You work for an industrial services firm, and you are onsite to change out several pieces of busway during a planned shutdown. The customer is supplying the scissor lift for this job. You go to the first busway on the list, and find the scissor lift is about three feet short.
You’re working with an electrician employed by the customer. He sees the problem and says he’ll be right back with a stepladder. You ask if they have a taller lift instead, and he says no you’ll have to use a stepladder to get those last three feet.
What should you do at this point? The stepladder option is out, because that is unsafe. But calling your office to lease a lift has ramifications. For example, that’s an added cost the customer was supposed to cover. And what are you supposed to do while waiting for the replacement lift?
You need to call your office and let them sort out the logistics with your customer. You can tell them that while they are doing that you will scope out the job for busway the scissor lift can reach and work on that.
It is not your duty to work dangerously (e.g., step ladder on a lift) just because someone failed to properly scope out the job and identify the correct equipment to perform the work. If the company loses money because of that, it’s not your fault. It would be your fault if the company lost money because you worked unsafely. What would happen, for example, if the step ladder on the lift caused you to fall in such a way you short the bus and cause an arc fault? Or you go over the lift rail and splatter onto the floor below?
If you decided to be a real trooper and set the stepladder on that lift, you might get by with it. But the risk of falling is high. If you do fall, the job will be really delayed, you will be severely injured or dead, and your office will still have to work out the lift problem with the customer (assuming the customer lets your company on site again).
When you’re faced with a “stop work or be safe” dilemma, always choose to be safe. You can think through ways to work around the safety dilemma (as in this example, work on what you can reach), but you don’t want to try to work through the safety dilemma.
About the Author
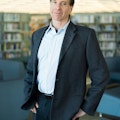
Mark Lamendola
Mark is an expert in maintenance management, having racked up an impressive track record during his time working in the field. He also has extensive knowledge of, and practical expertise with, the National Electrical Code (NEC). Through his consulting business, he provides articles and training materials on electrical topics, specializing in making difficult subjects easy to understand and focusing on the practical aspects of electrical work.
Prior to starting his own business, Mark served as the Technical Editor on EC&M for six years, worked three years in nuclear maintenance, six years as a contract project engineer/project manager, three years as a systems engineer, and three years in plant maintenance management.
Mark earned an AAS degree from Rock Valley College, a BSEET from Columbia Pacific University, and an MBA from Lake Erie College. He’s also completed several related certifications over the years and even was formerly licensed as a Master Electrician. He is a Senior Member of the IEEE and past Chairman of the Kansas City Chapters of both the IEEE and the IEEE Computer Society. Mark also served as the program director for, a board member of, and webmaster of, the Midwest Chapter of the 7x24 Exchange. He has also held memberships with the following organizations: NETA, NFPA, International Association of Webmasters, and Institute of Certified Professional Managers.