When a facility has more than one power source, what must you do to maintain a safe operation? Article 705 answers that and other questions related to using power sources that operate in parallel with a primary source.
Though the primary source is typically the electric utility supply, it can be an on-site source instead. For example, the primary source can be a fuel cell, gas turbine, photovoltaic system, or wind system. It can even be a hybrid system, as defined by 705.2.
This definition doesn’t recognize energy storage systems (e.g., batteries, flywheels) as power sources for the purposes of Art. 705. However, these sources are recognized as power sources elsewhere in the NEC. Thus, Art. 705 requires you to install a permanent plaque or directory denoting all electric power sources on the premises — even those that don’t fall under Art. 705. You must install such a plaque at each service equipment location and at all interconnected electric power production sources [705.10].
Connecting
You can connect an electrical power production source to the supply side of the service disconnecting means per 230.82(6), as shown in Fig. 1. This connection is required for facilities incorporating ground fault protection of equipment [705.12(D)].
When determining the number of disconnects per service per 230.71(A), don’t count photovoltaic system (PVS) disconnect(s) connected on the supply side of service equipment. A PVS disconnect is not a service disconnect as defined in Art. 100. PVS Connections provides advice on photovoltaic power source connections.
You can connect the output of a utility-interactive inverter to the load side of the service disconnecting means at any distribution equipment on the premises [705.12(D)].
Multiple circuits and inverters
The following rules apply to the interconnecting provisions for the electric utility-interactive inverter(s) where distribution equipment is capable of supplying multiple branch circuits or feeders.
Each inverter circuit must terminate to a dedicated circuit breaker or fusible disconnect [690.64]. This requirement, however, doesn’t apply to micro-inverters. All micro-inverters of a string must connect to a single breaker per the listed instructions [110.3(B)].
The sum of the ampere rating of the inverter overcurrent devices and panelboard overcurrent device must not exceed 120% of the panelboard bus ampere rating.
To illustrate the application of this rule, let’s work a sample problem.
What’s the maximum ampere rating of the dedicated inverter overcurrent device for a 200A bus panelboard that’s capable of supplying multiple feeder circuits supplied by 4/0 AWG aluminum rated 180A at 75°C?
Maximum Inverter OCPD = panelboard bus ampere × 1.20, less panelboard OCPD
Example: 150A panelboard
Max. inverter device = (200A × 1.20) – 150A
Max. inverter device = 240A – 150A
Max. inverter device = 90A
Example: 175A panelboard
Max. inverter device = (200A × 1.20) – 175A
Max. inverter device = 240A – 175A
Max. inverter device = 65A
Example: 200A panelboard (see Fig. 2)
Max. inverter device = (200A × 1.20) – 200A
Max. inverter device = 240A - 200A
Max. inverter device = 40A [two 30A inverter circuits would exceed the 40A maximum current limit]
The “not exceed 120% of the panelboard bus ampere rating” rule [705.12(D)(2)] applies only to distribution equipment that is capable of supplying multiple branch circuits or feeders (or both).
For example, a 225A bus panelboard protected by a 225A main circuit breaker could have four 50A inverter overcurrent protection devices, if those breakers fill all slots in the panelboard, as shown in Fig. 3.
But, there’s an exception. Where a PVS has energy storage for stand-alone operation, the value used in the calculation of bus or conductor loading is 125% of the output inverter current.
Panelboards containing AC inverter circuit breakers must be field-marked to indicate the presence of multiple AC power sources. The label must:
• Resist the environment for 25 to 40 years of system use.
• Be suitable for the environment.
• Be installed so as not to void the equipment listing [110.3(B)].
Conductors from the AC inverter can backfeed dedicated circuit breakers that aren’t marked “line” and “load.”
Dedicated AC inverter circuit breakers that are backfed don’t have to be secured in place by an additional fastener as required by 408.36(D). But note that once the dedicated AC inverter circuit breaker has been removed from the panelboard, the listed interactive inverter automatically powers down. It turns off output AC power from the inverter.
Where distribution equipment is capable of supplying multiple branch circuits or feeders, locate the AC inverter circuit breaker at the opposite end from the input feeder supply conductors.
Where distribution equipment is capable of supplying multiple branch circuits or feeders, install a permanent warning label on the panelboard to warn that the inverter output connection circuit breaker must not be relocated.
