Article 506: Class II and III Zone System
We first see the Zone system in Art. 505, which provides this alternative system for Class I locations (the combustibles are gases). The Zones are 0, 1, and 2. But if the combustibles are dust or ignitable fibers (Class II or III), the Zones are 20, 21, and 22 (see Zone System for Class II and III Locations), covered by the requirements in Art. 506.
Documentation
Article 500 provides documentation requirements for Class I, II, and III under the Division system [500.4]. The corresponding Articles (501, 502, and 503) don’t have their own documentation requirements, but the two Zone Articles (505 and 506) do. The documentation requirements for Zones in Class I locations [505.4] are more significant than those for Class II and III [506.4].
Special precaution
Article 505 identifies a “Special Precaution” in 505.7 while Art. 506 does so in 506.6. It’s the same requirement. The equipment construction and installation must “ensure safe performance under conditions of proper use and maintenance.” Unlike Art. 505, Art. 506 doesn’t have an Informational Note requiring special consideration for low ambient temperatures. The other requirements in 505.7 and 506.6 are similar, except:
• 505.7(D) pertains to clearances for flanges.
• 505.7(E) (new with the 2011 NEC) and 506.6(D) (carried over from the 2008 NEC) pertain to the simultaneous presence of flammable gases and combustible dusts or fibers/flyings. These passages should be identical, and they are. The requirement is that you take this simultaneous presence into consideration when selecting and installing the equipment.
• There is no 506.6(E).
Protection techniques
Article 506 provides a list of protection techniques to choose from. Except for intrinsic safety, it’s a different list from the one in Art. 505, because it’s easier to block dust and fibers (Art. 506) than gases (Art. 505).
Don’t be misled because the “intrinsic safety” technique is on both lists. The requirements for intrinsic safety vary with the Class and Zone (or Division), so what’s intrinsically safe for Zone 22 might not be for Zone 0.
For the Class I locations of Art. 505, you can use three of the nine protection techniques in any Zone (the rest are acceptable only for Zones 1 and 2). But for the Class II and III locations of Art. 506, things are different and more complex (Table 1).
Subsection 506.8 lists 10 protection techniques. You can use:
• Any of them for Zone 22.
• All but three (dusttight, nonincendive circuit, and nonincendive equipment) for Zone 21.
• Only three (dust ignitionproof, intrinsic safety, and protection by intrinsic safety “iD”) for Zone 20.
Because intrinsic safety and intrinsic safety “iD” are permissible in all three Zones, it may seem curious that the NEC distinguishes the two. It also does that in Art. 505. The “i” (as in ignition) means any spark or thermal effect is incapable of causing ignition of the combustible. Adding a D (as in dust) distinguishes it from the “i” used in Class I areas [Informational Note in 506.9(C)].
There’s also a subtle difference between “pressurized” and “protected by pressurization (pD).” Each is defined in 506.2. Don’t confuse the two.
Here’s another curiosity. If you compare the 10 protection techniques [506.8(A) through (J)] to the NEC’s Table 506.9(C)(2)(3) [Table 2], it seems something doesn’t add up. But things aren’t always as they appear.
Table 506.9(C)(2)(3) addresses the markings that must be on the equipment, as noted in the text of 506.9(C)(2)(3). The actual techniques are listed in 506.8(A) through (J) and defined in 509.2. There’s more detail to discover on equipment markings, and we’ll get to that shortly.
Equipment requirements
All equipment in Class II or III Zones must comply with five criteria. Upon casual observation, the first three seem like the usual culprits: suitability, listing, and marking. But don’t gloss over these or you’ll be had by some “gotchas.”
What if you want to use equipment in a Zone 21 location but it’s not listed or labeled for use there? One option is to use a testing lab’s evaluation [506.9(A)(2)]. Another alternative is to persuade the AHJ to permit that use.
Helping to simplify your design considerations, the listings are downward compatible [506.9(B)]. For example, if something is listed for Zone 20, you can use it anywhere. If it’s listed for Zone 21, you can also use it in Zone 22.
Marking requirements
The marking requirements are a bit complicated, involving the need to refer to several subsections and a table.
In Zones, you can use equipment that’s marked for Division use but equipment also must be marked Zone 20, 21, or 22 as applicable [506.9(C)]. In addition, it must be marked with its temperature classification per [506.9(D)].
Equipment meeting any of the protection techniques described in 506.8(A) through (J) must be marked with the following items in the order shown:
• Zone.
• Symbol “Ex.”
• Protection technique shown in Table 509(C)(2)(3).
• Temperature classification in Degrees C (preceded by T).
• Ambient temperature marking per 506.9(D).
