What is a maintenance money pig, and why should you care? A money pig is a pool of cost that is big relative to other costs in its category or in general. Suppose you ran a retail store and had 100 units of a slow-moving $200 floor jack. That would be a $20,000 money pig. You’d care because you have $20,000 of capital tied up in this inventory. You need not only to stop buying inventory of this product but also work on converting it to free capital.
For a similar reason, manufacturing plants stopped stockpiling every conceivable spare part and stopped the practice of having N+6 for things that rarely fail or cost a lot of money to stock. Decades ago, plants started sending these money pigs to the proverbial sausage factory. The cost reduction made a big difference in the bottom line. Thus, controlling money pig inventory is a common practice today. You have probably seen this in your own plant.
Another cost that many plants started cutting is maintenance labor. This still happens. It is often in the form of downgrading the labor pool—by forcing out higher-priced, more talented maintenance people and replacing them with lower-priced, less capable people. The result is the maintenance department appears to operate at a lower cost, at least for a while.
It is almost never the case that the maintenance department is cost-bloated due to paying for adequately qualified people, and it is never the case that dropping the average maintenance wage by a few bucks per hour solves a money-pig problem.
Find the real money pigs
In fact, the cost bloat will remain because the real drivers of cost were never addressed. Those drivers are your money pigs, and they are often hidden from view. Some examples:
- Doing project work for other departments. This usually goes on the maintenance department’s budget instead of on the budget of the other department. Even if you call it out as a line item, it’s on your total budget. If the projects had sufficient merit, these departments could get their funding approved by management instead of sneaking the funds from maintenance.
- Unfocused training. Training is essential, but when selections do not serve a clear goal, it is an excess cost. First identify the training needs in terms of meeting specific, revenue-related goals (in addition to training for safety goals). Then identify who should get that training based on who will use it. Don’t try to save money by sending someone from management to training with the idea that person will subsequently train all the maintenance people who need the training. This nearly always fails. The person who does the exact work should get the exact training.
- Unfocused test equipment purchases. A plant in the Midwest had an instrumentation room full of instruments nobody used, but few electricians had an adequately featured digital multimeter. Simply having the latest or greatest isn’t the goal. Buy maintenance techs what they need to do the work safely and efficiently. Part of this also means spending adequately, rather than saving money by getting something that doesn’t really do the job and, thus, doesn’t get used. A plant in the Southeast had four oscilloscopes that were never used, but it didn’t have even a single power analyzer or infrared camera.
- Maintenance done incorrectly. This is how you get breakdowns. A classic example is motor lubrication; there is only one correct way to do this. In many plants, motors are destroyed by mistakes such as lubing with too much grease or using incompatible grease. The result is downtime that makes maintenance look ineffective and like a cost that isn’t doing much good.
- Repairs done with make-do parts or methods. Trying to save money with “good enough” repairs ultimately has the effect of increasing downtime. This downtime often results in paying overtime, a money pig that looks unavoidable until you see why the downtime occurred in the first place.
- Inefficient work practices. If a maintenance tech must make multiple trips to the shop to complete one preventive maintenance or one repair, you are paying that person to walk the floor instead of fixing the equipment. This particular money pig causes a cascade of other costs. Look into things such as PM kits that are stored by equipment distant from the shop and repair kits that are like little service vans but portable. You can find rolling cases to make such kits possible, and those are just one of many fine options.
- Meetings. These are very costly. To make them shorter and more effective, ban the use of PowerPoint and (if they are in-person meetings) have everyone stand up rather than be seated. Establish one or two clear goals ahead of the meeting; when those are met, end the meeting. If you schedule a one-hour meeting, the meeting conversation will expand to fill that time; a goal-based meeting eliminates this problem.
Some plants have an abundance of money pigs. Getting rid of those could not only reduce the cost of maintenance but also reduce unplanned downtime by 90% or more by directing formerly wasted resources toward thorough preventive and predictive maintenance. This increases the revenue side of the equation, reducing pressure from the bean counters to slash costs.
Some plants won’t see such a dramatic improvement in downtime reduction, but they will still see an improvement in the allocation of resources, including a reduction in wasteful spending.
About the Author
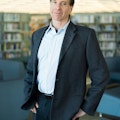
Mark Lamendola
Mark is an expert in maintenance management, having racked up an impressive track record during his time working in the field. He also has extensive knowledge of, and practical expertise with, the National Electrical Code (NEC). Through his consulting business, he provides articles and training materials on electrical topics, specializing in making difficult subjects easy to understand and focusing on the practical aspects of electrical work.
Prior to starting his own business, Mark served as the Technical Editor on EC&M for six years, worked three years in nuclear maintenance, six years as a contract project engineer/project manager, three years as a systems engineer, and three years in plant maintenance management.
Mark earned an AAS degree from Rock Valley College, a BSEET from Columbia Pacific University, and an MBA from Lake Erie College. He’s also completed several related certifications over the years and even was formerly licensed as a Master Electrician. He is a Senior Member of the IEEE and past Chairman of the Kansas City Chapters of both the IEEE and the IEEE Computer Society. Mark also served as the program director for, a board member of, and webmaster of, the Midwest Chapter of the 7x24 Exchange. He has also held memberships with the following organizations: NETA, NFPA, International Association of Webmasters, and Institute of Certified Professional Managers.