Critical Code Requirements for Class II Hazardous Locations
It’s easier to contain dust than gas, so the requirements for Class II locations (ignitable dust) are not as rigorous as those for Class I locations (ignitable gas). However, a dust-based explosion can leave a respectably big crater.
This means you must be rigorous about understanding and applying the requirements for these locations. You also must be rigorous about spotting Art. 502 violations in the project specifications, drawings, and installation practices. Let’s take a look at some Art. 502 violations that can make Class II locations go boom.
Mixing Zone and Division requirements
Use either the Zone [506] or Division system. It’s not à la carte or mix and match because each set of requirements must work as a system, or an otherwise prevented danger will almost certainly be introduced.
But how can this mixing happen? For starters, the electrical engineer on a given project might not have formal NEC training. Such training, if provided, typically covers the basics and doesn’t go into Chapter 5.
The first few Articles of Chapter 5 form a set. To correctly understand and apply any of them, you need to be familiar with several of them. Who gets the training on how these Articles work together as a set?
An engineer who is first confronted with this set of Articles could easily get confused, under the pressure of delivery dates, on Zone versus Division as well as several other important concepts.
What’s the solution? First, obtain from an authoritative source the exact classification of the area. Is it a Class II, Div. 2 location? If so, you can’t apply Class II, Zone 0 requirements. In this case, stop if you see “Zone” mentioned anywhere or if you see any reference to Art. 506. Then investigate to determine what the requirement should actually be.
In short, don’t blindly follow the drawings and other installation documents. Review them to ensure they are consistently applying either Zone or Division methodology.
Related
Critical Code Requirements for Class I Hazardous Locations
NEC Article 501: Class I Hazardous Locations
Confusing Div. I and Div. 2 requirements
This problem is similar to the one just discussed, and the solution is the same. What are some key differences between Div. 1 and Div. 2?
• Tubing is not permitted in Div. 1, but it is permitted in Div. 2 [502.10(A)(1) and (B)(1)]. EMT is great stuff; use it all you want in Div. 2. Just make sure you don’t use it in Div. 1.
• Because Div. 1 raceway must be conduit, the boxes and fittings must be threaded [502.10(A)(3)]. In Div. 2, they just have to be dusttight [502.10(B)(4)].
• Some cabling types (e.g., PLTC) are not permitted in Div. 1 but are permitted in Div. 2.
• If installing nonincendive field wiring in Div. 2, you can use any of the wiring methods permitted for nonclassified locations [502.10(B)(3)].
In addition, the requirements differ for the following types of equipment:
• Receptacles and attachment plugs [502.145].
• Motors and generators [502.125].
• Luminaires [502.130].
• Transformers and capacitors [502.100].
• Switches, breakers, fuses, motor controllers [502.115].
• Utilization equipment [502.135].
Compromising enclosures
When is a dust-ignitionproof enclosure not dust ignitionproof? When you use flexible connectors that are not dusttight [502.10(A)(2(1)]. That’s one of several errors that can stop the enclosure from doing its job. Similar errors can stop a dusttight enclosure from being dusttight anymore.
This raises the question of what the difference is between a dust-ignitionproof enclosure and a dusttight enclosure. The definitions are in 506.2.
• Dusttight enclosures keep dust out under specified conditions; they’re required in Div. 2 locations [502.10(B)(4)].
• Dust-ignitionproof enclosures also keep dust out (under specified conditions). The difference is they also keep ignition sources in; they are required in Div. 1 locations [502.10A(3)].
A dusttight enclosure won’t prevent an arc from traveling from inside the enclosure to some other point; that’s the job of the dust-ignitionproof enclosure.
In April of this year, the project manager of a Class II, Div. 1 project insisted that if an enclosure contains only intrinsically safe equipment then it needs to be only dusttight. That isn’t so simple. While it may apply [504.10(C)], there can be complicating factors [504.10(C) and 504.30].
Cases arise where you must exceed the letter of the Code to satisfy the intent of the Code. That doesn’t mean you exceed the Code just to do so, however. For example, it would be costly to specify dusttight enclosures in unclassified locations. Why would you do so when you’re not required to?
Bad communication
But you can’t have that enclosure in the unclassified area passing dust into your dust-ignitionproof enclosure. How do you prevent the raceway from channeling dust into your dust-ignitionproof enclosure?
The NEC permits four methods of solving this problem [502.15]:
1) Permanent and effective seal.
