Solutions to Maintenance Staffing Shortages
We have an acute shortage of skilled workers in most trades, and the electrical trade is among the hardest hit. The mechanics trade isn’t far behind. These two trades make the core of most maintenance departments.
Adding to the problem, it’s hard to compete for the limited number of qualified people due to such things as corporate budget cutting and salary limitations.
Unless your circumstances are very unusual, you can’t solve the people shortage by hiring the right people to fill the slots that need filling. That is supply-side thinking. What about the demand side?
Here are some things you can do to reduce the demand:
- Automate. Many people think of automation as simply replacing manual labor with machine labor on a direct, one-for-one basis. However, the right automation can reduce manual labor at a far greater ratio. For example, with vibration monitoring on your motors, you can be alerted to conditions that early intervention can correct and, thus, prevent time-consuming motor removal and replacement. It’s not feasible to have someone take vibration readings every minute of every day on large motors, but it is feasible to automate that.
- Focus on root-cause prevention. Systemic power quality problems can overwhelm the maintenance staff with repairs due to failures caused by poor power quality. Consider, for example, what happens when there is voltage imbalance on a few motor feeders. Detecting the imbalance with voltage monitoring allows you to prevent those failures by fixing the imbalance before damage is done. And you can automate the monitoring. Nobody actually saves money by not spending on power monitoring, despite any beliefs to the contrary.
- Train. Even the sharpest among your crew will founder on a problem he’s not trained to handle. Identify the technical tasks that most require training. For example, what systems could fail on your most critical machine or production line? If a line produces half a million dollars per hour in revenue and a properly trained person can correct a downtime cause in 15 minutes instead of an hour and 15 minutes, that is significant.
- Equip. Don’t go cheap on tools. Even small hand tools may offer significant labor savings and error prevention if you purchase the top-of-the-line model instead of something cheap. With power tools, you can expect big savings in labor and work quality by going pro. Test equipment is arguably (and it’s a strong argument) where the right selection can have the biggest effect.
About the Author
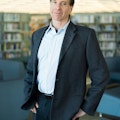
Mark Lamendola
Mark is an expert in maintenance management, having racked up an impressive track record during his time working in the field. He also has extensive knowledge of, and practical expertise with, the National Electrical Code (NEC). Through his consulting business, he provides articles and training materials on electrical topics, specializing in making difficult subjects easy to understand and focusing on the practical aspects of electrical work.
Prior to starting his own business, Mark served as the Technical Editor on EC&M for six years, worked three years in nuclear maintenance, six years as a contract project engineer/project manager, three years as a systems engineer, and three years in plant maintenance management.
Mark earned an AAS degree from Rock Valley College, a BSEET from Columbia Pacific University, and an MBA from Lake Erie College. He’s also completed several related certifications over the years and even was formerly licensed as a Master Electrician. He is a Senior Member of the IEEE and past Chairman of the Kansas City Chapters of both the IEEE and the IEEE Computer Society. Mark also served as the program director for, a board member of, and webmaster of, the Midwest Chapter of the 7x24 Exchange. He has also held memberships with the following organizations: NETA, NFPA, International Association of Webmasters, and Institute of Certified Professional Managers.