Electrical Troubleshooting Quiz — Sept. 4, 2018
Last year, one of the plant’s 15 production lines produced 10% of total revenue and 18% of total profit. Unfortunately, this line has seen frequent interruptions in recent months and orders are often late
The maintenance department responded by creating an “A Team” just for that line, keeping spare parts and special tools in a locker near the line, and other measures that have slashed repair times. The “A Team” has undergone extensive training, including performing mock repairs in a training lab set up to teach them how to perform specific repairs and check their performance for speed and accuracy.
The plant engineer wants the focus to shift to prevention, but all the recommended PMs are being done. Where do you look?
Speed and accuracy are important when repairing critical equipment, but thoroughness is also important, It arguably trumps the other two. Finishing a repair quickly but partially creates a vicious cycle of quickly done partial repairs.
If the “A Team” is not recording the reason code for each repair, have them do so going forward. Monthly, check the reason codes for patterns; not just repeat failures, but also related failures. Based on those findings, implement corrective repair (including equipment modification) and preventive and predictive maintenance.
In parallel with this, look for systemic root causes such as grounding or bonding deficiencies and power anomalies (e.g., with the proper equipment such as power analyzers).
About the Author
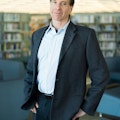
Mark Lamendola
Mark is an expert in maintenance management, having racked up an impressive track record during his time working in the field. He also has extensive knowledge of, and practical expertise with, the National Electrical Code (NEC). Through his consulting business, he provides articles and training materials on electrical topics, specializing in making difficult subjects easy to understand and focusing on the practical aspects of electrical work.
Prior to starting his own business, Mark served as the Technical Editor on EC&M for six years, worked three years in nuclear maintenance, six years as a contract project engineer/project manager, three years as a systems engineer, and three years in plant maintenance management.
Mark earned an AAS degree from Rock Valley College, a BSEET from Columbia Pacific University, and an MBA from Lake Erie College. He’s also completed several related certifications over the years and even was formerly licensed as a Master Electrician. He is a Senior Member of the IEEE and past Chairman of the Kansas City Chapters of both the IEEE and the IEEE Computer Society. Mark also served as the program director for, a board member of, and webmaster of, the Midwest Chapter of the 7x24 Exchange. He has also held memberships with the following organizations: NETA, NFPA, International Association of Webmasters, and Institute of Certified Professional Managers.