To an electrical consulting engineer, the necessity of designing an electrical system that functions per the owner’s requirements, adheres to code, and is constructible is of paramount importance. For the electrical contractor, building off of a set of plans that are clear and coordinated guarantees an efficient and timely installation schedule for the project. As an owner, understanding that a construction project is not meeting basic requirements or learning that a project is delayed due to design deficiencies during construction is a frustrating prospect. So how do you ensure that the electrical engineer’s design minimizes the adverse effects on the contractor’s install, which, in turn, guarantees a better final product for the owner? By establishing that the design job is done right from inception.
This piece will discuss the importance of developing an effective quality assurance and quality checking (QA/QC) process of design documentation to be completed before final documents leave the engineer’s office.
The focus of the QA/QC process
The focus of the QA/QC process is on all aspects of the design, including the review of lighting and power drawings, load calculations, and equipment specifications. In addition, an understanding of the Owner’s Project Requirements (OPR) is also necessary to confirm that the design intent adequately aligns with what the owner expects from the project.
The QA/QC process should confirm that all building standards are followed, particularly when they are unique to the base building in which the owner is a tenant. The process also should ensure that energy-efficiency standards, such as Leadership in Energy Environmental Design (LEED), International Energy Conservation Code (IECC), and/or American Society of Heating, Refrigerating and Air-Conditioning Engineers (ASHRAE) are adhered to as required by the state or city where the project is located. Verification that the system's design is up to the latest building, electrical or fire codes, and/or local jurisdictional amendments pertaining to the project location is yet another necessary focus of the QA/QC process.
Though not implicit in the job description of an electrical engineer, in projects with substantial electrical equipment as well as mechanical and plumbing equipment, constructability of the electrical distribution system must be reviewed. The aim is to confirm that equipment fits within its final location and that the path to install such equipment and other interconnecting pathways is feasible. It is also important that the QA/QC process focus on inter-trade coordination. A review of the different systems that will be occupying the same space as the electrical systems in corridor ceilings or user shafts, for example, should be within the design scope. Confirming that no foreign systems impinge upon the electrical equipment or working clearances should be verified as well. An electric utility coordination effort must be included to ensure that all requirements per utility are met; this might include load metering or monitoring requirements, documentation, submittals, and the like.
In essence, an effective QA/QC process establishes that the design engineer applies sound engineering practices while utilizing industry design standards and applicable guidelines to every project in the firm’s portfolio.
Developing the QA/QC process
The most effective and efficient method of developing a successful QA/QC process is to appoint a team of dedicated QA/QC reviewers who would use standardized methods to assess all drawings. These reviewers should be given ample time before a project is formally issued to make a thorough review of the documents and allow the design engineer to make any subsequent changes.
In collaboration with the appointed reviewer, a formal checklist should be developed that encompasses all aspects of the multi-dimensional QA/QC process. This checklist should be broken out per the various design phases so that the review is directed toward that phase of the design. Items on the checklist might include aesthetic items such as legibility of plans, drawing border information, drawing list, and naming/numbering — to which each item should be checked off upon completion. More technical items like code-required receptacle placement, configuration of circuiting, energy code lighting control, and feeder/panel sizing on risers also should be reviewed for accuracy, as each one of these items contributes substantially to the delivery of a comprehensive set of drawings.
In addition to standard checklist items, the checklist template should accommodate the addition of atypical owner-specific requirements such as electromagnetic interference (EMI) protection of certain spaces or noise-sensitive areas where locating loud equipment should be avoided. A thorough checklist should include items that must be received by the engineer (whether from the architect or the owner), for use in completing whatever phase of design is appropriate — whether it be the schematic design (SD), design development (DD), or construction document (CD) phase. Checklist items that might appear at the SD phase, as well as at the DD and CD phase, might include updated drawing backgrounds, latest appliance schedules, or finalized key decisions on the method of lighting control (see the Checklist below).
Implementing the QA/QC process
After the design engineer has used the checklist to develop her design requirements, the QA/QC reviewer can then begin her review of the documents to ensure they meet all the owner’s requirements and the prevailing codes. The QA/QC reviewer should reference the OPR and the engineer’s Basis of Design (BOD) throughout the review process to double-check that all requests made by the owner are met in the engineer’s documents.
