Understanding how different job conditions affect total labor hours on any project goes a long way when it comes to successful estimating.
In the article "Let Labor Hours Lead the Way," on page 32L of the June issue, we introduced you to the concept of figuring labor hours and their related costs by two different methods (personal experience or labor-units). Picking up where we left off, it's important to remember there is no specific labor-unit you can apply to every installation every time. So when you estimate labor hours on your next electrical wiring project, you must make adjustments to accommodate varying job conditions. That means taking all of the following job variables into consideration.
Building conditions. It takes much longer to run 100 ft of 3/4-in. EMT in a research laboratory than it does to run it down the wall of an unfinished office. Job complexity can cause confusion. The following examples demonstrate how other simple building characteristics can affect your estimate.
In some areas, an elevator is the only method you have to transport material from the ground floor to the work area. Sometimes, you can only use the elevator during certain hours of the day, or many trades may need to use it at once. If this happens, you must increase your labor-unit for material handling.
If the work area is littered with 4x4s, 2x4s, sheets of plywood, garbage, water, etc, who pays for cleanup? Find out ahead of time, and be sure your contract is clear on this before you begin work.
The height of a building can also have a significant impact on labor productivity. As the number of floors increases, you'll need to figure additional labor-hours to move equipment, material, tools, and personnel to the work area.
You'll also experience a slight decrease in productivity (increased labor unit) when you factor in the time workers will have to wait for lifts at the start of the day, end of the day, breaks, and at lunch. The rule of thumb for single floor adjustment is: If you are working above the third floor, add 1% to the total labor for each floor. Here is an example: If you are remodeling an office building on the ninth floor, increase your total labor by 9%.
Apply the following adjustment factors when estimating the total building labor-hours. These percentages appear low because each floor in the building is similar, and labor productivity increases due to the repetitive nature of the work.
1 to 2 floors +0%
3 to 6 floors +1%
7 to 8 floors +2%
9 to 14 floors +5%
15 to 19 floors +7%
20 to 30 floors +13%
Example: If you are wiring a seven-story building, increase the total labor by 2%.
Note: The National Electrical Contractors Association (NECA) has a 24-page report titled "The Effect of Multi-Story Buildings on Productivity."
Change orders. Jobs are never completed exactly as originally planned. Often, you need to make changes to the electrical system to accommodate changes in building design or the owner's changing needs. Change orders often result in delays, which decrease productivity.
Many times change orders do not affect the planning or scheduling of work, but they often create an unfavorable worker attitude toward the job. There is no specific adjustment for change orders; therefore, you should track your jobs to see if change orders affect your productivity.
Other factors you should consider include: the increased need for management time, interruption of job flow, compressed job schedule, overtime, revisions to as-builds, and possible restocking charges from your suppliers.
Concealed and exposed wiring. There is no labor unit adjustment necessary for electrical wiring in concealed walls or ceilings. However, if you conceal them in concrete or masonry, add the following adjustments: walls +50%; columns +100%.
Making sure enclosures and raceways will be exposed after the building has been completed requires the installation to be aesthetically appealing (nice offsets, raceways installed parallel, and level with the building lines, etc).
You must carefully bend multiple pipes exiting equipment so the raceways are parallel with each other. This takes lots of skill, experience, and time (not to mention wasted material). Here's a quick tip: exposed enclosures +10%; exposed raceways +20%.
Construction schedule. When you prepare an estimate, you generally need to increase labor-units for jobs that take more than a year to complete. Why? Electricians prefer new challenges. Jobs that run for a long time have a tendency to remove the excitement and productivity from the workforce. However, on the flip side, an accelerated job schedule often creates the need for additional employees. Since many of these new workers may be temporary (and they know it), they have a tendency to be less motivated. Naturally, they significantly decrease labor productivity.
Additionally, if you have more electricians on the job than you can manage efficiently, productivity suffers. There is no specific adjustment factor for these conditions, but you need to consider their impact on your labor productivity.
Example: The crew size for a six-week job (estimated to take 1200 hr) would require five electricians: 1200 hr/6 weeks = 200 hr per week/40 hr = 5 electricians.
If you accelerate the job to three weeks, you'll need 10 electricians; and your labor productivity will probably decrease.
Obviously, overtime is always a concern. If the general contractor or owner is unable to properly manage the overall project, you need to make emergency changes to your work schedule. Unexpected schedule changes often require changes in labor workforce, which affects not only the job in question, but other projects as well.
Overtime also interrupts established life patterns and causes fatigue, boredom, and lower productivity. Heavy overtime workers also tend to pay less attention to safety procedures, which can result in serious accidents or fatalities. Consider the following adjustments:
As you can see, overtime makes a big impact on your labor hours. Make sure you have a clear contract regarding who pays for required overtime in the event that the construction schedule changes.
