Tip of the Week: Six Principles of Effective Maintenance Management
How do you keep your maintenance program on track and yield the best results from your investment? These six principles will help:
1. Plan, rather than react. Focus resources on preventing downtime, not on reacting to downtime you should have prevented. When there’s a failure, determine the cause and figure out how to prevent that cause going forward. For example, motors in the finishing area fail frequently. The cause is a solvent that gets into the windings through the motor vents—so capture and exhaust the solvent, or use totally enclosed motors.
2. Be equipped to do the job. Thinking you can do the best job without the best test equipment, tools, and training is wishful thinking. Thinking you can do any job safely while skimping on safety training, PPE, and an (almost) obsessive safety culture is dangerous thinking.
3. Follow the plan. A plan is won't work if you don’t follow it. Sure, you may need to adjust it and make an occasional exception as exceptional circumstances (and common sense!) may dictate. But don’t stray from the plan just because someone in operations or management yells loudly enough. Always explain the plan, and if someone wants an exception, have them make a logical case for it. For example, all the maintenance for Line 3 is in the CMMS and scheduled for two months from now. But one month from now, this line is being tapped to fill huge orders and operations wants you to do all the PM work now instead of when runtime is so critical. There is only one correct answer and “we’re sticking to the plan” is not it.
4. Actively seek feedback and advice. This is a tough job, and you can’t know everything! Yes, of course get feedback from operators and maintenance people, but go well beyond your immediate surroundings. Good sources include industry publications, industry forums, industry standards, seminars, workshops, classroom training, reference guides, and peers that you network with through industry organizations.
5. Adjust as needed. Getting all that feedback and advice is pointless if you don’t use it when it may make a difference.
6. Keep others in the loop. Don’t just change something “in the back office.” Communicate changes and special activities to those who may be affected. For example, you could email the relevant department heads and supervisors that you’re conducting both a thermographic survey and a power analysis on Area X next Thursday, instead of just the usual voltage checks. Then share with them your findings (just be succinct). They will appreciate being kept in the loop, and you’re showcasing how maintenance is staying on top of things.
About the Author
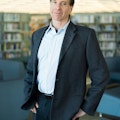
Mark Lamendola
Mark is an expert in maintenance management, having racked up an impressive track record during his time working in the field. He also has extensive knowledge of, and practical expertise with, the National Electrical Code (NEC). Through his consulting business, he provides articles and training materials on electrical topics, specializing in making difficult subjects easy to understand and focusing on the practical aspects of electrical work.
Prior to starting his own business, Mark served as the Technical Editor on EC&M for six years, worked three years in nuclear maintenance, six years as a contract project engineer/project manager, three years as a systems engineer, and three years in plant maintenance management.
Mark earned an AAS degree from Rock Valley College, a BSEET from Columbia Pacific University, and an MBA from Lake Erie College. He’s also completed several related certifications over the years and even was formerly licensed as a Master Electrician. He is a Senior Member of the IEEE and past Chairman of the Kansas City Chapters of both the IEEE and the IEEE Computer Society. Mark also served as the program director for, a board member of, and webmaster of, the Midwest Chapter of the 7x24 Exchange. He has also held memberships with the following organizations: NETA, NFPA, International Association of Webmasters, and Institute of Certified Professional Managers.