Courtesy of www.MikeHolt.com.
All questions and answers are based on the 2020 NEC.
Underlined text indicates revisions made in the 2020 Edition of the NEC.
Q. What is the Code rule regarding the installation of grounding electrode conductors?
A. Grounding electrode conductors (GECs) must be installed as specified in Sec. 250.64(A) through (F).
(A) Aluminum and Copper-Clad Aluminum Conductors. Bare, covered, or insulated aluminum or copper-clad GECs must comply with the following:
(1) Bare or covered conductors without an extruded polymeric covering are not permitted to be installed where subject to corrosive conditions or to be installed in direct contact with concrete.
(2) Terminations made within listed enclosures identified for outdoor use are permitted within 18 in. of the bottom of the enclosure.
Author’s Comment: If open-bottom enclosures are installed on a concrete pad, the concrete is not considered earth.
(3) Aluminum or copper-clad aluminum conductors external to buildings or equipment enclosures are not permitted to be terminated within 18 in. of the earth.
(B) Conductor Protection. Where exposed, a GEC must be securely fastened to the surface on which it is carried. GECs can be installed on or through framing members.
(1) Not Exposed to Physical Damage. GECs 6 AWG and larger can be installed exposed along the surface of the building if securely fastened and not exposed to physical damage.
(2) Exposed to Physical Damage. GECs subject to physical damage must be protected in rigid metal conduit (RMC), intermediate metal conduit (IMC), Schedule 80 rigid polyvinyl chloride conduit (PVC), reinforced thermosetting resin conduit Type XW (RTRC-XW), electrical metallic tubing (EMT), or cable armor.
(3) Smaller Than 6 AWG. GECs smaller than 6 AWG must be protected in RMC, IMC, Schedule 80 PVC, RTRC-XW, EMT, or cable armor.
Author’s Comment: While Table 250.66 permits the use of 8 AWG copper as the GEC for the phase conductor sizes typically used for a 100A service, use of a GEC smaller than 6 AWG is not common.
(4) In Contact with the earth. GECs and bonding jumpers in contact with the earth are not required to comply with the cover requirements of Sec. 300.5 but must be protected where subject to physical damage.
(C) Continuous. GECs must be installed without a splice or joint except by:
(1) Irreversible compression‑type connectors or exothermic welding.
(2) Busbars connected together.
(3) Bolted, riveted, or welded connections of structural metal frames of buildings.
(4) Threaded, welded, brazed, soldered, or bolted‑flange connections of metal water piping.
(D) GEC for Multiple Building Disconnect Enclosures. If a building contains two or more service or feeder disconnects in separate enclosures, the grounding electrode connections must be made by any of the following methods:
(1) Common GEC and Taps. The unspliced common GEC must be sized in accordance with Sec. 250.66 based on the sum of the circular mil area of the largest phase conductor supplying the equipment (Figure below).
A GEC tap must extend from each disconnect, and it must be sized no smaller than specified in Table 250.66 based on the area of the largest phase conductor.
The GEC tap must be connected to the common GEC by any of the following methods:
(1) Exothermic welding.
(2) Connectors listed as grounding and bonding equipment.
(3) Connections to a busbar of sufficient length and not less than ¼ in. thick × 2 in. wide that is securely fastened and installed in an accessible location.
(2) Individual GECs. An individual GEC from each disconnect, sized in accordance with Sec. 250.66 based on the phase conductor(s) supplying the individual disconnect, must connect the grounding electrode system to one of the following:
(1) The service neutral conductor
(2) The equipment grounding conductor of the feeder circuit
(3) The supply‑side bonding jumper
(3) Supply Side of Disconnects. A GEC from an accessible enclosure on the supply side of the disconnects, sized in accordance with Sec. 250.66 and based on the phase conductor(s) supplying the disconnect, must connect the grounding electrode system to one of the following:
(1) The service neutral conductor.
(2) The equipment grounding conductor of the feeder circuit.
(3) The supply‑side bonding jumper.
(E) Ferrous Raceways Containing GECs
(1) General. To prevent inductive choking of GECs, ferrous metal raceways, enclosures, and cable armor containing GECs must have each end of the raceway or enclosure bonded to the GEC.
(2) Methods. Raceway bonding must be done in accordance with Sec. 250.92(B)(2) through (B)(4).
(3) Size. Bonding jumpers must be the same size or larger than the largest GEC in the raceway or other enclosure.
Author’s Comment:
- Nonferrous metal raceways, such as aluminum rigid metal conduit, enclosing the GEC are not required to meet the “bonding each end of the raceway to the grounding electrode conductor” provisions of this section.
- To save a lot of time and effort, install the GEC in a nonmetallic raceway suitable for the application. Schedule 40 PVC can be used for exposed work, but Schedule 80 PVC is required in areas subject to physical damage [Sec. 352.10(F)].
These materials are provided to us by Mike Holt Enterprises in Leesburg, Fla. To view Code training materials offered by this company, visit www.mikeholt.com/code.
About the Author
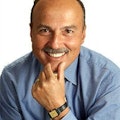
Mike Holt
Mike Holt is the owner of Mike Holt Enterprises (www.MikeHolt.com), one of the largest electrical publishers in the United States. He earned a master's degree in the Business Administration Program (MBA) from the University of Miami. He earned his reputation as a National Electrical Code (NEC) expert by working his way up through the electrical trade. Formally a construction editor for two different trade publications, Mike started his career as an apprentice electrician and eventually became a master electrician, an electrical inspector, a contractor, and an educator. Mike has taught more than 1,000 classes on 30 different electrical-related subjects — ranging from alarm installations to exam preparation and voltage drop calculations. He continues to produce seminars, videos, books, and online training for the trade as well as contribute monthly Code content to EC&M magazine.