To remove dangerous voltage on metal parts from a ground fault, electrically conductive metal water piping systems, metal sprinkler piping, metal gas piping, and other metal piping systems, as well as exposed structural steel members that are likely to become energized, must be bonded to an effective ground-fault current path [250.4(A)(4)]. Although bonding isn’t required for isolated sections of metal water piping connected to a nonmetallic water piping system, metal water piping systems must be bonded in accordance with the following:
- Building Supplied by a Service. The metal water piping system of a building or structure must be bonded to one of the following: service equipment enclosure; grounded neutral service conductor; grounding electrode conductor where the grounding electrode conductor is sized in accordance with Table 250.66; or one of the electrodes of the grounding electrode system. The metal water pipe bonding jumper must be sized in accordance with Table 250.66, based on the largest ungrounded service conductor. Where hot and cold water pipes are electrically connected, only one bonding jumper is required, either to the cold or hot water pipe. Otherwise, a single bonding jumper, sized in accordance with 250.104(A)(1), must be used to bond the hot and cold water piping together.
- Multiple Occupancy Building. When the metal water piping system in an individual occupancy is metallically isolated from other occupancies, the metal water piping system for that occupancy can be bonded to the equipment grounding terminal of the occupancy’s panelboard. The bonding jumper used for this purpose must be sized to the ampere rating of the occupancy’s feeder overcurrent protection device in accordance with Table 250.122.
- Building or Structure Supplied by a Feeder. The metal water piping system of a building or structure that is supplied by a feeder must be bonded to: the equipment grounding terminal of the building disconnect enclosure; the feeder equipment grounding (bonding) conductor; or one of the electrodes of the grounding electrode system. The bonding jumper for the metal water piping system must be sized to the feeder circuit conductors that supply the building or structure in accordance with Table 250.66. The bonding jumper is not required to be larger than the ungrounded feeder conductors. Note: It makes no sense to size the metal water piping bonding jumper in accordance with Table 250.66, based on the feeder circuit conductor size. The bonding jumper should be sized in accordance with Table 250.122, based on the building or structure feeder overcurrent protection device.
Other metal piping systems such as gas or air that are likely to become energized must be bonded to an effective ground-fault current path. The equipment grounding (bonding) conductor for the circuit that may energize the piping can serve as the bonding means. (See NFPA 54, National Fuel Gas Code) Because the equipment grounding (bonding) conductor for the circuit that may energize the piping can serve as the bonding means, no action is required by the electrical installer.
Exposed structural metal that forms a metal building frame that is likely to become energized must be bonded to: service equipment enclosure; grounded neutral service conductor; grounding electrode conductor where the grounding electrode conductor is sized in accordance with Table 250.66; one of the electrodes of the grounding electrode system. This rule does not require the bonding of sheet metal framing members (studs) or the metal skin of a wood frame building, but it would be a good practice.
The bonding jumper for the structural metal must be sized to the feeder or service conductors that supply the building or structure in accordance with Table 250.66, and the bonding jumper must be: copper where within 18 inches of earth [250.64(A)]; securely fastened and adequately protected if exposed to physical damage [250.64(B)]; and installed without a splice or joint, unless spliced by irreversible compression connectors listed for the purpose or by the exothermic welding process [250.64(C)].
For specific requirements when working with separately derived systems, see 250.104(D)(1), 250.104(D)(2), and 250.104(D)(3).
Editor’s note: This information was extracted from Mike Holt’s textbook, Understanding the National Electrical Code.
About the Author
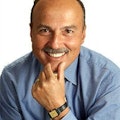
Mike Holt
Mike Holt is the owner of Mike Holt Enterprises (www.MikeHolt.com), one of the largest electrical publishers in the United States. He earned a master's degree in the Business Administration Program (MBA) from the University of Miami. He earned his reputation as a National Electrical Code (NEC) expert by working his way up through the electrical trade. Formally a construction editor for two different trade publications, Mike started his career as an apprentice electrician and eventually became a master electrician, an electrical inspector, a contractor, and an educator. Mike has taught more than 1,000 classes on 30 different electrical-related subjects — ranging from alarm installations to exam preparation and voltage drop calculations. He continues to produce seminars, videos, books, and online training for the trade as well as contribute monthly Code content to EC&M magazine.