The NEC provides minimum size requirements for conductors to prevent overheating and fire. Insulation type, ambient temperature, and conductor bundling are three primary factors in determining how big a conductor has to be for it to safely carry the current imposed on it.
A key concept in conductor sizing is understanding the definition of ampacity. The ampacity of a conductor is the amount of current the conductor can carry continuously under specific conditions of use [Art. 100 definition]. The ampacity of a conductor is not what size breaker can be used to protect the wire; it is simply the amount of current the conductor can carry. It is important to recognize this subtlety.
Temperature correction
Table 310.16 lists ampacities under two conditions: 1) no more than three current-carrying conductors bundled together, and 2) an ambient temperature of 86°F (30°C). If either of these two values changes, the ampacity of the conductor must change as well. If you look at the bottom of Table 310.16, you'll see temperature correction factors in 5°C increments from 21°C through 80°C.
When sizing conductors, you can't use a temperature rating any higher than the lowest temperature rating of any connected termination or device [110.14(C)]. Generally, you don't find terminals rated above 75°C, so why is there a 90°C column for conductors? True, most terminations simply aren't rated to carry 90°C, but remember that when you adjust the ampacity of a conductor due to ambient temperature or conductor bundling, you use the 90°C column to begin the calculation (assuming you are using a conductor 90°C insulation rating). Read through example D3(a) in Annex D, and you'll understand exactly why this column exists.
Use the conductor ampacity as listed in Table 310.16, and apply temperature adjustment factors based on the insulation rating of the conductor. Do not base conductor ampacity adjustment on the temperature terminal ratings discussed in 110.14(C). Understand that the location (wet, dry, or damp) influences which column ampacity of Table 310.16 to use. You can find this information in Table 310.13(A). For example, notice THHW is a 90°C conductor in a dry location, but it's a 75°C conductor in a wet location.
Let's work an example for practice. What's the minimum size THHN/THWN conductor you can use to supply a 40A noncontinuous load in a dry location, if the conductors pass through an ambient temperature of 100°F (Fig. 1)?
Corrected Ampacity = Table 310.16 Ampacity × Ambient Temperature Correction Factor
For a dry location, use the 90°C column for THHN.
Ambient Temperature Correction Factor for 100°F = 0.91 for THHN
Table 310.16 ampacity for 10 THHN is 40A at 90°C in a dry location
10 THHN = 40A × 0.91 = 36.40A. This is too small for the 40A load.
Table 310.16 ampacity for 8 THHN is 55A at 90°C in a dry location: Use the THHN 90°C column.
8 THHN = 55A × 0.91 = 50A
Therefore, an 8 AWG conductor is the answer to this question.
If this were in a wet location, would 8 THHN/THWN still be adequate?
Table 310.16 ampacity for 8 THWN is 50A at 75°C in a wet location: use the THWN 75°C column.
Ambient Temperature Correction Factor for 100°F = 0.88 for THWN
8 THWN = 50A × 0.88 = 44A
The conductor must have an ampacity of at least 40A, after applying the ambient temperature correction factor, in order to carry the load. In this example, the 8 THHN/THWN has sufficient ampacity after correction in either a wet or dry location. That either/or result is not always the case, so pay attention to the wet/dry question when using conductors with dual-rated insulation types, and use the column that corresponds to the location. In addition, keep in mind that a conductor with a “-2” after its insulation, such as THHN/THWN-2, is rated 90°C in a wet, dry, or damp location[Table 310.13(A)].
What if you have conductors installed in raceways exposed to direct sunlight on or above rooftops? In such cases, add the ambient temperature adjustment in Table 310.15(B)(2)(c) to the outdoor ambient temperature when applying ampacity adjustment correction factors contained in Table 310.16.
Bundling
When conductors are bundled together, they lose some of their ability to dissipate heat. In the NEC, the allowable ampacity starts dropping when four or more current-carrying conductors are bundled together for more than 24 inches [310.15(B)(2)(a)] (Fig. 2).
Be aware that there are five exceptions described in 310.15(B)(2)(a), one of which is for AC or MC cable, which allows up to 20 current-carrying conductors in 12 AWG, 2 or 3 conductor cables without having to adjust the ampacity.
If the ambient temperature is anything but 86°F — and more than three current-carrying conductors are bundled together — adjust the ampacity (listed in Table 310.16) for both conditions.
To make that adjustment, multiply these three numbers together:
- Table 310.16 ampacity
- Temperature correction factor
- Bundling adjustment factor.
Always remember that the higher insulation temperature rating of 90°C rated conductors provides a greater conductor ampacity for use in ampacity adjustment, even though you size those conductors based on the column that corresponds to the temperature listing of the terminals [110.14 (C)(1)]. When correcting or adjusting conductor ampacity, use the temperature insulation rating of the conductor as listed in Table 310.16, not the temperature rating of the terminal [110.14(C)].
