The Importance of Normal Operating Conditions
As an electrical professional, what do you think about when performing hazard identification and assessment? Are you looking for potential energy sources, ergonomic hazards, and cut and pinch point hazards? Performing hazard identification and assessments on equipment has become a normal and integral part of business within the electrical industry. Employers teach and continuously train their employees on how to identify hazards and the various ways to mitigate them. But are they performing hazard identification and assessment every time they interact with electrical equipment? Based on the number of occurrences that involve electrical equipment, we must conclude hazards are not always being identified and/or properly mitigated.
Transferring loads, manipulating circuit breakers, and turning equipment on and off are tasks that can be found within normal day-to-day operation. Any interaction with electrical equipment should involve hazard identification, assessment, and mitigation (Photo 1). One critical question that should always be answered before interacting with electrical equipment is: “Is this equipment operating within normal operating conditions?” In addition: “Is the procedure the safest possible available means to accomplish the work?” It seems like it never fails that after an occurrence someone determines there was a safer means available.
All work where the potential for injury exists should include a written procedure that addresses mitigation of all potential hazards. Considering the complexity of today’s electrical power generation and distribution systems and Internet access to manufacturer’s documentation, there is no valid reason not to be familiar with the system. To understand “normal operating condition,” you must understand the requirements in NFPA 70E, Standard for Electrical Safety in the Workplace.
NFPA 70E Sec. 110.4 states, “Normal operation of electric equipment shall be permitted where a normal operating condition exists. A normal operating condition exists when all of the following conditions are satisfied: (1) The equipment is properly installed, (2) The equipment is properly maintained, (3) The equipment is used following instructions included in the listing and labeling and per manufacturer’s instructions, (4) The equipment doors are closed and secured, (5) All equipment covers are in place and secured, (6) There is no evidence of impending failure.” Just as one would do if repairing a system, this criterion must be evaluated before any interaction with equipment to reduce the likelihood of injury or equipment damage.
When troubleshooting electrical equipment, the following are some important factors to consider.
The equipment is properly installed
The manufacturer of the equipment should include mechanical/electrical installation instructions. The installation of your equipment should not only meet the manufacturer’s instructions, but also be installed in compliance with local, state, and federal codes. The equipment has been designed and tested to work in a specific manner, and deviation from this could create unknown hazards.
Note: Not all electrical installations have governmental oversight to verify that the installation is performed within the applicable regulations, codes, and standards. The owner and employer should ensure that the installations are performed as prescribed by the manufacturer to avoid an increased potential for injury.
The equipment is properly maintained
Properly maintaining equipment is a must unless we are willing to place equipment reliability and employee safety in jeopardy. Equipment manufacturers will include instructions with the equipment purchased. These instructions normally contain important information such as equipment operation, alarm recognition, technical specifications, and maintenance actions/intervals. If the maintenance actions are not completed at the intervals set forth by the manufacturer (at minimum), then the equipment must be considered not to be within normal operating condition. See Photo 2, Photo 3, and Photo 4 for examples of the consequences of poor maintenance protocols. Reference NFPA 70E Sec. 205.3 and NFPA 70B, Recommended Practice for Electrical Equipment Maintenance, for further information on the maintaining of electrical equipment.
The equipment is used following instructions included in the listing and labeling and per the manufacturer’s instructions
Within the equipment instructions supplied by the manufacturer is information on how to interact with the equipment. This could include how to perform specific actions and/or personal protective equipment recommended when operating the equipment. Within the instructions may be a requirement stating that only trained and qualified employees should perform specific actions on the equipment. Failure to adhere to these instructions can result in an increased risk to employees.
The equipment doors are closed and secured — and all equipment covers are in place and secured
Properly identifying which doors and/or covers should be closed and secure comes from proper training and manufacturer instructions, as there are some doors/covers that are required to be opened to interact with a circuit breaker or possible logic controls. Through training and understanding of the equipment, one should be able to decide if a door and/or cover is to remain open when interacting with equipment. It is best practice to understand the exposure to shock and arc flash in the making of these decisions (Photo 5).
There is no evidence of impending failure
Determining if equipment has evidence of impending failure isn’t difficult. An employee who is trained and qualified to interact with the equipment should have the knowledge to determine if there is any evidence of impending failure. These signs can be alarms indicating a fault(s), abnormal smells and/or noise, failures downstream indicating potential upstream problems, or even evidence of animal intrusion. Although all the situations that could be present would be impossible to name, a professionally trained and qualified employee should be able to assess the equipment and decide how to proceed — keeping in mind many times the safest procedure is not to proceed.
NFPA 70E Table 130.5(C) states common tasks performed on electrical equipment and the likelihood of occurrence as it pertains to potential arc flash in both AC and DC systems. Within the table is a column for equipment condition. For equipment to meet the normal condition as stated in this table, normal operating condition must be ascertained.
If the time is taken to ensure that equipment is operating as designed by the manufacturer, the reduction of potential risks can be achieved. In doing so, not only do you decrease the risk of equipment damage, but it is also possible to avoid injury and/or save lives. Work on electrical equipment systems typically involves looking for a problem or defect. If so, you need to expect to find one. Electrical equipment is most dangerous when it is not operating properly.
One final note: Troubleshooting is always outside of normal operation. It’s best to adhere to the manufacturers’ warning and turn it off. There are very few troubleshooting procedures that require work on energized equipment.
Joshua Stayton has spent the last 19 years in the electrical industry. As a NFPA Certified Electrical Safety Compliance Professional, Josh currently serves as a safety manager for a Fortune Global 500 company.
A licensed electrical contractor, Bennie Kennedy is a nationally recognized authority on electrical safety and electrical systems with more than 40 years of experience in the electrical industry.
About the Author
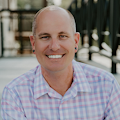
Joshua Stayton
Joshua Stayton has spent the last 19 years in the electrical industry. As a NFPA Certified Electrical Safety Compliance Professional, Josh currently serves as a Safety Manager for a Fortune Global 500 company. [A licensed electrical contractor, Bennie Kennedy is a nationally recognized authority on electrical safety and electrical systems with more than 40 years of experience in the electrical industry.
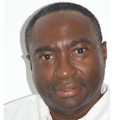
Bennie Kennedy
Licensed electrical contractor Bennie Kennedy is a nationally recognized authority on electrical systems/ safety with more than 40 years of experience in the electrical industry. He has trained and spoken to hundreds of organizations nationally and authored numerous published articles on low- and medium-voltage power distribution systems and safety. He has been authorized by the U.S. Department of Labor OSHA to conduct safety training for more than 20 years. He’s also skilled in electrical equipment failure analysis and occurrence investigation.