According to a recent National Fire Protection Association (NFPA) report, 126 workers died from exposure to electricity in 2020. Deaths from an arc flash are down from previous years, but most of these fatalities could have been prevented. Workers in highly charged areas can be exposed to electrical hazards that place them at risk of serious injury or death. Injuries occur when electrical safety is not given the proper attention, procedures are not followed, or employees are not trained appropriately. An arc flash blast can occur in a fraction of a second, resulting in skin burns, respiratory issues, hearing loss, eye damage, and death. Conducting an arc flash study helps organizations identify the likelihood of an arc flash hazard and is the first step in preventing it from occurring. This article will review the arc flash regulatory requirements, mitigation, and compliance strategies, consider the impact of an arc flash incident on employees and businesses, and provide a framework for developing an arc flash management program.
Arc flash and the risks involved
An arc flash is a sudden discharge of energy, connecting a component with the ground or another voltage phase in the same system through the air. This discharge can result from loose connections, exposed live parts, or other short circuits in faulty equipment. The resulting explosion produces dangerous intensities of force, heat, and light. In addition to damaging equipment, an arc flash can injure nearby workers. The impact can cause internal and external burns, resulting in severe injuries or death caused by intense UV light emissions, hot gases, or vaporized metals.
Across electrical systems, each equipment location will have a different arc flash incident risk level, depending on the available fault current and interrupting time to clear that fault. An arc flash analysis will detect the available fault current using a short-circuit study, and the interrupting time is calculated with a coordination study. These two protective device calculations are the basis for determining the arc flash incident energy in calories per centimeter squared, which provides the arc flash incident risk level. This information is included in the arc flash report, and the incident energy value will be included on device-specific arc flash equipment labels. When it is necessary to work on energized equipment, the arc flash label informs personnel of the magnitude of the potential hazard, so they can take appropriate steps to protect themselves with the proper personal protective equipment (PPE) and other safety procedures.
An arc flash study and proper arc flash labeling are required by law to reduce the hazard for workers when working on or near energized equipment. The study also simultaneously provides selective coordination of electrical system protective devices that will minimize interruptions to the operation of the facility's electrical infrastructure.
Maximizing employee safety and optimizing business operations
Establishing a risk management program for arc flash safety is the first step toward mitigating arc flash risk and ensuring worker safety while optimizing facility operation.
The NFPA 70E standard requires facility owners to perform an arc flash risk assessment before allowing a worker or contractor to perform a task on energized equipment. An arc flash risk assessment identifies the presence and location of potential hazards. It provides recommendations for PPE, boundaries for limited and restricted approaches, proposals for flash protection, and safe work practices. The Occupational Safety and Health Act (OSHA) requires all business owners to have an NFPA 70E-compliant safety program — including an arc flash risk assessment and labeling. OSHA strictly enforces these requirements, and violations can result in hundreds of thousands of dollars in fines. There are even examples of repeated violations costing more than a million dollars when incidents have resulted in serious injury or death.
Mitigating risk with an arc flash management program
An arc flash risk management program is comprised of a typical sequence of tasks conducted by the system owner or in conjunction with a third-party service provider to implement a personnel safety and system reliability solution.
- The first task in the sequence starts with a commitment by the system owner to define, document, and implement safe operating practices. This activity should include electrical safety and policy procedures. Many of these procedures are described in the NFPA 70E standard related to workplace electrical safety.
- Specific hazards should be identified by location across the electrical infrastructure. Details of the electrical system layout are required as the basis to define a scope of work for a risk management solution.
- End-users or approved third-party service providers will confirm system data on-site. This data will be used to model an electrical representation of the system to perform a short circuit, coordination, and arc flash analysis. The analysis is performed according to industry standards using an available software application. The application software will aid a knowledgeable systems engineer in calculating the available fault current. From these calculations, the engineer will recommend protective device settings that optimize system operation while minimizing the magnitude of the arc flash hazard.
- Results are documented by device, including actions to replace underrated devices that can't safely interrupt the available fault current and relay settings to support the approved recommendations of the study.
- Once the user approves the study results, equipment labels are produced and affixed to each piece of equipment. The labels provide all the necessary information a worker will require to wear appropriate PPE and define safe working distances for qualified and unqualified workers. These labels are then available for installation on the electrical devices as defined in the study.
- Labeling equipment is only a part of the overall process of operating safely. There are many safety procedures outlined in OSHA and NFPA 70E. These include a requirement to train personnel who may be working on or near energized equipment. NFPA 70E requires personnel to be trained every three years and audited for retention of safety policies/procedures each year.
