Electrical Troubleshooting Quiz — October 3, 2023
About six months ago, Jim was hired as the new plant maintenance manager. You report directly to him. You really like him, and so do your immediate coworkers. He’s a good boss and fair. He listens to your ideas and has good ones of his own. Since Jim started, downtime of the most critical equipment has dropped by more than 90%. However, downtime on some other equipment has risen sharply because he’s given it a lower priority based on discussions he had with operations managers. Consequently, he may have made some enemies in the lower ranks of operations.
He came to you with a problem. The plant manager who hired Jim left the company not long after, and over the past few weeks, his replacement has taken heat for several late shipments. The common point of failure for the various lines in question is a varnishing operation that feeds parts to all of them. It jams up for seemingly no reason, and downstream customers of the process starve for materials.
Jim had solved other problems with this particular operation not long after he started, and downtime decreased dramatically, but the jamming is a new failure mode.
Jim told you all of the PMs have been optimized per engineering analysis and the CMMS shows they are being duly carried out. But the scuttlebutt being relayed to the plant manager is “the new PMs” are actually causing equipment failures. Jim’s in the perfect position to be the scapegoat for the shortfall and could be fired for it. He asked you to figure out why this new problem exists, since there seems to be no technical explanation for it.
How might you get to the bottom of this?
Answer to Quiz. The last thing you want to do is get into a political fight. There are usually no winners in such fights. The plant manager is concerned with solving the late shipment problem, so that needs to be your focus. You already know the PMs are solid and are being performed and that downtime decreased after technical issues were solved. So, this likely is not a maintenance issue. But verify that the PMs are being performed correctly by interviewing the last few techs who performed them and have them walk you through the steps. A dry run would work, but an actual PM would be better.
Next, take the time to understand how that equipment is operated. Interview a couple of operators and get a walk-through, just as you did with the maintenance techs. Try to interview different operators who do the same function, for example by contacting the first and second shift operators on the same work station. Ask them questions, such as what they do if two parts stick together.
A plant in central Tennessee had this very problem. The operators were supposed to use a specially made tool to separate parts that stuck together. It was about the length of a broom handle and had a funny looking contraption on the business end. An operator demonstrated how well this works then commented that you had to wipe the varnish off with a rag after using it, and some people didn’t like doing that. This led to a short conversation in which this operator revealed that another operator swung a metal prybar at the sticking parts and the force of the blow would knock them apart. It would also cause varnish to be flung to places it shouldn’t be flung, and sometimes a part's hook or a part itself would end up getting bent — and thus, more jams. This particular operator had transferred to this department only days before the jamming started.
While the ability to engage operators in a conversation about what they see happening is a valuable troubleshooting skill, it’s not always available. A plastics plant just east of Dallas had a problem with unexplained E-stop activation. Periodically late in the afternoon, somebody would hit an E-stop button, but none of the operators seemed to know who it was. This meant nobody could give maintenance a reason, which meant maintenance had to perform a list of safety checks before resetting the E-stop.
The plant ran on only one shift, so after hours some hidden cameras were installed. There was one pointing at each E-stop. Over the course of several days, two operators were caught on video slapping E-stops, and they each did this multiple times. They had been complaining about the heat, but management did not address the issue to their satisfaction, so they shut equipment down to put less heat into the building.
As in the previous case, there was no problem with the equipment. You could troubleshoot it all day long and not solve the problem. Frustrated people come up with their own “solutions,” and these can cause downtime. When a technical reason has been effectively ruled out, look for a behavior problem. That doesn’t mean to accuse people; it means to listen to them. And if they aren’t speaking, then watch them even if you have to watch them on hidden camera. Note that privacy laws generally prohibit the use of audio in hidden cameras, so either disable audio if it’s available on any cameras you use for this purpose, or don’t conceal the cameras.
About the Author
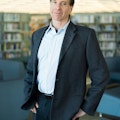
Mark Lamendola
Mark is an expert in maintenance management, having racked up an impressive track record during his time working in the field. He also has extensive knowledge of, and practical expertise with, the National Electrical Code (NEC). Through his consulting business, he provides articles and training materials on electrical topics, specializing in making difficult subjects easy to understand and focusing on the practical aspects of electrical work.
Prior to starting his own business, Mark served as the Technical Editor on EC&M for six years, worked three years in nuclear maintenance, six years as a contract project engineer/project manager, three years as a systems engineer, and three years in plant maintenance management.
Mark earned an AAS degree from Rock Valley College, a BSEET from Columbia Pacific University, and an MBA from Lake Erie College. He’s also completed several related certifications over the years and even was formerly licensed as a Master Electrician. He is a Senior Member of the IEEE and past Chairman of the Kansas City Chapters of both the IEEE and the IEEE Computer Society. Mark also served as the program director for, a board member of, and webmaster of, the Midwest Chapter of the 7x24 Exchange. He has also held memberships with the following organizations: NETA, NFPA, International Association of Webmasters, and Institute of Certified Professional Managers.