Aluminum grounding conductors cannot be in contact with earth, masonry, or subjected to corrosive conditions. When used outdoors, the termination to the electrode must not be within 18 inches of earth.
Where exposed, grounding electrode conductors sized 8 AWG and smaller must be installed in rigid metal conduit, intermediate metal conduit, rigid nonmetallic conduit, or electrical metallic tubing. Ferrous metal raceways containing the grounding electrode conductors must be made electrically continuous by bonding each end of the ferrous metal raceway to the grounding electrode conductor [250.64(E)]. Grounding electrode conductors 6 AWG copper and larger can be run exposed along the surface if securely fastened to the construction and not subject to physical damage.
The grounding electrode conductor, which runs to any convenient grounding electrode [250.64(F)], must not be spliced, except as permitted in (1) through (3):
- Splicing is permitted by irreversible compression-type connectors listed for grounding or by exothermic welding.
- Sections of busbars can be connected together to form a grounding electrode conductor.
- Bonding and grounding electrode conductors are permitted to terminate to a busbar that is sized not smaller than ¼ x 2 inches, and the busbar must be securely fastened in place at an accessible location. Connections must be made by a listed connector or by the exothermic welding process.
When a service consists of multiple disconnecting means as permitted in 230.71(A), a grounding electrode tap from each disconnect to a common grounding electrode conductor is permitted. The grounding electrode tap must be sized in accordance with 250.66, based on the largest ungrounded conductor serving that disconnect. The common grounding electrode conductor for the grounding electrode taps is also sized in accordance with 250.66, based on the service conductors feeding all the service disconnects. Each grounding electrode tap must terminate to the common grounding electrode conductor in such a manner that there will be no splices or joints in the common grounding electrode conductor.
Ferrous (iron/steel) raceways, boxes, and enclosures containing the grounding electrode conductors must have each end of the ferrous metal raceway, box, and enclosure bonded to the grounding electrode conductor [250.92(A)(3)]. “Nonferrous” metal raceways, such as aluminum rigid metal conduit, enclosing the grounding electrode conductor aren’t required to meet the “bonding each end of the raceway to the grounding electrode conductor” provisions of this section.
The bonding jumper must be sized no smaller than the enclosed grounding electrode conductor. Caution: The effectiveness of the grounding electrode can be significantly reduced if ferromagnetic raceway containing a grounding electrode conductor isn’t bonded to the grounding electrode conductor at both ends. This is because a single conductor carrying high-frequency lightning current in a ferrous raceway causes the raceway to act as an inductor, which severely limits (chokes) the current flow through the grounding electrode conductor. ANSI/IEEE 142, Recommended Practice for Grounding of Industrial and Commercial Power Systems (Green Book) states, “An inductive choke can reduce current flow by 97%.” To save a lot of time and effort, simply run the grounding electrode conductor exposed if not subject to physical damage [250.64(B)], or enclose it in a nonmetallic conduit that is suitable for the application.
The grounding electrode conductor can be run to any convenient grounding electrode available in the grounding electrode (earthing) system. The grounding electrode conductor must be sized for the largest grounding electrode conductor required among all the electrodes connected to it. It is not necessary to run the grounding electrode conductor to all of the electrodes unbroken, just to the first electrode.
Editor’s note: This information was extracted from Mike Holt’s textbook, Understanding the National Electrical Code.
About the Author
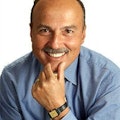
Mike Holt
Mike Holt is the owner of Mike Holt Enterprises (www.MikeHolt.com), one of the largest electrical publishers in the United States. He earned a master's degree in the Business Administration Program (MBA) from the University of Miami. He earned his reputation as a National Electrical Code (NEC) expert by working his way up through the electrical trade. Formally a construction editor for two different trade publications, Mike started his career as an apprentice electrician and eventually became a master electrician, an electrical inspector, a contractor, and an educator. Mike has taught more than 1,000 classes on 30 different electrical-related subjects — ranging from alarm installations to exam preparation and voltage drop calculations. He continues to produce seminars, videos, books, and online training for the trade as well as contribute monthly Code content to EC&M magazine.