When it comes to using equipment in hazardous (classified) locations that is manufactured in other countries, what are the rules? What certifications are necessary, and how do you tell if equipment is safe for your application?
Hazardous (classified) locations contain flammable gas, liquids or vapors, combustible dust, or easily ignitable fiber and flyings. When one of these is combined with an oxidizer and ignition source, the result could be an explosion or fire.
In North America, equipment meeting relevant hazardous (classified) location certifications first must meet ordinary location requirements. These “ordinary” standards include but are not limited to:
- UL 94-VO standard for flammability.
- UL 489 for molded case circuit breakers.
- UL 50 and NEMA 250 standards for electrical enclosures.
- UL 1581 standard for electrical wires, cables, and flexible cords.
In our view, there is a common shortfall with not properly certified hazardous (classified) location solutions from overseas; they may not be tested to the general ordinary location American standards for suitability. In contrast, North American products applied in hazardous (classified) locations must first meet the requirements of ordinary locations before approval for hazardous areas may be achieved.
When no other product is available — and organizations need to use technology from outside of North America without proper certification — there are the National Electrical Code (NEC) and Occupational Safety and Health Administration (OSHA) exceptions. It’s essential to understand there is a tremendous liability to use those technologies if the equipment is not certified to North American standards.
Primer on zone equipment certification
The Zone method has become a worldwide accepted practice for classifying hazardous (classified) locations. The International Electrotechnical Commission System for certification to standards relating to equipment for use in explosive atmospheres (IECEx System) lists 62 countries that are full members and an additional 26 as associate members. Many countries have their own directives and certification requirements for equipment approvals within their borders.
The Zone method in the United States dates back to 1996 and was first introduced by the NEC (Art. 505). It allows for parallel classification in the traditional NEC Art. 500 Division system.
In this method, Zone terminology was used as the international system for classification of hazardous locations containing flammable gasses, liquids or vapors, combustible dust, or ignitable flyings, which divided classified areas into three segments: Zone 0, Zone 1, or Zone 2 for gases/ vapors, and Zone 20, Zone 21, Zone 22, for combustible dust and ignitable flyings.
Today, Zone-rated equipment still requires certification of ordinary location requirements in the United States. The AEx marking (Figure below), developed by the American National Standards Institute (ANSI) and International Society of Automation (ISA), ensures that Zone equipment conforms with hazardous location requirements and the general ordinary location American safety standards. As such, the AEx symbol is a critical marking requirement within the Zone material nomenclature.
The Authority Having Jurisdiction (AHJ) and qualified testing labs have an essential role. The AHJ can approve equipment when there is sufficient safety data. Also, if the equipment is listed by a qualified lab, then the internals of the equipment do not need to be inspected, except to look for problems, changes, or damage.
What if an AEx-Zone or Division certified technology isn’t available?
Section 500.8(A) of the NEC addresses this possibility and indicates that the suitability of equipment is determined by one of the following:
- Equipment listing.
- Evidence of equipment evaluation from a qualified testing lab or AHJ.
- Evidence acceptable to the AHJ like a manufacturer’s self-evaluation or owner’s engineering judgment.
In our view, a manufacturer’s self-certification and owner’s engineering judgment must be carefully reviewed and only be considered when the decision-maker is fully confident that ordinary safety standards have been achieved. This evidence must also be accepted by the AHJ.
Furthermore, OSHA provides additional guidance and requirements for product allowance. OSHA 29 CFR 1910.399 defines acceptable equipment as:
- If it is determined safe by a nationally recognized testing lab.
- If it is inspected by another federal agency, or by a state, municipal, or other local authority responsible for enforcing occupational safety provisions of the NEC and found in compliance with the NEC.
- If the equipment is determined to be safe for its intended use by its manufacturer, based on test data, that the employer keeps and can provide for inspection.
Marked with AEx, listed by an NRTL
The OSHA and NEC allowances permit for a product to be approved for installation without third-party testing by a nationally recognized testing lab (NRTL) while OSHA lists 19 NRTLs on its website, including UL, CSA, ETL-Intertek, and FM.
However, both the OSHA and NEC language indicate the general rule is that equipment should be tested and listed by an NRTL — unless these avenues have been exhausted.
When thinking about electrical equipment without testing by an NRTL, it’s important to consider:
- Does the state or municipality where equipment is being installed have requirements only allowing for the installation of third-party evaluated equipment?
- Does the customer facility have requirements only allowing for installation of third-party NRTL-evaluated equipment?
- Who is shouldering the liability for the owner’s engineering judgment or self-evaluated equipment for suitability of ordinary and hazardous-area locations?
Facilities using the NEC zone classification of hazardous (classified) locations (Arts. 505 and 506) are governed by the approval requirements outlined in the NEC Articles for the wiring methods and equipment certification.
When zone method-rated equipment includes the AEx marking, it means the equipment is certified to the American standards per NEC Sec. 505.9(C) and Sec. 506.9 (C). The AEx marking ensures the zone equipment conforms with both hazardous (classified) location requirements and general safety American standards for ordinary locations. These certifications give customers confidence and trust in the equipment they’re applying.
Robert Potter is a field application specialist for Eaton. He can be reached at [email protected]. Richard Holub is an electrical engineering consultant for Dupont. He can be reached at [email protected].
About the Author
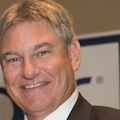
Robert C. Potter
Robert C. Potter Jr. is the Eastern Region field application specialist for Eaton’s Crouse-Hinds Business, with whom he has been employed for 25 years. His electrical industry career spans 39 years of service. Potter has served on the IEEE PCIC Executive Committee, was the Local Chair for the 2016 IEEE PCIC Philadelphia conference, and had been the PCIC Chair of the Facilities Sub-Committee. He has been twice published in IAS magazine and is a member of IEEE and IAS. In 2011, Potter had the honor of participating on a team proposing clarifications to the National Electrical Code that were approved for the 2014 edition. He has been presenting at the National Training Institute NJATC IBEW/ NECA annual conference in Ann Arbor, Mich., since 2015. Potter has also completed a draft for the new NEIS NECA-507 - Recommended Practices for Electrical Wiring and Equipment in Hazardous Locations standard.
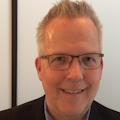
Richard A. Holub
Richard A. Holub is a principal electrical engineering consultant with DuPont Engineering in Wilmington, Del. He received a B.S. in Electrical Engineering from Clemson University in 1991, and an M.S. in Systems Engineering from Virginia Tech in 2000. Currently, Holub is a corporate consultant on the National Electrical Code, and consults on motors, adjustable speed drives, electric fire pump controllers, and uninterruptible power supplies. He is the alternate on CMP-14, the principal on the Correlating Committee, and the alternate on the Electrical Equipment in Chemical Atmospheres Committee representing the American Chemistry Council.