Article 408 covers the specific requirements for switchboards and panelboards that control power and lighting circuits. When applying these rules, keep in mind that a major objective is to prevent contact between current-carrying conductors and people or equipment.
If you mount a panelboard in the face-up position, then you increase the likelihood that circuit breakers and buses will accumulate contamination. This orientation also complicates meeting minimum workspace requirements. Thus, with a 2020 revision, it is now prohibited [Sec. 408.43].
Is your panelboard job being done in a neat and workmanlike manner [Sec. 110.12]? To do so, ensure the panel enclosures are level; shim if you must. Pay attention to mechanical aspects such as mounting bolt torque (and whether those bolts are torqued dry or lubricated, per the manufacturer’s instructions [Sec. 110.3(B)]. As you proceed with the installation, address workmanship issues at each step.
Bus bars and conductor arrangement
Panelboards supplied by a 4-wire, delta-connected, 3-phase (high-leg) system must have the high-leg conductor (which operates at 208V to ground) terminate to the “B” phase of the panelboard [Sec. 408.3(E)(1)] (Fig. 1).On a 4-wire, delta-connected, 3-phase system where the midpoint of one phase winding of the secondary is grounded, the conductor with the resulting 208V to ground (high-leg) must be durably and permanently marked by an outer finish (insulation) that is orange in color or other effective means. Such identification must be placed at each point where a connection is made if the neutral conductor is present [Sec. 110.15 and Sec. 230.56].
The ANSI standard for meter equipment requires the high-leg conductor (208V to neutral) to terminate on the “C” (right) phase of the meter socket enclosure. This is because the demand meter needs 120V, and it gets it from the “B” phase.
When replacing equipment in existing facilities that contain a high-leg conductor, be certain to replace the high-leg conductor in the same phase position. Prior to 1975, the high-leg conductor was required to terminate on the “C” phase of panelboards and switchboards. Failure to re-terminate the high-leg per the existing installation can result in 120V circuits being inadvertently connected to the 208V high-leg, with disastrous results.
Your ID, please
Article 408 requires various identification labels to help prevent confusion during maintenance, repair, upgrades, or emergencies.
A switchboard or panelboard containing a 4-wire, delta-connected system where the midpoint of one phase winding is grounded must have a label that is legibly and permanently field marked as follows: “CAUTION _____ PHASE HAS _____ VOLTS TO GROUND” [Sec. 408.3(F)(1)].
Circuits and circuit modifications must be legibly identified as to their clear, evident, and specific purpose [Sec. 408.4(A)]. Circuit identification must not be based on transient conditions of occupancy, such as “Dad’s Office” [Sec. 408.4(A)].
Identification must include sufficient detail to allow each circuit to be distinguished from all others, and the identification must be on a circuit directory. The directory must be on the face or inside of, in an approved location adjacent to or on the door of the panelboard [Sec. 110.22].
Switchboards and panelboards supplied by a feeder in other than one‑ or two‑family dwellings must be marked with a permanent, machine-printed label that withstands the environment. This label must indicate where the power supply originates [408.4(B)].
Short-circuit current rating
Switchboards and panelboards must have a short-circuit current rating of at least the available fault current [Sec. 408.6].
In other than one- and two-family dwellings, the available fault current and the date the calculation was performed must be field marked on the enclosure at the point of supply. The marking must be of sufficient durability to withstand the environment involved per Sec. 110.21(B)(3).
Raceway clearances and openings
If raceways enter a switchboard, floor-standing panelboard, or similar enclosure, the raceways (including end fittings) are not permitted to rise more than 3 in. above the bottom of the enclosure [Sec. 408.5].
Unused openings for circuit breakers must be closed using identified closures or other approved means that provide protection substantially equivalent to the wall of the enclosure [Sec. 408.7].
Equipment reconditioning
The reconditioning process must use design-qualified parts verified under applicable standards. It must be performed per any instructions provided by the manufacturer [Sec. 408.8]. If equipment has been damaged by fire, products of combustion, or water, it must be specifically evaluated by its manufacturer or a qualified testing laboratory prior to being returned to service.
You cannot recondition a panelboard, so replacement is your only option if one is in poor shape. If the replacement panelboard has not been listed for the specific enclosure and the available fault current is greater than 10,000A, then the completed work must be field labeled. Remove any previously applied listing marks on the cabinet [Sec. 408.8(A)].
You can recondition switchboards or sections of switchboards. Reconditioned switchboards must be listed or field labeled as reconditioned. Remove any previously applied listing marks [Sec. 408.8(B)].
