Electrical Troubleshooting Quiz — May 2, 2023
The company you work for manufactures its own products. It recently bought a supplier of key components. The idea behind this vertical integration was to better manage production of those components, which were often delivered late. The supplier’s factory is only a short drive from your own, and that was another plus in the decision to integrate.
Now it turns out that one reason for the supplier’s “advantageous pricing” is they didn’t have a professional maintenance operation. There’s no CMMS, and all of the maintenance team came from the production department instead of from the skilled trades.
Your boss, the plant engineer, was shocked to see how much downtime this supplier’s plant incurred. The plant engineer told you, “No wonder they sold it. Our management certainly didn’t do due diligence.” The plant engineer doesn’t want to play reactive maintenance games. Toward that end, he is putting together a proposal to the COO. One part will involve replacing the unqualified maintenance staff with qualified maintenance staff. Another part will involve identifying root causes that can be addressed to dramatically reduce downtime.
How might you efficiently identify several root causes?
Answer to Quiz. When a system has systemic problems, always start with the power supply. This rule applies whether you are troubleshooting a circuit board or an entire plant. If there’s no one-line diagram, you will need to draw one.
Start with a visual inspection of the service switchgear. Look for obvious problems, such as feeder circuits leaving with conductors in different raceways, parallel conductors of different sizes, corrosion of connectors, discoloration of insulation jackets, etc.
Obtain the electrical testing reports of the electrical infrastructure (e.g., breaker testing, feeder cable testing, etc.), if those exist. They probably don’t, in which case an electrical testing firm will need to be brought in to perform those tests after your team addresses what you find in this first pass at the problem. If those do exist, determine what, if any repair actions were taken and fill in any gaps.
Even a small amount of voltage imbalance can cause a large amount of motor failure, so check motor feeders for this issue and fix as needed. A typical fix involves taking all the lighting loads that were connected to a single phase (e.g., Phase B) and spreading them out across all phases.
You can quickly identify dry-type transformers that may be overloaded; they run hot and tend to hum. These will produce power quality issues that cause downtime, so have any hot hummers properly assessed by one of your plant’s electricians.
Undesired circulating current is a major cause of downtime in manufacturing plants. So inspect every piece of production equipment and every large metallic object (e.g., equipment cabinets) for proper bonding. Not “grounding,” but bonding. If you see ground rods driven anywhere in the plant, just consider those red flags for bonding deficiencies and make the necessary corrections.
Check the equipment grounding conductor (EGC) system for electrical continuity and mechanical integrity. One plant with apparent power quality issues had non-metallic connectors in some of its metallic raceways, even though the raceways were used as the EGC. This resulted in differences of potential plus currents flowing through things like motor bearings.
Another plant with apparent power quality issues had some 277V lighting with no neutral wire pulled through the raceway; the ballast neutral had been connected to the EMT instead. Obviously, an electrician would not make this mistake. But an unqualified maintenance person installed the additional lights and believed that neutral and “ground” (the EGC, which isn’t actually ground but is a bonding system) were the same. It’s by sheer luck nobody got killed, but these kinds of mistakes happen in plants where unqualified workers perform the work.
To satisfy the intent of the plant engineer, you need to go through each circuit in the plant and look for gross errors that can cause downtime. After you finish your service switchgear inspection, look at the feeders. Then look at the branch circuits for critical equipment and end with an inspection of the other branch circuits.
A longer range plan is needed to bring this plant up to industry standards, but getting these basics addressed will allow the plant to operate with much more reliability. The plant engineer also needs to get asset numbers on the equipment so it can be included in the CMMS. Asset numbers will also make it easier to make sense of your reported findings, so while you’re doing all of this inspecting assign asset numbers to assets with deficiencies (the other assets can be assigned and tagged later).
About the Author
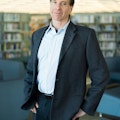
Mark Lamendola
Mark is an expert in maintenance management, having racked up an impressive track record during his time working in the field. He also has extensive knowledge of, and practical expertise with, the National Electrical Code (NEC). Through his consulting business, he provides articles and training materials on electrical topics, specializing in making difficult subjects easy to understand and focusing on the practical aspects of electrical work.
Prior to starting his own business, Mark served as the Technical Editor on EC&M for six years, worked three years in nuclear maintenance, six years as a contract project engineer/project manager, three years as a systems engineer, and three years in plant maintenance management.
Mark earned an AAS degree from Rock Valley College, a BSEET from Columbia Pacific University, and an MBA from Lake Erie College. He’s also completed several related certifications over the years and even was formerly licensed as a Master Electrician. He is a Senior Member of the IEEE and past Chairman of the Kansas City Chapters of both the IEEE and the IEEE Computer Society. Mark also served as the program director for, a board member of, and webmaster of, the Midwest Chapter of the 7x24 Exchange. He has also held memberships with the following organizations: NETA, NFPA, International Association of Webmasters, and Institute of Certified Professional Managers.