Make Your Electrical Maintenance Work Meaningful
At a paper mill, a newly minted plant manager with little real world experience freaked out when he saw a machinist calmly standing with coffee cup in hand and watching a machine that wasn’t having any problems. While on his way to corral the apparently negligent maintenance manager, he noticed one electrician sitting in front of a cabinet reading a book and another electrician, no tools in hand, chatting with an operator.
After unloading on the maintenance manager about these idle workers and issuing the appropriate threats to give people something to do or else, the plant manager did not get the response he expected. Instead of rushing out to crack the whip, the maintenance manager shared three thoughts:
- The last thing you want is a busy machinist. That situation means we are in serious trouble. It’s good that he’s watching that equipment. Are you aware that both of our machinists have, by doing this, provided ideas that we have acted upon to reduce breakdowns?
- I’d lay odds the first electrician was reading a technical manual. We hammer it into people that if they don’t know what they are doing, don’t do anything. Yes, we have training and procedures, but we cannot leave out the in-depth knowledge that comes from reading the manufacturer’s manual.
- We assign people to specific equipment. It is their job to understand the theory of operation, what normal operation looks like, and what issues the operator encounters. I suppose we could keep them too busy to learn these things until the equipment is actually down. But with our approach, they can respond to downtime with this learning already completed.
This maintenance manager was differentiating between being busy and being effective. His organization practices a concept that is sometimes called “purposeful idleness.” It isn’t idleness per se, but it is a concept that replaces busy work with work that supports a mission.
Work that is done merely for doing work lacks meaning. It’s demotivating. Some effects of this:
- People disengage. They hate their jobs and are often elsewhere mentally.
- People “quit in place.” Rather than strive for excellence or have an interest in what they are doing, they try to get by with the minimum or less.
- People outright quit.
- Insight, input, and innovation tend to range between rare and non-existent.
Work that is meaningful and for which employees take ownership of is motivating. Some effects of this include:
- People fully engage. They love their jobs, and this shows in the sheer energy they bring to it. They are fully into their work and are usually thinking of how to do it better.
- People not only strive for excellence but think of themselves as giving 110%. Then they often dig deeper.
- Not only do people tend to stay, they also tend not to complain.
- Insight, input, and innovation occur in ways both large and small.
Some ways to make work more meaningful and people more effective:
- Automate the boring tasks, such as routine vibration measurements.
- Purchase the test equipment, safety gear, and materials that people need to do their jobs well. Any lack of support here will communicate that neither they nor their work are very important.
- Assign specific people to specific processes or equipment. Encourage them to become subject matter experts on those. Provide a pathway, and support the effort.
- Don’t communicate the expectation that people must stay busy. Communicate the expectation that they must become as effective as possible.
- Frequently repeat the concept that the plant’s customers do not pay for busywork — they pay for quality product that is delivered on time. That is the mission everyone must support, not the mission of occupying the available time with simply staying busy.
- Reward people for providing insight that proves useful, helping to move an insight from mere observation to reality, providing thoughtful and useful input, and for innovating in ways that improve safety, efficiency, or quality. Rewards can vary from specific acknowledgement to monetary and can include things, such as being flexible with schedules to accommodate personal goals such as attending the grandson’s Little League Championship Game. If employees are innovating in the plant, management can also innovate in the administration.
- Praise in public, but criticize in private.
- Acknowledge problems, but focus on solutions.
- Give the benefit of the doubt. If you see something that appears to be wrongdoing, don’t assume it is. Ask the employee to explain. Rather than ask, “Why are you sitting there doing nothing?” ask, “What are you thinking about?”
- But don’t tolerate obviously bad behavior. Things like horseplay or sabotage must be dealt with immediately and decisively. This is part of creating a desirable workplace for the other employees.
- Never disparage employees or the company. The former violates a social contract and destroys trust. The latter violates your employment contract (whether this aspect is implied or explicit) and can destroy your career.
- Be relentless about safety. Some employees may chafe, but this is the single most effective way to show you actually care about the people who work for you.
About the Author
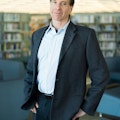
Mark Lamendola
Mark is an expert in maintenance management, having racked up an impressive track record during his time working in the field. He also has extensive knowledge of, and practical expertise with, the National Electrical Code (NEC). Through his consulting business, he provides articles and training materials on electrical topics, specializing in making difficult subjects easy to understand and focusing on the practical aspects of electrical work.
Prior to starting his own business, Mark served as the Technical Editor on EC&M for six years, worked three years in nuclear maintenance, six years as a contract project engineer/project manager, three years as a systems engineer, and three years in plant maintenance management.
Mark earned an AAS degree from Rock Valley College, a BSEET from Columbia Pacific University, and an MBA from Lake Erie College. He’s also completed several related certifications over the years and even was formerly licensed as a Master Electrician. He is a Senior Member of the IEEE and past Chairman of the Kansas City Chapters of both the IEEE and the IEEE Computer Society. Mark also served as the program director for, a board member of, and webmaster of, the Midwest Chapter of the 7x24 Exchange. He has also held memberships with the following organizations: NETA, NFPA, International Association of Webmasters, and Institute of Certified Professional Managers.