The plant air system can’t maintain pressure, so three lines have shut down. Your team troubleshoots and finds that a 100-hp compressor motor has failed.
Your trusty distributor gets a replacement motor on a truck within minutes, and a lift truck driver is sent to your dock to wait for it. Your team goes to work disconnecting and removing the old motor. Even before you get the old motor out of the compressor room, you get a call. The replacement has arrived and will be at the compressor room soon.
Despite the tight space, your crew gets the new motor mounted, shimmed, and bolted in place in under 1 hr. You’ll schedule a laser alignment for the back shift. Two of your team members connect the load, while another one makes the motor lead connections.
Two hours after starting this high-pressure replacement project, you close the disconnect and start the motor. Unfortunately, it has a bent shaft and 2 hr of downtime.
You make a mental note that in the future, someone will always check the motor’s axial runout at the dock.
About the Author
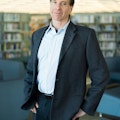
Mark Lamendola
Mark is an expert in maintenance management, having racked up an impressive track record during his time working in the field. He also has extensive knowledge of, and practical expertise with, the National Electrical Code (NEC). Through his consulting business, he provides articles and training materials on electrical topics, specializing in making difficult subjects easy to understand and focusing on the practical aspects of electrical work.
Prior to starting his own business, Mark served as the Technical Editor on EC&M for six years, worked three years in nuclear maintenance, six years as a contract project engineer/project manager, three years as a systems engineer, and three years in plant maintenance management.
Mark earned an AAS degree from Rock Valley College, a BSEET from Columbia Pacific University, and an MBA from Lake Erie College. He’s also completed several related certifications over the years and even was formerly licensed as a Master Electrician. He is a Senior Member of the IEEE and past Chairman of the Kansas City Chapters of both the IEEE and the IEEE Computer Society. Mark also served as the program director for, a board member of, and webmaster of, the Midwest Chapter of the 7x24 Exchange. He has also held memberships with the following organizations: NETA, NFPA, International Association of Webmasters, and Institute of Certified Professional Managers.