Critical Code Requirements for Class I Hazardous Locations
Nothing contained in Art. 501 is unimportant, but some of its requirements may merit extra attention. To make sense of the potential pitfalls and conflicts, begin outside of Art. 501. Specifically, you need to understand what a Class I location is and whether a particular Class I location is a Div. 1 or Div. 2 location.
What Class and Division?
That issue takes us to Art. 500. A location may be Class I, II, or III. Of these, Class I locations have the most stringent requirements. These are locations that contain flammable gas or flammable liquid-produced vapor that is (or may be) present in the air in quantities sufficient to produce explosive or ignitable mixtures [500.5(B)].
The “is (or may be)” is significant. That is not, as some people suppose, the difference between Div. 1 and Div. 2. We’ll address that in a moment. With so many Art. 501 requirements depending upon the Division, getting this right is critical.
Div. 1 is the more stringent of the two divisions. In a Div. 1 location, the gas or vapor is (or may be) present under these conditions:
- During normal operation.
- Frequently due to repair, maintenance, or leakage.
- During equipment breakdown or faulty operation.
This is where people sometimes confuse a Div. 1 with a Div. 2. They assume only the first condition from the list exists. If the gas or vapor isn’t normally present, you might think the less stringent requirements apply. But if the “normally Div. 2 situation” location can “convert” to Div. 1 conditions, it’s a Div. 1.
That conversion is where the “may be” part comes in. People make mistakes, even people who are qualified to classify hazardous locations. Before installing anything in a Div. 2 location, look for proof that it actually is Div. 2. If you don’t find that proof, assume it’s Div. 1 until you get clarification from the person responsible for the classification.
A Div. 2 exists in a Class I location only under the following three conditions [500.5(B)(2)]:
- The liquids, vapors, or gases are confined within closed containers or systems.
- Positive mechanical ventilation prevents “critical mass” accumulation.
- Positive mechanical ventilation prevents spillover from an adjacent Class I, Div. 1 location.
Boxes and fittings
New with the 2014 NEC is the requirement that boxes and fittings be approved for Class I, Div. 1 [501.10(A)(3)].
What about Div. 2? The requirement was carried over verbatim from the 2011 NEC, but a new Informational Note was added with the 2014 revision. The requirement basically states that boxes and fittings don’t have to be explosionproof except as required when you have switches, circuit breakers, fuses, and/or make or break contacts. In such cases, see:
- 501.105(B).
- 501.115(B)(1).
- 501.150(B)(1).
Sealing and drainage
It doesn’t seem logical that the concepts of sealing and drainage go together. Yet, the title of Sec. 501.15 is “Sealing and Draining.” The requirements run for a little more than three full pages, and only about one-eighth of a page is devoted to drainage.
The drainage requirements [501.15(F)] apply in two special cases. Those are where liquid:
- Probably will accumulate in control equipment.
- May accumulate in motors or generators.
In either case, you must provide an approved means for periodic draining. Note the use of the word “periodic,” which excludes the idea of simply leaving a hole for constant drainage.
In the case of the motors, the drainage means must be provided by the manufacturer and considered an integral part of the machine. That means if the motor doesn’t have this means, you can’t just go ahead and add your own drainage device.
If you are expecting the conditions that require drainage, don’t forget your conductors will be in that same environment. This means their insulation must be of a type identified for use under those conditions [501.20].
The sealing requirements are extensive and very detailed, so the likelihood of a Code violation is high. Here’s a tip to help you avoid that. There’s a logical arrangement to the Subsections.
First come the conduit seals. Pick your Division:
- Subsection (A). Conduit seals, Class I, Div. 1.
- Subsection (B). Conduit seals, Class I, Div. 2.
- Subsection (C) applies to seals in both Divisions.
Then we have cable seals:
- Subsection (D). Cable seals, Class I, Div. 1.
- Subsection (E). Cable seals, Class I, Div. 2.
It’s a toss-up as to whether the most common Code violation is improper installation of the seal or the wrong seal for the application in the first place. To ensure sure you get both of these right, read the seal packaging instructions in addition to the requirements in Sec. 501.15.
