety manual in all but the most forward-thinking companies. If their supervisor caught them doing something clearly unsafe, they would be written up.
Of course, the supervisor wasn’t familiar with that manual, so it was things like horseplay or not wearing safety glasses. An employee could skip hearing protection, lounge around energized equipment for no job-related reason (conducting bull sessions or eating lunch in the switchgear area wasn’t considered foolish), or commit 21 ladder safety violations and not get written up.
This “get caught by an unqualified person” control method isn’t the best way to control for safety. Fortunately, NFPA 70E, Annex E, provides eight examples of typical controls for companies where the concept has gotten proper attention from management and employees. These are paraphrased as follows:
- The employer develops the programs and procedures, then trains the employees, applying what they learned.
- Employees are trained to be qualified for the electrical environment they are working in.
- Employees and managers use procedures to identify electrical hazards and eliminate or control the risks.
- Every electrical conductor or circuit part is considered energized until proven otherwise. (This particular example has extensive implications for how work is performed. Take a few minutes to think about what those are).
- Deenergizing is considered a hazard in itself.
- Tasks to be performed within the limited approach boundary or flash boundary are identified and categorized.
- Management and employees identify and take the precautions needed for a given working environment.
- The associated risk of each task is determined with a logical approach.
These are just examples. But do you see how not among them is anything about being caught violating some rule? The emphasis is on empowering employees to identify hazards and protect themselves against those hazards.
Under this model, you don’t see employees snapping on their safety glasses when the supervisor is spotted coming their way. What you are more likely to see is an employee consulting with his or her supervisor on the best way to address an identified hazard.
How familiar are you with the controls of your electrical safety program? Do they make sense for the hazards you encounter or is something missing? How many years has it been since they were revised? Is your supervisor able to specify several of them from memory? Are you?
The controls are not something written down for posterity or to check off a box. They are meant to be integral to how you work. Take the time to understand them. If they are not adequate, then take the time to improve them.
About the Author
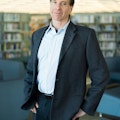
Mark Lamendola
Mark is an expert in maintenance management, having racked up an impressive track record during his time working in the field. He also has extensive knowledge of, and practical expertise with, the National Electrical Code (NEC). Through his consulting business, he provides articles and training materials on electrical topics, specializing in making difficult subjects easy to understand and focusing on the practical aspects of electrical work.
Prior to starting his own business, Mark served as the Technical Editor on EC&M for six years, worked three years in nuclear maintenance, six years as a contract project engineer/project manager, three years as a systems engineer, and three years in plant maintenance management.
Mark earned an AAS degree from Rock Valley College, a BSEET from Columbia Pacific University, and an MBA from Lake Erie College. He’s also completed several related certifications over the years and even was formerly licensed as a Master Electrician. He is a Senior Member of the IEEE and past Chairman of the Kansas City Chapters of both the IEEE and the IEEE Computer Society. Mark also served as the program director for, a board member of, and webmaster of, the Midwest Chapter of the 7x24 Exchange. He has also held memberships with the following organizations: NETA, NFPA, International Association of Webmasters, and Institute of Certified Professional Managers.