Threading requirements
The threading requirements are similar to those for Class I locations under the Zone system. For example, threaded fittings must be wrenchtight. But with Class II and III locations, the need to do this doesn’t include ensuring the explosionproof or flameproof integrity of the conduit system.
Any unused openings must be closed with listed metal close-up plugs that comply with 506.9)(E)(1) or (E)(2). In other words, they must be threaded. The difference between (E)(1) and (E)(2) is they apply to National Pipe Thread (NPT) or metric, respectively. Obviously, you’re not going to install a metric plug in a hole threaded for NPT or vice versa.
Wiring methods
At first glance, these look like a headache to comply with, but a closer look reveals it’s not that bad:
• They’re organized by Zone.
• The requirements are downward compatible. Anything that’s permitted for Zone 20 is permitted in the other Zones. If it’s permitted in Zone 21, it’s also permitted in Zone 22.
• For Zone 20, most of the text consists of exceptions.
Each of the permissible wiring methods in Art. 506 has its own article in Chapter 3. For Zone 20, those are generally RMC [344], IMC [342], and Type MI cable [332]. You can use other cable types under specific conditions [506.15(A)(3), (4), and (6)]. Any fittings or boxes must be identified for Zone 20 locations or Class II, Div. 1 locations [506.15(A)(5)].
For Zone 21, you simply follow Zone 20 requirements, except you can use fittings and boxes that are dusttight — but only if they:
• Have threaded bosses for conduit.
• Don’t contain taps, joints, or terminal connections.
• Aren’t used in locations where metal dust is present.
For Zone 22, you follow Zone 21 requirements, except you can:
• Choose from more cable types.
• Use nonincendive field wiring, using any of the wiring methods permitted for unclassified locations.
Seals
Under the Division system, the seal requirements are extensive for Class I locations, light for Class II, and absent for Class III. Under the Zone system, seal requirements are also extensive for Class I. But whether Class II or III, seal requirements may apply. You must provide seals if doing so is necessary to protect the ingress of combustible dust or ignitable fibers/flyings or to maintain the type of protection [506.16].
Grounding and bonding
The requirements for grounding and bonding are nearly the same, regardless of Class, Division, or Zone. Basically:
• All equipment must be bonded to eliminate differences of potential.
• You can’t depend on bushings to maintain the integrity of the bonding path. Jumper around them.
• You can’t depend on the metal jacket of flexible conduit to maintain the integrity of the bonding path. Include a bonding jumper in the conduit.
Staying in the zone
The difficult part of correctly applying the Zone system to Class II and Class III locations is selecting and implementing the appropriate protection technique(s). Read the definitions carefully, as some of these don’t seem different based on the name alone. Make sure any equipment designated “intrinsically safe” carries a listing for the specific Zone you plan to install it in.
Lamendola is an electrical consultant located in Merriam, Kan. He can be reached at [email protected].
SIDEBAR: Zone System for Class II and III Locations
Articles 501, 502, and 503 use the Division system. If combustibles are present under normal conditions, it’s Div. 1. But if combustibles are present only under abnormal conditions, it’s Div. 2 (and the rules are less strict).
Under the Zone system for Class II and Class III locations (Art. 506), if combustible dust or ignitable fibers/flyings are:
• Present continuously or for long periods, they are Zone 20 [506.5(B)(1)] (strictest rules).
• Likely to be present or are frequently (but not continuously) present under conditions, they are Zone 21 [506.5(B)(2)] (moderately strict).
• Present only under abnormal conditions or only for short periods, they are Zone [506.5(B)(3)] (least strict).
About the Author
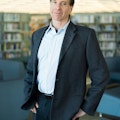
Mark Lamendola
Mark is an expert in maintenance management, having racked up an impressive track record during his time working in the field. He also has extensive knowledge of, and practical expertise with, the National Electrical Code (NEC). Through his consulting business, he provides articles and training materials on electrical topics, specializing in making difficult subjects easy to understand and focusing on the practical aspects of electrical work.
Prior to starting his own business, Mark served as the Technical Editor on EC&M for six years, worked three years in nuclear maintenance, six years as a contract project engineer/project manager, three years as a systems engineer, and three years in plant maintenance management.
Mark earned an AAS degree from Rock Valley College, a BSEET from Columbia Pacific University, and an MBA from Lake Erie College. He’s also completed several related certifications over the years and even was formerly licensed as a Master Electrician. He is a Senior Member of the IEEE and past Chairman of the Kansas City Chapters of both the IEEE and the IEEE Computer Society. Mark also served as the program director for, a board member of, and webmaster of, the Midwest Chapter of the 7x24 Exchange. He has also held memberships with the following organizations: NETA, NFPA, International Association of Webmasters, and Institute of Certified Professional Managers.