Maintenance-Related Questions for Critical Equipment
In this scenario, a central Tennessee manufacturing plant had a particular line dedicated to a particular client. Not only was this line the second most profitable in the plant, but this particular client also bought its entire output. That is, the output never exceeded the demand, and the client often asked if more units could be delivered.
When the maintenance manager retired, his replacement was told to ensure this line had the maximum uptime it could have just as his predecessor had done. Not quite understanding what this entailed, he reviewed the maintenance schedule. He found that task frequencies had greatly been increased. For example, just about every task that should be done quarterly was done monthly. One particular annual task was done monthly, and it required opening an interlocked door which sometimes resulted in an unplanned shutdown because there were not enough techs trained on this particular equipment to go around. Someone junior would be assigned this “simple” task to ensure it got done.
Excessively short intervals do not always result in reduced downtime, but they do result in excessively higher rates of human error. In most plants, “maintenance error” is high on the list of downtime causes. If excessively short intervals somehow extended equipment life, then manufacturers would use excessively short intervals in their maintenance guidelines to avoid warranty claims. But they don’t do that because those intervals introduce risk with no benefit.
That new maintenance manager wrote out a list of questions and answered them. You can also use these questions as a framework for your own critical equipment:
- Are we doing the right maintenance? Some of the maintenance procedures being performed on that special line were not recommended by the manufacturer or any industry standard. Somebody imagined they might help, and so they were added. Doing unnecessary work when time is limited — as it always is for maintenance — results in short-cuts taken with the necessary work.
- Are we doing the maintenance right? As noted with the door interlock problem, this is critical to assess. In this particular case, the new maintenance manager found that motors were being lubricated with incompatible greases. He also found that one tech would adjust a setting one way and another tech would adjust it the opposite way.
- Are we using the right test equipment set to the right settings? Another issue he found was one of the manufacturer’s procedures called for a meter with a given resolution and accuracy and a calibration of no more than two years. But techs were using a variety of DMMS, none of which had ever been sent out for calibration and some of which lacked the necessary accuracy. This meant misadjustment was guaranteed sooner or later and that would result in operation outside specifications.
- Are we assigning the right people to the tasks? This usually translates into whether people are qualified by dint of training. But sometimes it can be a matter of temperament. Not everyone is suited to performing a detailed procedure; some people need time to mature into having the necessary patience.
- Are we creating the right environment? The previous maintenance manager had all maintenance scheduled to take place during breaks and shift changes. Those were not always long enough for the intended task to be correctly performed. And there was never quite enough time to set up the right lighting, run power cords, lay out tools, set up test equipment, etc. before diving into the work.
- Are we supplying the right spare parts, consumables, and other materials needed? This would include such things as identifying which grease goes to which motor and setting up a fool-proof lubrication area in the maintenance shop (e.g., a colored tag system to readily identify each kind of grease).
You may have noticed that all of these questions were addressed to management. And you may have noticed the word “right” was used instead of the phrase “often enough”. Effective maintenance isn’t about doing more of it — effective maintenance is about doing the right things the right way with the right people and the right equipment at the right time.
About the Author
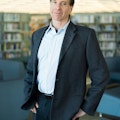
Mark Lamendola
Mark is an expert in maintenance management, having racked up an impressive track record during his time working in the field. He also has extensive knowledge of, and practical expertise with, the National Electrical Code (NEC). Through his consulting business, he provides articles and training materials on electrical topics, specializing in making difficult subjects easy to understand and focusing on the practical aspects of electrical work.
Prior to starting his own business, Mark served as the Technical Editor on EC&M for six years, worked three years in nuclear maintenance, six years as a contract project engineer/project manager, three years as a systems engineer, and three years in plant maintenance management.
Mark earned an AAS degree from Rock Valley College, a BSEET from Columbia Pacific University, and an MBA from Lake Erie College. He’s also completed several related certifications over the years and even was formerly licensed as a Master Electrician. He is a Senior Member of the IEEE and past Chairman of the Kansas City Chapters of both the IEEE and the IEEE Computer Society. Mark also served as the program director for, a board member of, and webmaster of, the Midwest Chapter of the 7x24 Exchange. He has also held memberships with the following organizations: NETA, NFPA, International Association of Webmasters, and Institute of Certified Professional Managers.