Clearances for switchboards and switchgear
For other than a totally enclosed switchboard or switchgear, provide a space of at least 3 ft between the top of the switchboard or switchgear and any combustible ceiling. This requirement is waived if you provide a noncombustible shield between the switchboard or switchgear and the ceiling [Sec. 408.18(A)].
Clearances around switchboards and switchgear must comply with Sec. 110.26. [Sec. 408.18(B)]. The focus there is working space. OSHA takes its working space requirements directly from this part of the NEC. Those are bare minimums. Conditions of operation or maintenance in an installation may call for additional working space.
Each section of equipment that requires rear or side access to make field connections must be so marked in the front by the manufacturer. Section openings requiring rear or side access must comply with the workspace and access to workspace requirements of Sec. 110.26 [Sec. 408.18(C)].
Overcurrent protection for panelboards
Panelboards must have overcurrent protection within or at any point on the supply side of the panelboard with a rating not greater than that of the panelboard [Sec. 408.36].
When a panelboard is supplied from a transformer, as permitted in Sec. 240.21(C), the overcurrent protection for the panelboard must be on the secondary side of the transformer. You can install the overcurrent in an enclosure ahead of the panelboard or within the panelboard [Sec. 408.36(B)] (Fig. 2).You cannot install delta breakers in panelboards. You cannot connect a 3-phase disconnect or overcurrent device to the bus of any panelboard that has less than 3-phase buses [Sec. 408.36(C)].
Plug-in circuit breakers that are backfed must be secured in place by a fastener that requires other than a pull to release the breaker from the panelboard [Sec. 408.36(D)].
The breaker fastener prevents the circuit breaker from being removed from the panelboard while energized. The removal would expose someone to dangerous voltage.
Breakers marked “Line” and “Load” must be installed per listing or labeling instructions [Sec. 110.3(B)]; therefore, these types of devices cannot be back-fed.
Panelboards in damp or wet locations
Cabinets for panelboards installed in damp or wet locations must be weatherproof per Sec. 312.2 [Sec. 408.37]. The main concept of that requirement is you place or equip the enclosure to prevent moisture or water from entering and accumulating within the enclosure.
Be sure to use enclosures and fittings listed for wet locations. The same goes for mounting hardware. Zinc-plated bolts and washers cost considerably more, but they won’t leave rust stains running down the enclosure like uncoated versions do.
Equipment grounding conductor
Metal cabinets containing panelboards must be connected to an equipment grounding conductor (EGC) of a type recognized in Sec. 250.118 [Sec. 215.6 and Sec. 250.4(A)(3)]. Where a panelboard cabinet contains EGCs of the wire type, a terminal bar for the EGCs must be installed and bonded to the metal cabinet [Sec. 480.40] (Fig. 3).EGCs are not permitted to terminate on the neutral terminal bar except as permitted by Sec. 250.142(A) for services and separately derived systems.
Many panelboards are rated for use as service disconnects, which means they are supplied with a main bonding jumper [Sec. 250.28]. You cannot install this screw or strap except when the panelboard is used for a service disconnect [Sec. 250.24(A)(5)] or a separately derived system [Sec. 250.30(A)(1)].
Neutral conductor terminations
Each neutral conductor within a panelboard must terminate to an individual terminal [Sec. 480.41].
If two neutral conductors are connected to the same terminal and someone removes one of them, then the other neutral conductor might unintentionally also be removed. If that happens to the neutral conductor of a multiwire circuit, it can result in excessive line-to-neutral voltage for one of the circuits, plus undervoltage for the other circuit.
Avoiding rework
It is costly to fix errors once an installation is complete. You will save time and money by performing a mini review at each major stage of the job. This process can be quickly and efficiently done if you mark on the drawings and/or work plan the specific Code references that apply.
These materials are provided to us by Mike Holt Enterprises in Leesburg, Fla. To view Code training materials offered by this company, visit www.mikeholt.com/code.
About the Author
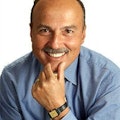
Mike Holt
Mike Holt is the owner of Mike Holt Enterprises (www.MikeHolt.com), one of the largest electrical publishers in the United States. He earned a master's degree in the Business Administration Program (MBA) from the University of Miami. He earned his reputation as a National Electrical Code (NEC) expert by working his way up through the electrical trade. Formally a construction editor for two different trade publications, Mike started his career as an apprentice electrician and eventually became a master electrician, an electrical inspector, a contractor, and an educator. Mike has taught more than 1,000 classes on 30 different electrical-related subjects — ranging from alarm installations to exam preparation and voltage drop calculations. He continues to produce seminars, videos, books, and online training for the trade as well as contribute monthly Code content to EC&M magazine.