2) Horizontal raceway at least 10 ft long.
3) Vertical raceway at least 5 ft long and extending downward from the dust-ignitionproof enclosure.
4) Raceway installed in a manner equivalent to either of the two preceding methods and that extends only horizontally and downward from the dust-ignition proof enclosures.
Why not combine two or more of these methods, wherever feasible? Even a seal that is permanent and effective can fail.
Consider a grain facility, which contains plenty of combustible dust and attracts rodents. Anti-rodent measures and infiltration protection are taken seriously at these locations. But those little critters can sometimes show amazing resolve to get past the countermeasures and chew up perfectly good seals. Rather than check off the box that you met one requirement, look for opportunities to create layers of protection — especially low-cost ones.
For example, you’ve got two enclosures spaced 8 ft apart, and only one of them is dust-ignitionproof. Your plant’s engineering guide requires installing seals in all raceway connected to dust-ignitionproof enclosures. You not only seal the raceway, but also “route it the long way around” to give it a horizontal run of 12 ft — a little extra expense over just meeting the requirement.
Improper bonding
Bonding errors can have terrible consequences anywhere, but at least in unclassified locations they generally don’t present the hazard of blowing the place up. That isn’t true for hazardous locations, because a difference of potential (which bonding prevents) can serve as an ignition source.
One misconception is that if you have a very low-voltage system (such as that in an intrinsically safe system), then you don’t have to bond. The fact is bonding is required in any Class II location regardless of the system voltage [502.30].
Your bonding connections can’t rely on locknut-bushing or double-locknut types of contact [502.30(A)]. Instead, use bonding jumpers with approved fittings.
Let’s say your enclosure is bonded via six metallic raceways that carry conductors to or from it. What is providing a mechanically and electrically reliable means of establishing that path from the enclosure to each raceway? Simply assembling the raceway and making sure that locknut is extra tight doesn’t meet the requirement. Installing a bonding jumper in parallel with the locknut/enclosure interface does. You’re jumpering around that interface by installing the bonding jumper.
Ignoring equipment specifics
Article 502 ends with Part III, Equipment. Each Section of Part III provides requirements for a specific type of equipment — for example, motors and generators in 502.125 and receptacles and attachment plugs in 502.145. With the 2014 NEC, the requirements for flexible cords have been greatly expanded [502.140]. So what is all that additional material about?
The addition was mostly a listing of five permitted uses. Suppose you need to provide power to an electric mixer on an open vat. Whether the use of a flexible cord here is permitted or not depends upon whether that mixer is supposed to travel in and out of that vat [502.140(A)(4)]. The flexible cord facilitates this travel, but if there’s no travel, then the need for being flexible isn’t there.
From dust to boom
When working in Class II locations, don’t look for loopholes in the Code that let you “save money” by not doing something that good engineering practice would dictate under the conditions. Instead, first ensure you’ve met Art. 502 requirements. Part of that is going to include making sure every metallic object is properly bonded.
Next, look for possible dust migration or spark communication that conforming to Art. 502 requirements doesn’t totally mitigate. In the unlikely case you find such problems, do what it takes to eliminate them as potential hazards.
Lamendola is an electrical consultant located in Merriam, Kan. He can be reached at [email protected].
About the Author
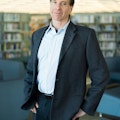
Mark Lamendola
Mark is an expert in maintenance management, having racked up an impressive track record during his time working in the field. He also has extensive knowledge of, and practical expertise with, the National Electrical Code (NEC). Through his consulting business, he provides articles and training materials on electrical topics, specializing in making difficult subjects easy to understand and focusing on the practical aspects of electrical work.
Prior to starting his own business, Mark served as the Technical Editor on EC&M for six years, worked three years in nuclear maintenance, six years as a contract project engineer/project manager, three years as a systems engineer, and three years in plant maintenance management.
Mark earned an AAS degree from Rock Valley College, a BSEET from Columbia Pacific University, and an MBA from Lake Erie College. He’s also completed several related certifications over the years and even was formerly licensed as a Master Electrician. He is a Senior Member of the IEEE and past Chairman of the Kansas City Chapters of both the IEEE and the IEEE Computer Society. Mark also served as the program director for, a board member of, and webmaster of, the Midwest Chapter of the 7x24 Exchange. He has also held memberships with the following organizations: NETA, NFPA, International Association of Webmasters, and Institute of Certified Professional Managers.