The arc flash analysis documents and analyzes a user's existing system for what it is. It could be a relatively new state-of-the-art electrical system with the latest gear, a decades-old system with equipment that is no longer manufactured, or something in between. As a result, there are situations where the ability to reduce the magnitude of arc flash hazards has its limits while also providing desired protection device coordination for optimal system operations.
An arc flash analysis is essentially a snapshot in time. It documents the user’s electrical system as currently configured. Any changes to the system could invalidate all or a portion of the results provided in the study report. Accordingly, NFPA 70E requires the study to be rerun every five years or when significant changes have been made to the system. Periodic updates not only keep the study current to retain the benefits of safety and system reliability but also to make the ongoing implementation of an arc flash safety program less costly and complex.
In addition, NFPA 70E requires a current single-line diagram to be included in each arc flash update. The single-line diagram references each device in the model and is a critical component of the final arc flash report.
Arc flash labeling
Arc flash labels follow a specific layout according to NFPA 70E guidelines. See the Figure below for a detailed diagram of the arc flash-related information included on every label. Note that there may be some variations based on customer preference and historical safety procedures already in place. Changes to the standard in recent years include the elimination of the prohibited approach boundary for shock hazard and PPE category 0. PPE category designations of 1-4 are no longer required when the analysis method review in this article is used.
Arc flash training
Arc flash safety training, as mentioned above, is required every three years by OSHA 1910 and NFPA 70E. A typical arc flash safety course will include demonstrations on how to determine incident energy values and arc flash boundaries and instruct on how to interpret arc flash labeling. The information will guide participants in the selection of methods designed to minimize arc flash hazards and in choosing the proper PPE. A training course can be conducted in one day and should in general cover the following topics:
- Safety basics
- Electric flashover
- Arc flash and blast
- Codes and standards
- Standard maintenance requirements
- Work-safe practices
- Arc flash label interpretation
Arc flash safety compliance
OSHA1910, NFPA 70E, and IEEE 1584 are the primary standards that drive arc flash compliance activities. These standards provide policies and procedures that facilitate electrical safety. They have been developed and refined over time from real-world experience. OSHA requires employers to provide their employees with working conditions that are free of known dangers. It refers to NFPA 70E to fulfill the performance-based requirements in the OSHA standards. The purpose of NFPA 70E is to ensure workers are provided with a working area that is safe from the unacceptable risk associated with the use of electricity in the workplace. The IEEE1584 standard referenced in NFPA 70E provides the mathematical model used as the basis to calculate arc flash incident energy values. A review of these standards and how they are to be applied should be part of every discussion related to an arc flash management program.
Third-party service providers can help system owners comply with arc flash standards and assist with creating a custom arc flash management program. When hiring a third-party service provider, consider their ability to offer the following expertise and assurances:
- Trained and qualified field technicians experienced in performing on-site tasks including, data collection, labeling, relay settings, breaker testing, device replacement, and installation of an engineered solution.
- Expertise in single- and multi-site implementation.
- Qualified arc flash training programs to educate employees and measure understanding of safety procedures.
- System engineers to perform system analysis, review results and provide supporting documentation.
- Application engineering capabilities to advance and apply additional mitigation solutions.
- An approved process for managing system changes that support ongoing personnel safety and system reliability.
- A review and update of safety policy to ensure compliance with applicable codes and standards.
In summary
Arc flash incidents represent a significant risk to personnel, system performance, and company reputation. System owners by law are required to be actively involved in risk management, and accountability is not excused due to ignorance of the standards. NFPA 70E specifies safety training every three years and arc flash study updates every five years (or after changes have been made to the electrical system). Following these standards is essential to a safe and dependable operating environment. In the end, it’s all about safety and reliability.
Fred Toepfer, engineering services business development manager for Electrical Reliability Services, received his BSEE degree from Louisiana State University and MBA from Vanderbilt University. He has more than 30 years of sales and marketing experience in the electrical industry related to service and new product/business development. He can be reached at [email protected].
About the Author
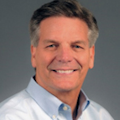
Fred Toepfer
Fred Toepfer, engineering services business development manager for Electrical Reliability Services, received his BSEE degree from Louisiana State University and MBA from Vanderbilt University. He has more than 30 years of sales and marketing experience in the electrical industry related to service and new product/business development.