Related
Grounding and bonding
Confusion on this topic is common, and it frequently results in unsafe installations. One of the results of that confusion is an installation with dangerous differences in potential. When those differences exist in a hazardous location, they can create an ignition source. Even if a plant renovation is long overdue, you really don’t want your installation igniting the vapors in a hazardous location.
So let’s be clear that grounding means a connection to the earth (dirt) [see definitions in Art. 100] and that does not create an equipotential plane because the earth is not a low-impedance path. A metallic path, however, is a low-impedance path. Therefore, it can create an equipotential plane if you connect metallic objects using that metallic path. That’s what Art. 100 means by bonding.
Bonding requirements are contained in Art. 250, Part IV, but you’ll also find specific requirements for Class I, Div. 1 locations in Sec. 501.30. These tell you where, at a minimum, you must add bonding jumpers. Nothing in here stops you from installing bonding jumpers at every place you join two sticks of conduit if you want the extra layer of equipment grounding conductor (EGC) continuity.
Luminaires
Remember, the purpose of an “explosionproof” luminaire isn’t to survive an explosion but to prevent the sparking that can ignite an explosion. Every luminaire used in a Class I location must be listed for the use. If the luminaire is portable, it must be specifically listed as a complete assembly for use in a Class I location [501.130(A)(1) and 501.130(B)(4)].
Pendant luminaires must be suspended by threaded stems of rigid metal conduit or steel intermediate conduit [501.130(A)(3) and 501.130(B)(3)]. If installed in a Class I, Div. 1 location, they must also be supplied by those stems [501.130(A)(3)].
Flexible cords
Somehow, the idea that flexible cords don’t have to meet special requirements sometimes sneaks into hazardous location work. A core philosophy of hazardous location work is that you prevent an explosion by isolating or preventing sources of ignition. The requirements for flexible cords are set out with that in mind.
You know that irritating coworker who twists and tapes flexible cord connections instead of using solderless connectors? Yeah, the guy whose work you’ve had to redo a few times in unclassified locations of the plant. If he does this kind of substandard work in a hazardous location, the sparks that fly won’t be just from arguing with him.
That’s why this workmanship issue is made a safety issue in 501.140(A)(1). The requirement was added with the 2014 Code revision. Not only must you use a proper connector as you should for any installation, but in this case it also must be listed for the protection technique of the equipment wiring compartment.
Whatever flexible cord you use, make sure it [501.140(B)]:
- Is listed for extra-hard usage.
- Contains an EGC.
- Is supported such that there’s no tension on the terminal connections.
- Is installed with a seal, cord connector, or attachment plug listed for the location, if the enclosure or fitting it goes into is required to be explosion-proof.
- Is of continuous length. It it’s too short, don’t splice it; instead, replace it with a longer one.
Preventing violations
It can be hard to keep track of the requirements for Class I locations, as you’re working. One way to prevent problems is to remember why those requirements exist in the first place. They’re mostly there to keep ignition sources and combustible vapors/gases apart from each other. If you think along these lines, the Code requirements almost become confirmation you understand what’s needed. Going at the job from that perspective dramatically reduces the odds of violating a requirement.
Lamendola is an electrical consultant located in Merriam, Kan. He can be reached at [email protected].
About the Author
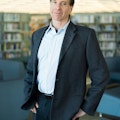
Mark Lamendola
Mark is an expert in maintenance management, having racked up an impressive track record during his time working in the field. He also has extensive knowledge of, and practical expertise with, the National Electrical Code (NEC). Through his consulting business, he provides articles and training materials on electrical topics, specializing in making difficult subjects easy to understand and focusing on the practical aspects of electrical work.
Prior to starting his own business, Mark served as the Technical Editor on EC&M for six years, worked three years in nuclear maintenance, six years as a contract project engineer/project manager, three years as a systems engineer, and three years in plant maintenance management.
Mark earned an AAS degree from Rock Valley College, a BSEET from Columbia Pacific University, and an MBA from Lake Erie College. He’s also completed several related certifications over the years and even was formerly licensed as a Master Electrician. He is a Senior Member of the IEEE and past Chairman of the Kansas City Chapters of both the IEEE and the IEEE Computer Society. Mark also served as the program director for, a board member of, and webmaster of, the Midwest Chapter of the 7x24 Exchange. He has also held memberships with the following organizations: NETA, NFPA, International Association of Webmasters, and Institute of Certified Professional Managers.