Electrical Troubleshooting Quiz — June 1, 2021
A contractor installed a new production machine and left without testing it. The operator has contacted maintenance to say it won’t start.
You arrive and ask the operator to show you what he means. The operator’s control screen functions, so clearly there is power to the system. You ask the operator what should happen when he taps the START button onscreen.
He does that and various pilot lights come on. Then he points to one end and says, “Parts come in here, through these hoppers.” He motions along the machine, describing what each section should do. “And out this end, you get the finished piece. But as you can see, no parts are coming in, and this conveyor isn’t moving even if they did.”
You ask him if there is a simulation mode so you can isolate the problem a bit. There isn’t. How might you solve this?
First, check the drive motor for power. Perhaps the contractor left it locked out or did not connect it. There is probably an interlock that prevents parts from entering if the conveyor isn’t moving; check the control logic. Also look for an interlock that prevents the system from running unless the parts are “loaded” and available to the conveyor.
If the motor has power available to it, then perform a basic function test with the load disconnected to verify the motor will run. If it works, reconnect it.
If there is a parts availability interlock, then check the parts chutes. Do the gates operate, and are there parts on the supply side?
If the machine checks out, next turn your attention to the operator controls. Determine which input(s) and outputs should change at the PLC when the operator pushes START.
About the Author
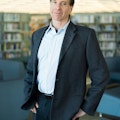
Mark Lamendola
Mark is an expert in maintenance management, having racked up an impressive track record during his time working in the field. He also has extensive knowledge of, and practical expertise with, the National Electrical Code (NEC). Through his consulting business, he provides articles and training materials on electrical topics, specializing in making difficult subjects easy to understand and focusing on the practical aspects of electrical work.
Prior to starting his own business, Mark served as the Technical Editor on EC&M for six years, worked three years in nuclear maintenance, six years as a contract project engineer/project manager, three years as a systems engineer, and three years in plant maintenance management.
Mark earned an AAS degree from Rock Valley College, a BSEET from Columbia Pacific University, and an MBA from Lake Erie College. He’s also completed several related certifications over the years and even was formerly licensed as a Master Electrician. He is a Senior Member of the IEEE and past Chairman of the Kansas City Chapters of both the IEEE and the IEEE Computer Society. Mark also served as the program director for, a board member of, and webmaster of, the Midwest Chapter of the 7x24 Exchange. He has also held memberships with the following organizations: NETA, NFPA, International Association of Webmasters, and Institute of Certified Professional Managers.