On the backshift, Roger had to replace a 50-hp motor. He radioed the stockroom and they said a lift truck driver would bring it up in 30 minutes. Meanwhile, Roger began to remove a troublesome assembly that consisted of heat shield, cooling shroud, ventilation duct, vent fan, and seemingly 1,000 screws. After 20 minutes, Mike arrived to help him.
When the lift truck driver arrived, they hadn’t yet gone to get a lift for pulling the existing motor out because of the time spent on this assembly. The driver offered to set his load down nearby and use his truck to lift the old motor; he had the correct lifting gear with him.
They set the new motor in place, aligned it, and performed rotation testing. They even performed baseline insulation resistance testing before connecting it. But in the meantime, four other trouble calls had come in so Mike left to take those while Roger finished the job.
What are the odds that Roger correctly reassembled this complex cooling system? Slim. Look for ways to simplify reliability equipment so it’s operating correctly after a repair. Use flip locks instead of screws, for example.
About the Author
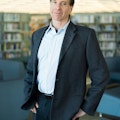
Mark Lamendola
Mark is an expert in maintenance management, having racked up an impressive track record during his time working in the field. He also has extensive knowledge of, and practical expertise with, the National Electrical Code (NEC). Through his consulting business, he provides articles and training materials on electrical topics, specializing in making difficult subjects easy to understand and focusing on the practical aspects of electrical work.
Prior to starting his own business, Mark served as the Technical Editor on EC&M for six years, worked three years in nuclear maintenance, six years as a contract project engineer/project manager, three years as a systems engineer, and three years in plant maintenance management.
Mark earned an AAS degree from Rock Valley College, a BSEET from Columbia Pacific University, and an MBA from Lake Erie College. He’s also completed several related certifications over the years and even was formerly licensed as a Master Electrician. He is a Senior Member of the IEEE and past Chairman of the Kansas City Chapters of both the IEEE and the IEEE Computer Society. Mark also served as the program director for, a board member of, and webmaster of, the Midwest Chapter of the 7x24 Exchange. He has also held memberships with the following organizations: NETA, NFPA, International Association of Webmasters, and Institute of Certified Professional Managers.