Electrical Troubleshooting Quiz — July 21, 2020
You recently hired on as a senior maintenance electrician at a manufacturing plant. You are actually the only senior maintenance electrician at this plant. The other electricians have far less experience than you do.
After several months of enduring process interruptions due to low pressure in the plant air system, the plant installed another air compressor. They located it on the opposite end of the plant from the existing set of air compressors. This happened a few months before you arrived.
During those few months, the new compressor has shut down on overload many times. Changing various settings on the controls has not solved this problem. The plant engineer has asked you to figure out what is wrong electrically — if anything. How do you approach this?
The distance from its supply may be the problem due to voltage drop. If you look at the relationship between voltage, current, and resistance in the formula for calculating power, you see that as voltage decreases, the motor must draw more current, but it’s squared not linear. Excess voltage drop would cause the motor to overheat.
Measure the voltage at the motor. Is the value acceptable for that motor? If not, then you need a different power distribution scheme (larger conductors would be the usual solution), or you need to relocate the compressor closer to its supply after carefully calculating voltage drop for that new location.
Low power factor is the next most likely culprit, with voltage imbalance closely following. Check the motor lead terminations for conductance, also.
Impress your boss by recommending that ultrasonic imaging be done to locate and repair the leaks that are likely the root cause of the low pressure.
About the Author
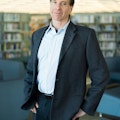
Mark Lamendola
Mark is an expert in maintenance management, having racked up an impressive track record during his time working in the field. He also has extensive knowledge of, and practical expertise with, the National Electrical Code (NEC). Through his consulting business, he provides articles and training materials on electrical topics, specializing in making difficult subjects easy to understand and focusing on the practical aspects of electrical work.
Prior to starting his own business, Mark served as the Technical Editor on EC&M for six years, worked three years in nuclear maintenance, six years as a contract project engineer/project manager, three years as a systems engineer, and three years in plant maintenance management.
Mark earned an AAS degree from Rock Valley College, a BSEET from Columbia Pacific University, and an MBA from Lake Erie College. He’s also completed several related certifications over the years and even was formerly licensed as a Master Electrician. He is a Senior Member of the IEEE and past Chairman of the Kansas City Chapters of both the IEEE and the IEEE Computer Society. Mark also served as the program director for, a board member of, and webmaster of, the Midwest Chapter of the 7x24 Exchange. He has also held memberships with the following organizations: NETA, NFPA, International Association of Webmasters, and Institute of Certified Professional Managers.