Best Practices for Avoiding Equipment Failures
Industrial and commercial facilities often contain self-made booby traps that cause equipment failures, add more work to the maintenance function, and impede the work that maintenance must do. Here are six such booby traps you can disarm with a little extra attention and not much effort.
Inspect EMT
Due to its relatively low cost (and ease) of installation, electrical metallic tubing (EMT) is often the preferred raceway instead of conduit. When assembled properly, EMT reliably protects conductors while also being an excellent equipment grounding conductor (EGC).
But sometimes, EMT is not assemble properly. For example, the connector screws are too tight or not tight enough. Or perhaps, the tubing isn’t inserted far enough because the person who cut the tubing didn’t follow the “measure twice, cut once” axiom or account for the width of the saw blade. So the he “fixes” the short tubing problem by inserting the tubing only partway into the collar. Sometimes the locking nut inside the enclosure wasn’t properly tightened; while a screwdriver can do the job, there are specialty wrenches that ensure the job is done with precision.
Set up a periodic inspection for each discrete area of the plant or circuit by circuit to look for EMT system defects. Make sure you repair them correctly. For example, if a connector is loose, don’t just tighten the screws down. Instead, back each screw out a couple of turns, and apply a thread locker to the now exposed threads. Then tighten the screw until you feel it gently pinch or grab the tubing.
Look for and fix common NEC violations
While NEC compliance doesn’t ensure reliability or optimum performance, certain violations ensure unreliability and poor performance. For example, unsealed “unused openings” are fairly common in plants due to upgrades, retrofits, and equipment moves. The thinking is often that these don’t need to be closed because the operators don’t go near them. But those openings can let in rodents and other pests. In many circumstances, those openings increase the likelihood of the entry of insulation-damaging solvents and oils as well. Close them up.
Another common violation is the “harmless” use of raceway to support some kind of light cable such as speaker cable for a PA system or low voltage wiring for the security system. One job of the raceway is to dissipate heat, so don’t be insulating it with wiring from other systems. Also, that extra wiring adds weight, makes inspection of joints and connections more difficult, and leads to even more wiring being tacked onto the raceway.
Maintain working space
So the operators park a skid within the mandated working distance around equipment. If nobody is working on that equipment, what does it matter? It matters because when someone does go to work on that equipment, there is stuff to move. But move to where? Make the operators decide that by insisting they move the skid (or anything else) to that other location instead of in front of equipment.
Identify “missing” receptacles
Ensure there are receptacles conveniently located near equipment that must be maintained. Convenience here isn’t just a matter of distance, the location must also not be “across the aisle” from where the work must take place. A lamination plant in Tennessee had a complex machine that was responsible for about a fifth of the plant revenue. Every time a maintenance tech performed maintenance or responded to a downtime call, he had to spend time routing portable cords through a maze of machinery. That consumed almost half an hour each time. The additional cost of downtime in a single incident dwarfed the cost of installing receptacles.
Maintain spares
Spare parts are typically “store it and forget it” items. What happens with a motor that sits for five years on a shelf and then is put into service? It’s got old grease and old seals. The shaft hasn’t been turned in five years, and maybe the bearings are stiff. Now you install the spare to replace its counterpart that just failed and shortly thereafter this motor also fails. Many things have a shelf life or expiration date, and long-term storage ensures you’ll be using something that you shouldn’t be using.
If you have a local electrical distributor, let them manage your inventory of consumables. This will help reduce the effects of shelf life. If you have a local motor shop, contact them about possibly pooling with another customer or two of theirs for keeping spare motors. The shop may even agree to keep the spares on hand and conduct the necessary maintenance with two or three plants splitting the bill.
Use the right tool for the job
When an electrician uses a pocket knife to strip the insulation from a conductor, there is almost always damage. The wire gets nicked, the remaining insulation is weak from being overstretched, and the cut is uneven in a way that can interfere with making a good connection. Use a set of self-adjusting wire strippers, and these problems don’t occur. Similarly, use locknut pliers instead of whacking a screwdriver with your lineman’s pliers (those pliers should not be used as a hammer, either). Every workmanship defect that exists due to using the wrong tool to do “good enough” work increases the odds of a failure.
Using the wrong tool is also bad for the tool. For example, using a drill to warble out a hole or debur it using the same bit you just used to drill the hole means you are side-loading the bearings. Do this enough, and that drill will never produce a hole that is true. And using a drill damaged in that way increases the odds the bit will be grabbed due to its eccentric motion and snap; this is dangerous.
About the Author
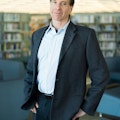
Mark Lamendola
Mark is an expert in maintenance management, having racked up an impressive track record during his time working in the field. He also has extensive knowledge of, and practical expertise with, the National Electrical Code (NEC). Through his consulting business, he provides articles and training materials on electrical topics, specializing in making difficult subjects easy to understand and focusing on the practical aspects of electrical work.
Prior to starting his own business, Mark served as the Technical Editor on EC&M for six years, worked three years in nuclear maintenance, six years as a contract project engineer/project manager, three years as a systems engineer, and three years in plant maintenance management.
Mark earned an AAS degree from Rock Valley College, a BSEET from Columbia Pacific University, and an MBA from Lake Erie College. He’s also completed several related certifications over the years and even was formerly licensed as a Master Electrician. He is a Senior Member of the IEEE and past Chairman of the Kansas City Chapters of both the IEEE and the IEEE Computer Society. Mark also served as the program director for, a board member of, and webmaster of, the Midwest Chapter of the 7x24 Exchange. He has also held memberships with the following organizations: NETA, NFPA, International Association of Webmasters, and Institute of Certified Professional Managers.