If a single length of conductor has two ampacities, use the lower ampacity for the entire circuit [310.15(A)(2)]. An exception applies: If that portion of the conductor with reduced ampacity is not longer than 10 feet and is not longer than 10% of the length of the part of the circuit with the higher ampacity, then you can use the higher ampacity for the entire circuit [310.15(A(2) Ex] (Fig. 3 on page 46).
Current-carrying conductors
Table 310.15(B)(2)(a) adjustment factors apply only when there are more than three current-carrying conductors bundled together. All phase conductors are considered current carrying, but what about other conductors? Here's the rundown:
- Grounding and bonding conductors [310.15(B)(5)]
Grounding and bonding conductors are never considered current carrying. Don't count grounding and bonding conductors when adjusting conductor ampacity for the effects of conductor bundling [310.15(B)(5)]. They do, however, occupy space in the raceway and are included in raceway fill calculations (see Chapter 9, Table 1, Note 3), so you are accounting for their presence. You just aren't counting them as current-carrying conductors.
- 2-wire circuits
The neutral and ungrounded conductors of a 2-wire circuit are considered current carrying.
- Neutral conductor — unbalanced loads [310.15(B)(4)(a)]
A neutral conductor that carries only the unbalanced current from other conductors of the same circuit is not considered a current-carrying conductor (Fig. 4 on page 48).
- Neutral conductor — unbalanced 3-wire wye circuit [310.15(B)(4)(b)]
The neutral conductor of a 3-wire circuit of a 4-wire, 3-phase, wye-connected system carries about the same current as the line-to-neutral load currents of the other conductors. As a result, it's considered a current-carrying conductor.
- Neutral conductor — nonlinear loads [310.15(B)(4)(c)]
The neutral conductor for a 4-wire, 3-phase wye circuit is considered a current-carrying conductor where more than 50% of the load consists of nonlinear loads (Fig. 5).
Nonlinear loads supplied by a 4-wire, 3-phase, 120/208V or 277/480V wye-connected system can produce unwanted and potentially hazardous harmonic currents. Odd triplen harmonic currents (3rd, 9th, 15th, etc.) can add on the neutral conductor. To prevent fire or equipment damage from excessive harmonic neutral current, consider increasing the size of the neutral conductor or installing a separate neutral for each phase. See 210.4(a) FPN, 220.61(C) FPN No. 2, and 450.3 FPN No. 2.
Meeting minimums
From an NEC standpoint, conductors must be of a certain size to prevent a fire [90.1(B)]. This is the minimum conductor size, not necessarily the recommended conductor size. From an operational efficiency standpoint, you should size conductors to reduce voltage drop and/or to cope with nonlinear loads. Other reasons for exceeding NEC minimums may also apply.
If your installation doesn't even meet the NEC requirements, it will fail to meet other requirements that may also exist (such as those for operational efficiency). To prevent that, remember the ampacity of a conductor changes with changing conditions. Part of your job in sizing conductors is to anticipate what those conditions will be. To determine the correct ampacity, you have to determine:
-
Allowable ampacity, as listed in Table 310.16.
-
Ambient temperature correction factors, if the ambient temperature is not 86°F.
-
Conductor ampacity adjustment factors, if four or more current-carrying conductors are bundled together.
The last two items are where things can get dicey if you don't do your homework. Find out what the ambient temperature will be along the entire length of each conductor. Such things as cable routing [see the example in Appendix D3(a)] and ventilation can change ambient temperature considerably, so take the time to review the entire installation — not just the electrical drawings.
If you correctly anticipate the ambient temperatures and perform the necessary ampacity adjustments, then you'll meet the NEC minimums for conductor sizing. From there, you can decide whether to allow for other considerations in making a final determination of conductor size.
About the Author
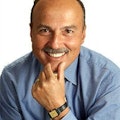
Mike Holt
Mike Holt is the owner of Mike Holt Enterprises (www.MikeHolt.com), one of the largest electrical publishers in the United States. He earned a master's degree in the Business Administration Program (MBA) from the University of Miami. He earned his reputation as a National Electrical Code (NEC) expert by working his way up through the electrical trade. Formally a construction editor for two different trade publications, Mike started his career as an apprentice electrician and eventually became a master electrician, an electrical inspector, a contractor, and an educator. Mike has taught more than 1,000 classes on 30 different electrical-related subjects — ranging from alarm installations to exam preparation and voltage drop calculations. He continues to produce seminars, videos, books, and online training for the trade as well as contribute monthly Code content to EC&M magazine.