Note: Some good references in this area are available from NECA: the "Project Peak Workforce Report" and "Overtime and Productivity in Electrical Construction."
Labor skill. Some contractors always go for the lowest cost installer. This can be dangerous because low-wage earners typically have less experience and require greater supervision. And don't forget about attitude. When some workers realize their job is almost done, they naturally slow down (decrease labor productivity) to stretch out the work. If you do not have motivated, skilled, and experienced electricians, you'll need to increase supervision in your estimate.
Poorly skilled labor often results in increased costs to correct Code violations and mistakes. This is where training comes in. Improved labor productivity and accidents or injuries easily offset money invested in training.
Ladder and scaffold work. Installations that require a ladder will increase the labor-unit. Use the following adjustments, based on working height, until you develop your own units.
12 ft +3%
13 ft +5%
14 ft +8%
15 ft +10%
16 ft +13%
17 ft +16%
18 ft +19%
19 ft +22%
20 ft +25%
If you need to install equipment from a scaffold, you must add in labor for setting up, moving, and removing the scaffold. Here are a few pointers when it comes to figuring in scaffold considerations: fixed scaffolds +40%, plus labor for pickup, setup, moving, takedown, and return. Motorized scaffolds don't require as much increase in labor.
Project management. Proper job management includes keeping the labor force informed on the project at hand, how you plan to accomplish the work, and how much time you estimate it will take to complete the job. Similarly, an organized and efficient electrical contractor makes sure all workers have the proper tools, materials, and skills to complete the task efficiently.
If your workforce is properly trained, given the tools to complete the task, and motivated by management, they will give their best and perform better. Improper job management often leads to emergency ordering of material and tools or changes in labor scheduling - all of which result in lost productivity. A poorly managed job is probably the leading cause of labor overruns. That's why planning your material orders is so critical. Most of us have worked jobs where we waited for the shop or supplier to get the material to the job. Planning the delivery of material to the job is vitally important to the success of completing the job within budget.
Remodeling. If you're working in an existing building and trying to fish-in wire or cut-in boxes, the adjustment for increased labor costs might be as much as 200%. The only way you can get a feel on this factor (with any degree of confidence) is to actually complete a remodel job and track the labor costs for future reference. Once you have some experience, you will be better prepared to adjust the labor costs for the next remodel job.
Repetitive factor. When you perform the same function repeatedly, you can significantly improve your labor productivity. Consider the following labor adjustment suggestions:
1 to 2 repeats 10%
3 to 5 repeats 115%
6 to 10 repeats 125%
11 to 15 repeats 135%
16+ repeats 145%
Note: These adjustments apply if you are connecting 25 identical AC compressors at one time or wiring 25 identical panelboards.
Teamwork. The general contractor's lack of coordination with the other trades can decrease your labor productivity. If the GC does not coordinate effectively, it is going to cause everyone problems and money.
When stress exists between the trades, expect problems and reduced labor productivity. Labor is often more efficient on jobs where all of the trades interact and are willing to help each other. When possible, try to stimulate and encourage positive teamwork habits between the trades.
Some contractors improve productivity by simply giving the job supervisor a bonus if he or she completes the job in less than the budgeted (estimate) hours. Similarly, successful electrical contractors have some form of incentive or reward system for the employees who complete projects on time within budget.
Temperature. Optimum labor efficiency is achieved when the ambient temperature is between 40øF and 70øF, with the relative humidity below 80%. Studies have shown that extreme temperatures can lead to an increase in accidents, deterioration in workmanship, and lower labor productivity. Although studies indicate humidity has a small impact on labor productivity, I do not agree. Rain can ruin an otherwise productive day, water runoff can destroy all of your work in a ground floor slab, and water entering the building can reduce the interior production to a standstill.
Note: NECA offers a 32-page report titled "The Effect of Temperature on Productivity."
As you can see, so many factors can impact the productivity of your team - some within your control and some beyond. However, planning for and identifying these factors ahead of time will help you hit the mark on your labor estimates every time. Sure, no two electrical contractors will have the exact same labor-unit productivity on any given job. But the more you do it, the better you'll become.
About the Author
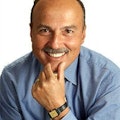
Mike Holt
Mike Holt is the owner of Mike Holt Enterprises (www.MikeHolt.com), one of the largest electrical publishers in the United States. He earned a master's degree in the Business Administration Program (MBA) from the University of Miami. He earned his reputation as a National Electrical Code (NEC) expert by working his way up through the electrical trade. Formally a construction editor for two different trade publications, Mike started his career as an apprentice electrician and eventually became a master electrician, an electrical inspector, a contractor, and an educator. Mike has taught more than 1,000 classes on 30 different electrical-related subjects — ranging from alarm installations to exam preparation and voltage drop calculations. He continues to produce seminars, videos, books, and online training for the trade as well as contribute monthly Code content to EC&M magazine.