Training and certification are good. In fact, they are essential to success. Any electrical contractor or maintenance department that tries to save money here ultimately underperforms.
Yet, you don’t want to put all of your eggs in the technical training basket. Another tool set that’s very powerful is the one called thinking. Ask 10 people at random if they’ve had formal training in thinking, and probably all 10 will say no (at least, I think so).
People who can logically and methodically think their way through problems tend to solve them. People who lack this ability will try other means. They may mischaracterize the problem just so it fits a solution they already have. They may brute force their way through it, or perhaps they’ll just ignore it so that it festers into a mess that can’t be cleaned up.
Many types of thinking methodologies or systems, such as critical thinking, exist. They differ, but they all give you a framework for thinking in an organized fashion. And you’ve probably heard of Six Sigma and of The Five Whys. Each of these relies on structured thinking.
Not that all of these are the same, but if you just pick one and go with it, you really can’t lose. Put your people through the training, and then make thinking integral to how you do business. You don’t want robots, you want people who take ownership of problems and then develop good solutions to those problems. You also want people who can look at a situation and think of the opportunities it may provide.
Let’s say John is an electrician at your firm, and he regularly does some contract maintenance work at the ABC Company. Bill is the plant engineer at ABC. Bill and John are standing in sight of the loading dock, talking about the PM procedures that John just completed. Suddenly, there’s a loud crash.
Bill says: “Those truck drivers just seem to love hitting the corner of that building. I wish they could drive better.”
John, thinking, looks at the angles involved. He looks at the visual clutter, the grade that’s involved, and the tricks played by the light. Then he says, “Bill, you have to admit that’s a tricky approach for any trucker to take on.”
Bill says: “I’ll grant you that. But why do they have to hit those dumpsters or my building?”
John says: “You don’t have people out there helping the driver navigate up to the dock. I think you need a customized system that will do that job. Something maybe with photo eyes. We can design and install something like that. And we can maintain it, too.”
John just hooked this fish on an automation project that would also add to the maintenance revenue stream. But having been trained to think methodically, he’s not done yet. This was a problem outside. What about inside?
“So, Bill, you like that idea. Let me ask you something. I’ve noticed a lot of dents in the pillars throughout the building. Would those be from lift trucks?”
John just hooked this fish for a plant-wide system! And the maintenance on it. Had he not been trained in thinking, what would his response to Bill have been? “Yeah, those guys are not the above-average drivers you and I are.” Or something to that effect, basically agreeing with Bill’s false premise that the drivers were the problem.
Incorrectly identifying the problem, whether because of a false premise or some other defect in thinking, prevents a solution. In this case, Bill can do nothing about the drivers; so if they are the problem, there is no solution.
But John’s company had all of its electricians complete a course in structured thinking. And John’s company encourages people to think. The course would have been pointless if people weren’t given the opportunity to think on the job and then rewarded for doing so.
Then consider Paul. Safety notes in work procedures in his company used to be very prescriptive, like paint by numbers. When people got hurt, the procedures got updated. Hey, here’s another problem. Let’s add it to the list! But this can go only so far. And it helps create a “Let’s see what we can get by with” mentality as that list grows ever more tiresome to wade through.
Paul influenced the company to go with a different perspective. It called for each employee to take ownership of the safety situation and think it through. This began with asking, “What are the potential dangers and how do I protect myself against them?”
Yes, the safety record dramatically improved. People felt (rightfully so) that safety was their responsibility. They didn’t need to be told what to do or not to do. They used their safety training to think through the situation and effectively guard against all dangers — even the unforeseen dangers that formerly might have been added to a list after the proverbial horse left the barn.
How can you encourage your people to think? To get the answer that’s right for your organization and the people in it, think about that.
About the Author
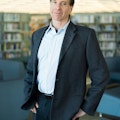
Mark Lamendola
Mark is an expert in maintenance management, having racked up an impressive track record during his time working in the field. He also has extensive knowledge of, and practical expertise with, the National Electrical Code (NEC). Through his consulting business, he provides articles and training materials on electrical topics, specializing in making difficult subjects easy to understand and focusing on the practical aspects of electrical work.
Prior to starting his own business, Mark served as the Technical Editor on EC&M for six years, worked three years in nuclear maintenance, six years as a contract project engineer/project manager, three years as a systems engineer, and three years in plant maintenance management.
Mark earned an AAS degree from Rock Valley College, a BSEET from Columbia Pacific University, and an MBA from Lake Erie College. He’s also completed several related certifications over the years and even was formerly licensed as a Master Electrician. He is a Senior Member of the IEEE and past Chairman of the Kansas City Chapters of both the IEEE and the IEEE Computer Society. Mark also served as the program director for, a board member of, and webmaster of, the Midwest Chapter of the 7x24 Exchange. He has also held memberships with the following organizations: NETA, NFPA, International Association of Webmasters, and Institute of Certified Professional Managers.