Bus bar connections often fail because those making the connections fail to follow the basic rules. Just as often, however, the connections fail even when people do follow the basic rules. Why?
In the early '70s, the EPA came down hard on plating facilities. As a result, the once common plated copper bus bar is no longer what you're likely to encounter. The newer bare bus is not as forgiving as the old plated copper bus. The old assembly techniques are inadequate for ensuring a good connection using today's bus bar. So, an experienced electrician who "does the job right" still may not make a good connection because of additional requirements that didn't exist back when bus had the heavy copper plating.
You must apply two concepts: properly clean and prepare the surfaces and apply sufficient clamping force to ensure good and lasting contact.
So, how do you know if your connection is clean enough? If you have a copper surface and it looks clean, it probably is. This is not true of aluminum, though. Aluminum oxidizes rapidly. In other words, your aluminum bus connector contact surface forms an insulating aluminum oxide film immediately after cleaning. Unless you properly treat the surface, it won't be suitable for connection purposes.
Some treatments, like plating, work quite well. Others, like anodizing, don't. Anodizing, by definition, requires building an oxide film on the surface. If you can tell simply by looking that someone treated your surface for good electrical contact, a non-residual solvent will clean it sufficiently. If the surface has an oxide film or is bare, you need a more strenuous approach to cleaning it. You may use wire brushes; steel wool, fine sandpaper, or a scuff pad, but do so with caution. If you abrade the surface to clean it, make sure the abrasion process does not make the surface uneven. Also, protect the surrounding surfaces from loose particles and clean up thoroughly after abrading. Conductive particles can find their way into insulating systems and wreak havoc later. Similarly, take care not to get insulating material particles into the conductive areas.
If your contact surface is extremely rough, you can use a file to speed up the repair process. However, take care to move the file in the same plane as (parallel to) the surface you are filing (see Fig. 1), so the bar stays true (see Fig. 2). If you aren't careful, you'll get rounded edges and depressions, as shown in Fig. 3. You can avoid distorting the surface if you use light pressure and full strokes, changing the file's horizontal angle frequently. Make sure you keep its vertical angle the same: blade of the file parallel to the surface of the bus bar. File only enough to knock the roughest of the edges off.
Your goal in surface preparation is to produce a flat, clean surface. Before you begin cleaning the surface, obtain a container of electrical joint compound
About the Author
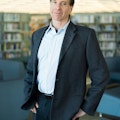
Mark Lamendola
Mark is an expert in maintenance management, having racked up an impressive track record during his time working in the field. He also has extensive knowledge of, and practical expertise with, the National Electrical Code (NEC). Through his consulting business, he provides articles and training materials on electrical topics, specializing in making difficult subjects easy to understand and focusing on the practical aspects of electrical work.
Prior to starting his own business, Mark served as the Technical Editor on EC&M for six years, worked three years in nuclear maintenance, six years as a contract project engineer/project manager, three years as a systems engineer, and three years in plant maintenance management.
Mark earned an AAS degree from Rock Valley College, a BSEET from Columbia Pacific University, and an MBA from Lake Erie College. He’s also completed several related certifications over the years and even was formerly licensed as a Master Electrician. He is a Senior Member of the IEEE and past Chairman of the Kansas City Chapters of both the IEEE and the IEEE Computer Society. Mark also served as the program director for, a board member of, and webmaster of, the Midwest Chapter of the 7x24 Exchange. He has also held memberships with the following organizations: NETA, NFPA, International Association of Webmasters, and Institute of Certified Professional Managers.