Source loss
Upon loss of electric utility source power, an electric power production source must be automatically disconnected from all ungrounded conductors of the utility source. And it must not reconnect until the electric utility source has been restored [705.40]. However, there’s an exception. A listed utility-interactive inverter can automatically cease exporting power upon loss of electric utility source power. It isn’t required to automatically disconnect all ungrounded conductors from the electric utility source power. A listed utility-interactive inverter can automatically resume exporting power to the electric utility source once the utility source has been restored.
Utility-interactive inverters
A key concept from Part II of Art. 705 is that single-phase inverters connected to a 3-phase primary power source must not significantly increase unbalanced system voltage [705.100], as shown in Fig. 4. But why does it matter?
At a voltage imbalance of 5%, the motor runs 50% hotter. A voltage imbalance of only 2% reduces motor life enough that it can void the motor warranty.
As PVS installations are becoming increasingly common, let’s walk through a sample installation challenge of such a system. We’ll be using the NEMA formula for maximum unbalanced voltage Vmu = (100 × Dmax) ÷ Vavg.
• Vavg is the average voltage (add all three, divide by three).
• Dmax is the maximum deviation from average (the voltage furthest away from the average, whether greater or less than the average).
We want to add a PVS to the existing system. The existing system’s line voltages are: A to B, 206V; B to C, 200V; and A to C, 204V. What’s the maximum unbalanced system voltage at the electrical service?
Average voltage = (206V + 200V + 204V) ÷ 3 lines = 203.33V
Maximum deviation from average = 203.33V – 200V = 3.33V
Maximum unbalanced voltage = (100 × 3.33V) ÷ 203.33V = 1.64%
Maybe we should place the PVS inverters at lines A to B. Doing so results in voltages of: A to B, 208V; B to C, 200V; and A to C, 204V. What’s the maximum unbalanced system voltage at the electrical service now?
Average voltage = (208V + 200V + 204V) ÷ 3 lines = 204V
Maximum deviation from average = 208V - 204V = 4V
Maximum Unbalanced Voltage = (100 x 4V) ÷ 204V = 1.96%
Oops! Placing those inverters between lines A to B increases the maximum unbalanced voltage by almost 20% — so we don’t want to do that.
If we connect two single-phase PV systems to lines B to C, we have the proper connection. It results in voltages of: A to B, 206V; B to C, 202V; and A to C, 204V.
What’s the calculated maximum unbalanced system voltage at the electrical service?
Average voltage = (206V + 202V + 204V) ÷ 3 lines = 204V
Maximum deviation from average = 206V – 204V = 2V
Maximum unbalanced voltage = (100 × 2V) ÷ 204V = 0.98%
Placing the two inverters between lines B to C significantly decreased the maximum unbalanced voltage, rather than increasing it as the other arrangement did.
Avoiding mistakes
When applying the requirements of Art. 705, remember that its focus is on identifying and properly connecting interconnecting power sources. It doesn’t address the requirements for those power sources. However, other Articles do [Table 705.3]. Where using utility-active inverters, follow the requirements of Part II — and make sure you calculate the maximum unbalanced voltage where you’re connecting single-phase inverters to a 3-phase primary power source.
SIDEBAR: PVS Connections
The following are suggested best practices for a photovoltaic system (PVS):
• Bond the grounded conductor (typically the neutral) on the supply-side of PVS service equipment to the PV disconnect per 250.24.
• Bond raceways containing PVS supply-side service equipment conductors per 250.92(B).
• Limit your wiring methods for the supply-side of PVS service equipment to those identified in 230.43.
• For line-side of service equipment connection, don’t let the sum of the ratings of all PVS system overcurrent devices exceed the ampere rating of the service.
• For load-side of service equipment connection of PVS, the sum of the ampere rating of the PV and service overcurrent device can exceed the ampere rating of the service [705.12(D)].
About the Author
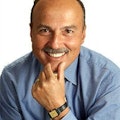
Mike Holt
Mike Holt is the owner of Mike Holt Enterprises (www.MikeHolt.com), one of the largest electrical publishers in the United States. He earned a master's degree in the Business Administration Program (MBA) from the University of Miami. He earned his reputation as a National Electrical Code (NEC) expert by working his way up through the electrical trade. Formally a construction editor for two different trade publications, Mike started his career as an apprentice electrician and eventually became a master electrician, an electrical inspector, a contractor, and an educator. Mike has taught more than 1,000 classes on 30 different electrical-related subjects — ranging from alarm installations to exam preparation and voltage drop calculations. He continues to produce seminars, videos, books, and online training for the trade as well as contribute monthly Code content to EC&M magazine.