You’ve probably heard (and maybe even said) the adage, “Good, fast, cheap. Pick any two, you can’t have all three.” When it comes to repairing equipment that is down, you are usually forced to choose “fast” as one of the two. If you don’t choose “good”, you’re likely to be repairing that equipment again. Yet, cost is also a factor and sometimes it is a very limiting factor.
One way to look at this problem is to set a standard for what constitutes “good” based on a cost/benefit analysis for each type of repair. Of course, that is best done ahead of time rather than while equipment is down.
Another way to look at this problem is you can modify the inputs to these three choices so each one comes at less cost to the other two. For example, you can inexpensively speed up the repair of a critical machine by storing special parts and tools in a locker near the machine. And you can do an upfront investment to increase all three simultaneously: technology, training, and equipment modification are all areas to explore.
About the Author
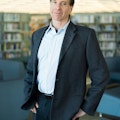
Mark Lamendola
Mark is an expert in maintenance management, having racked up an impressive track record during his time working in the field. He also has extensive knowledge of, and practical expertise with, the National Electrical Code (NEC). Through his consulting business, he provides articles and training materials on electrical topics, specializing in making difficult subjects easy to understand and focusing on the practical aspects of electrical work.
Prior to starting his own business, Mark served as the Technical Editor on EC&M for six years, worked three years in nuclear maintenance, six years as a contract project engineer/project manager, three years as a systems engineer, and three years in plant maintenance management.
Mark earned an AAS degree from Rock Valley College, a BSEET from Columbia Pacific University, and an MBA from Lake Erie College. He’s also completed several related certifications over the years and even was formerly licensed as a Master Electrician. He is a Senior Member of the IEEE and past Chairman of the Kansas City Chapters of both the IEEE and the IEEE Computer Society. Mark also served as the program director for, a board member of, and webmaster of, the Midwest Chapter of the 7x24 Exchange. He has also held memberships with the following organizations: NETA, NFPA, International Association of Webmasters, and Institute of Certified Professional Managers.