An underlying concern of most maintenance seminars, workshops, books, and other forms of training is on how to succeed at maintenance. While this definitely deserves the bulk of your attention if you are involved in maintenance, it’s not the end of the story. It is not a good mindset to always expect success, and in many cases, you should not care if a failure does happen.
Expecting failure
You shouldn’t always expect success because no matter how hard you try to prevent failure, it can and does happen. If you are unprepared for failure, responding to it effectively will be difficult, if not impossible. What happens when something unexpectedly fails in your plant? Do people go into a panic? Does a sort of three-ring circus ensue for the first (and most critical) minutes of the failure?
Our safety practices anticipate failure. For example, we have fall arrest gear. It’s not the primary safety measure, it’s the backup in case of one or more failures of the primary safety measures such as proper securing of scaffolding boards. Another example is in lockout/tagout. You always verify de-energization with a meter, and you always use the double test method (measure where you expect it to be de-energized, then test the meter on an energy source to ensure it’s reading, then measure again).
For your most critical equipment, determine if you have:
- A list of failure modes.
- A written procedure for addressing each failure mode.
- The test equipment, parts, and tools necessary to perform the repair.
- The skill, whether in-house or outsourced, to perform the repair.
Should you fill in all gaps? To answer that, conduct a risk analysis that accounts for both the likelihood and the severity of a given failure mode.
For all other equipment, people need to accept that failures occur. But maintenance needs to prepare for the unexpected by:
- Making sure a rapid response system is in place and everyone knows to use it and how to use it.
- Continually developing skill sets.
- Continually evaluating tools and test equipment, upgrading as needed.
- Refining procedures based on user feedback.
And, of course, maintenance can use monitoring and predictive maintenance to anticipate failure. Seeing the warning signs of, or beginnings of, a failure allows you to deal with it preemptively. Motor vibration monitoring, power monitoring, infrared inspections, and other technologies can significantly reduce your chances of being caught by surprise.
Allowing failure
Should you always care if something fails? That depends on what “something” is. The plant has limited resources for maintenance. If one piece of equipment is responsible for 30% of your plant’s revenue, it should be allocated an outsized share of your maintenance resources. Letting that run to failure is hardly a smart approach.
What about a piece of production equipment that is responsible for 1% of your plant’s revenue and delivery is never critical? If maintenance resources are used to provide quarterly preventive maintenance (PM) on this while there is also a backlog of PMs for equipment of higher revenue value, you are misallocating resources.
If this equipment is expensive to replace, it still might make financial sense to let it fail because you are taking maintenance resources away from equipment that produces far more revenue than this equipment. Raise the question with the production department, being sure to supply them all the numbers they will need from you (replacement cost, opportunity cost lost when other equipment fails, maintenance cost, etc.).
This issue of allowing failure came up at a plant that had just undergone an across-the-board 10% staff reduction in every department (except in HR, which had only two people so had to lay one off to hit the 10% target). Suddenly, there was a very tight pinch in available skilled labor for maintenance. The plant had many of what the plant engineer deemed “discretionary motors,” such as sump pumps, exhaust fans, and automatic door motors. Simply stopping maintenance on these would free up the needed resources for the more critical equipment. All of these motors were allowed to run to failure.
Ideally, the maintenance department would not allow any equipment to fail. But in the real world, it does not have that option. Efforts to go that route anyhow will necessarily impair the ability of maintenance to adequately maintain the most important equipment.
About the Author
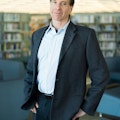
Mark Lamendola
Mark is an expert in maintenance management, having racked up an impressive track record during his time working in the field. He also has extensive knowledge of, and practical expertise with, the National Electrical Code (NEC). Through his consulting business, he provides articles and training materials on electrical topics, specializing in making difficult subjects easy to understand and focusing on the practical aspects of electrical work.
Prior to starting his own business, Mark served as the Technical Editor on EC&M for six years, worked three years in nuclear maintenance, six years as a contract project engineer/project manager, three years as a systems engineer, and three years in plant maintenance management.
Mark earned an AAS degree from Rock Valley College, a BSEET from Columbia Pacific University, and an MBA from Lake Erie College. He’s also completed several related certifications over the years and even was formerly licensed as a Master Electrician. He is a Senior Member of the IEEE and past Chairman of the Kansas City Chapters of both the IEEE and the IEEE Computer Society. Mark also served as the program director for, a board member of, and webmaster of, the Midwest Chapter of the 7x24 Exchange. He has also held memberships with the following organizations: NETA, NFPA, International Association of Webmasters, and Institute of Certified Professional Managers.