Six Tips for Adapting to the Skilled Worker Shortage
Today’s equipment is more complicated than ever, and the skills to maintain it have risen commensurately. This is a problem because the pool of people from which to even teach those skills has shrunk — not only proportionate to the population but also in absolute numbers.
The quick fix of increasing pay to draw skilled workers from a competitor doesn’t work for several reasons, such as there just aren’t enough skilled workers to attract. And you don’t want to get into a hiring war either. However, you also don’t want to underpay your people. Make sure your total compensation (pay, benefits, and perquisites) is competitive and that people are being rewarded in meaningful ways for initiative, outstanding performance, and cost savings they have brought to the company.
Some companies have developed their own training programs, and others are outsourcing that effort to companies that specialize in it. But you can’t produce a qualified maintenance technician in only a few months. Increasing the number of qualified technicians must be done, but it’s a long game. What can you do in the short term? Here are six tips.
- Don’t waste your limited resources. Ensure that jobs are properly planned and coordinated, updated drawings are easy to obtain, and your people aren’t doing favors for other departments. Plan work, and equip people to reduce walking back and forth to the shop. Look at where people’s time goes, and find ways to reduce the drain. Ask them what wastes their time, and take their input seriously.
- Implement monitoring. For every maintenance procedure that includes any sort of manual measurement (e.g., vibration, voltages, temperature, etc.) replace that step with a monitor wherever feasible. Where not feasible, examine the task and the equipment for ways to make the task safer and more efficient (for example, install measurement ports and infrared windows).
- Upgrade hand tools, power tools, and test equipment. Many companies don’t provide hand tools; maintenance people provide their own. This is false economics, but if it’s policy at your company, see what funds you can obtain to provide power tool equivalents where practical. Power tools are usually provided and maintained by the company, but they are usually replaced with models in a similar feature class or price range. You want to look at tools that save time, simplify work, improve safety/ accuracy, or any combination thereof. The advances and improvements in the past few years alone boggle the mind. The same goes for test equipment.
- Optimize your spare parts program. These are typically home grown and not as efficient or cost-effective as they should be. Key spares are often stored improperly or not at all, while items that don’t need to be stored take up room and clutter the system. A firm that specializes in spare parts optimization may reduce inventory cost enough to pay for the firm’s fee. And nothing frustrates a maintenance person more than replacing a bad part with a bad part from the storeroom. If there are many plants in your area, you can probably work something out with your electrical distributor on items such as motors. The distributor may be able to min/max a given motor to cover all the plants.
- Double down on safety. Of course, if a maintenance technician is injured or killed, you will be a person short. But another reason to double down on safety is a safe work style is a methodical work style. A methodical work style often means taking more time upfront to do a job than what is required for a “wing-it” work style. Winging it means mistakes and rework. Thus, this dynamic has given rise to the expression, “Never enough time to do it right, always enough time to do it over.” In some companies, the safety emphasis is on wearing PPE and avoiding specific mistakes (e.g., don’t stand on the top rung of the ladder). The emphasis, however, needs to be on working methodically.
- Listen to people. Exit interviews, polls, and surveys have, for decades, shown the main reason skilled workers leave a company is they don’t feel respected. And that often arises from not being listened to. Attentively listening to another person is a big sign of respect. It makes them feel valued, and it helps create a bond between people. Another reason to listen to people is they have ideas. They are aware of system deficiencies and other issues that need to be addressed. Without their input, management operates at least partially blind.
About the Author
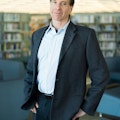
Mark Lamendola
Mark is an expert in maintenance management, having racked up an impressive track record during his time working in the field. He also has extensive knowledge of, and practical expertise with, the National Electrical Code (NEC). Through his consulting business, he provides articles and training materials on electrical topics, specializing in making difficult subjects easy to understand and focusing on the practical aspects of electrical work.
Prior to starting his own business, Mark served as the Technical Editor on EC&M for six years, worked three years in nuclear maintenance, six years as a contract project engineer/project manager, three years as a systems engineer, and three years in plant maintenance management.
Mark earned an AAS degree from Rock Valley College, a BSEET from Columbia Pacific University, and an MBA from Lake Erie College. He’s also completed several related certifications over the years and even was formerly licensed as a Master Electrician. He is a Senior Member of the IEEE and past Chairman of the Kansas City Chapters of both the IEEE and the IEEE Computer Society. Mark also served as the program director for, a board member of, and webmaster of, the Midwest Chapter of the 7x24 Exchange. He has also held memberships with the following organizations: NETA, NFPA, International Association of Webmasters, and Institute of Certified Professional Managers.