The BOD serves as the overview of the scope of work for the complete electrical systems design and also alerts the reviewer to the mechanical and plumbing systems that will be incorporated into the job. Knowing which types of mechanical equipment will be designed allows the reviewer to understand if emergency systems will be required or if special equipment sizing will be needed as is required for fire pumps or smoke exhaust systems.
The next step is to review a complete set of MEP drawings to confirm coordination between the applicable trades. Such a review might constitute overlaying the mechanical, plumbing, and fire protection drawings over the electrical drawing. Some reviewers manually overlay the drawings one upon the other, while others prefer using software to highlight any existing conflicts between trade drawings. Either method is fine if areas of conflict and/or congestion are clearly identified and subsequently rectified. This step in the process guarantees that there are no conflicts and that clearances and equipment spaces are not impinged upon.
It is important that the QA/QC reviewer examine the specifications sections of the documents provided to ensure that all required sections are included and edited appropriately. Coordination information between the drawings and specifications, such as equipment ratings indicated in both the specifications and on the drawings, should be reviewed for consistency. The specifications should also be reviewed to guarantee that related sections are incorporated within the combined specifications booklet and that the pertinent trades and/or external consultants whose sections are referenced in the electrical specifications are informed of those references. A very necessary but often overlooked section is the testing section of the specifications. This section should be evaluated to verify that all pertinent tests are provided for per the project scope. Where required, it should be verified that commissioning activities are included and that the specifications call for the manufacturer to provide the necessary lodging and travel should witness testing be requested by the owner. Warranty, storage, and handling information regarding equipment should also be clearly detailed so that the OPR requirements are met and that the owner is not liable for any damaged equipment that was improperly stored or mishandled during delivery and/or installation.
Another important aspect of QA/QC implementation is a review of the BOD manufacturer installation information. Are the manufacturer’s specific minimum access spaces and clearance requirements adhered to? Is a clear pathway for installation of equipment and/or its removal during maintenance or replacement provided? Considering the number of different parties involved in the programming of a space, it is not necessarily unusual that specific equipment requirements might go unnoticed until the time of equipment install, thereby adversely affecting both schedule and cost. An effective QA/QC aims to avoid this undesirable outcome.
After all aspects of the project are reviewed, a formal submission of review items should be provided to the design engineer for her action. The review items might be in the form of “markups” on the design drawings and specifications, or they might be a comment sheet with all items collated together. In either case, the design engineer must review the comments and make changes to the drawings as necessary.
In some instances, the reviewer might provide direction with which the engineer need not comply because it conflicts with some more recent information the designer has received. This may also be the case if there is a lack of understanding of the project scope on the part of the reviewer since she was not involved in the design process itself. If such an instance arises, the design engineer should provide the reviewer with an explanation and confirm that no further action is required.
In summary
The intent of the QA/QC process in the design phase of a project is to ensure that the project, the engineer, the firm, and the owner all benefit. By ensuring that a rigorous QA/QC process is maintained, coordinated and constructible documents are ensured while technical knowledge is efficiently delivered to all members of the project team. Another benefit of an effective QA/QC process is a decrease in the number of project change orders developed by the contractor, which, in turn, will lead to an increased number of projects delivered on time and within budget. In this way, the effective implementation of a QA/QC process will go a long way toward more successful projects and the strengthening of the design engineer’s client/owner relationships for the long term.
Pearl Odu, PE, is a senior associate with Kohler Ronan Consulting Engineers in New York. She can be reached at [email protected].
About the Author
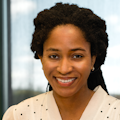
Pearl Odu, P.E.
Ms. Odu has more than 17 years of knowledge and industry experience in the consulting engineer industry and serves as a Senior Associate at Kohler Ronan, LLC in New York. She has a varied portfolio of work ranging from academic institutions, corporate offices, data centers, retail spaces, and private residences. She approaches her work with great care, consideration, and creativity, whether designing innovative electrical systems, managing various projects simultaneously, creating business development opportunities or maintaining valuable client relationships.